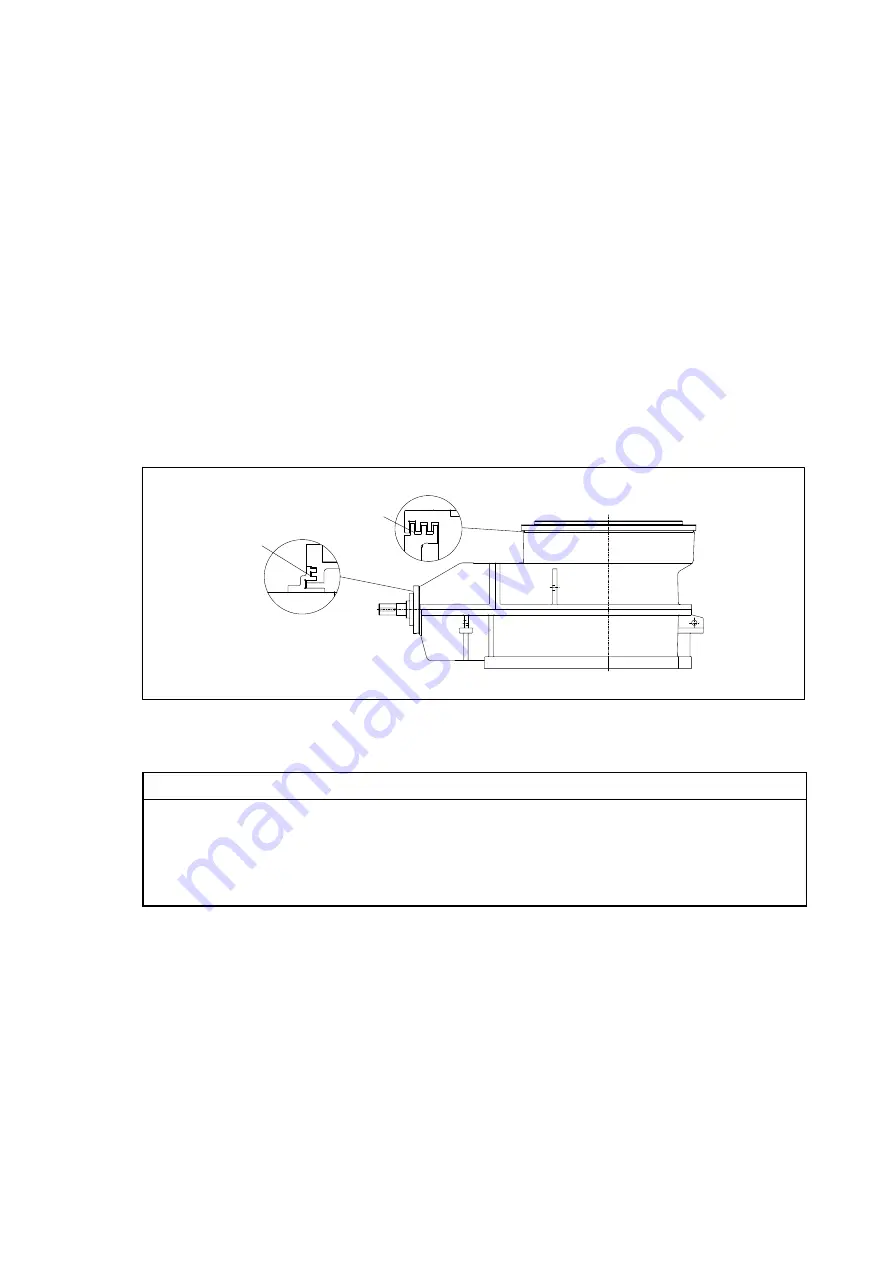
BA 9137 en 12/2015
5.3.3
Hydrodynamic lubrication of the axial tilting pad thrust bearings with radial piston pump
In addition to the hydrodynamic lubrication, part of the oil is fed immediately downstream of the cooler to
the high-pressure pumps through a branch circuit.
The high-pressure pumps are designed as radial piston pumps and supply a constant oil quantity at each
connection. The same oil quantity is supplied to each bearing pad independently of the counter pressure.
The oil connections are distributed so that no two adjacent pads are supplied by one high-pressure pump.
The drive can continue to be operated throughout the time required for replacing a broken-down
high-pressure pump.
In order to ensure that the high-pressure pumps are operating and no oil line is defective, the oil flows are
monitored for minimum and maximum pressure. The pressure is set through the pressure actually exerted
by the grinding rollers.
If the minimum setting of a pressure- or flow-monitored component is fallen short of, the main drive will be
switched off. If the maximum pressure is exceeded, a warning is given or the main drive is shut off. The
non-return valves built into the pads prevent the oil from backing up during normal operation.
5.3.4
Labyrinth seals
The input shaft and output flange are sealed with labyrinth seals. Air filters are provided on the housing to
regulate the pressure.
Labyrinth seals are non-contacting seals. Labyrinth seals prevent wear and tear on the shaft, are
maintenance-free and ensure favourable temperature characteristics.
1
2
Fig. 6:
Labyrinth seal (schematic illustration)
1
Labyrinth seal on output flange
2
Labyrinth seal on input shaft
NOTICE
Property damage
Deficient lubrication is possible from oil leakage on the gear unit.
For reliable operation, labyrinth seals require stationary, horizontal positioning away from dirty water
and high dust concentrations.
Overfilling of the gear unit can cause leakage, as can oil with high foam content.