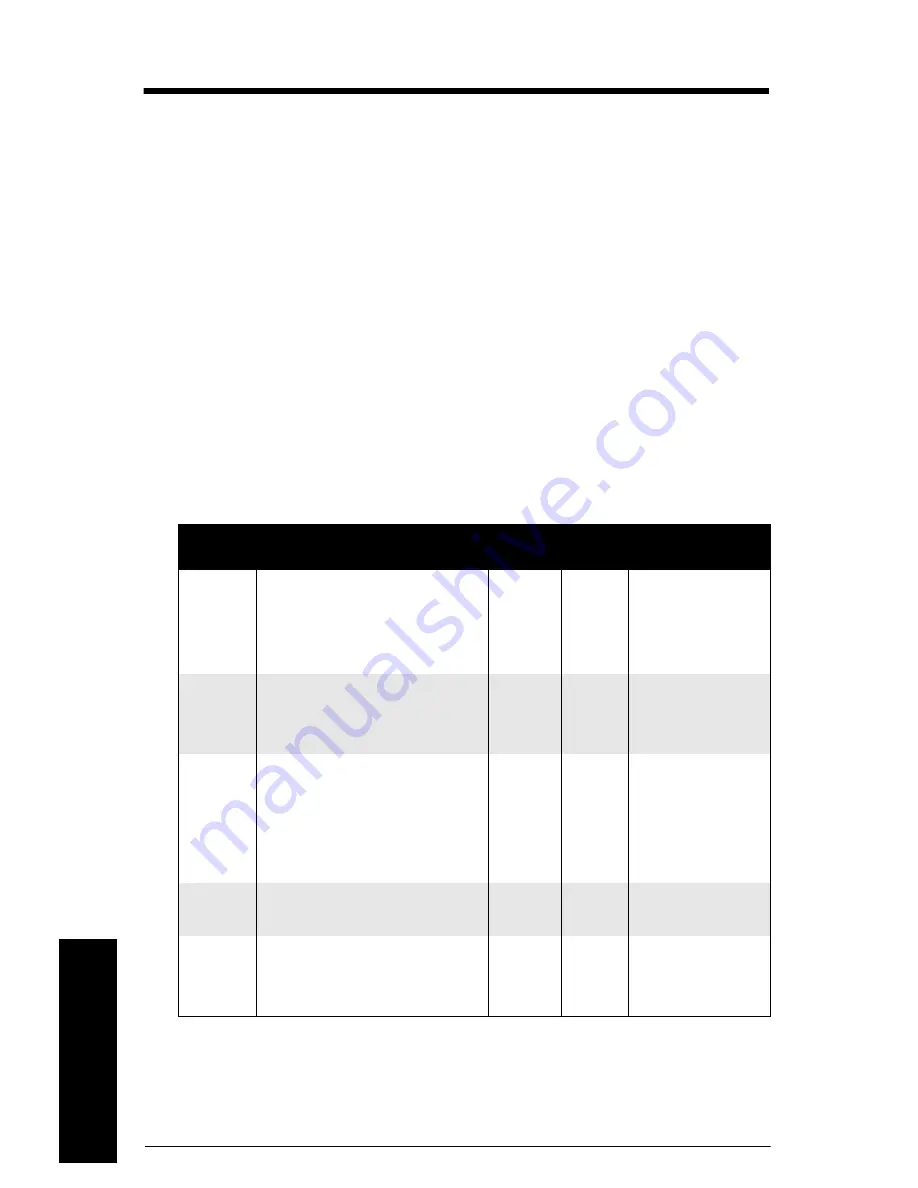
Page 12
SmartLinx PROFIBUS DP-V1 – Operating Instructions
A5E36197302
m
m
m
m
m
Co
m
m
un
ic
at
io
n
se
tu
p
Application layer
This section describes the information that can be read and written to the MultiRanger
200 HMI or the HydroRanger 200 HMI.
The PLC reads data from the Read block (PLC input) of the PROFIBUS DP-V1 module.
Please note that the current firmware of the HydroRanger 200 HMI does not require a
Write block (PLC output) to be configured in the PLC, as cyclic writing to the MultiRanger
200 HMI is not supported at this time.
Data access methods
The PROFIBUS DP-V1 module supports cyclic and acyclic communications for Class 1 and
Class 2 master.
Data map
This section describes the read/write process data available from the MultiRanger 200
HMI or the HydroRanger 200 HMI. Please refer to the
Parameters chapter of the your
Siemens device operating instructions for details about the parameters used in the table
below.
Word
offset
Description
Data
type
Bytes
Parameter
0
PV Point 1 (Process variable for
Point 1) in Programmed units.
PV is displayed as an IEEE float-
ing point number.
Float
4
3.2.6.2. Reading
2
PV Point 1 Status Profi status.
PV status byte. See next table for
more details.
Word
2
n/a
3
PV Point 1 Signal Strength.
The
3.2.9.4. Echo Strength (in dB)
from Transducer 1. The value
range is from minimum -30 to
maximum 99.
Word
2
3.2.9.4. Echo
Strength
4
PV Point 2 (Process variable for
Point 2) in Programmed units.
Float
4
3.2.6.2. Reading
6
PV Point 2 Status Profi status
PV status byte. See next table for
more details.
Word
2
n/a
Summary of Contents for PROFIBUS DP-V1
Page 1: ...Operating Instructions SmartLinx PROFIBUS DP V1 08 2015 Edition Communication ...
Page 4: ...ii mmmmm Table of Contents ...
Page 30: ......
Page 31: ......