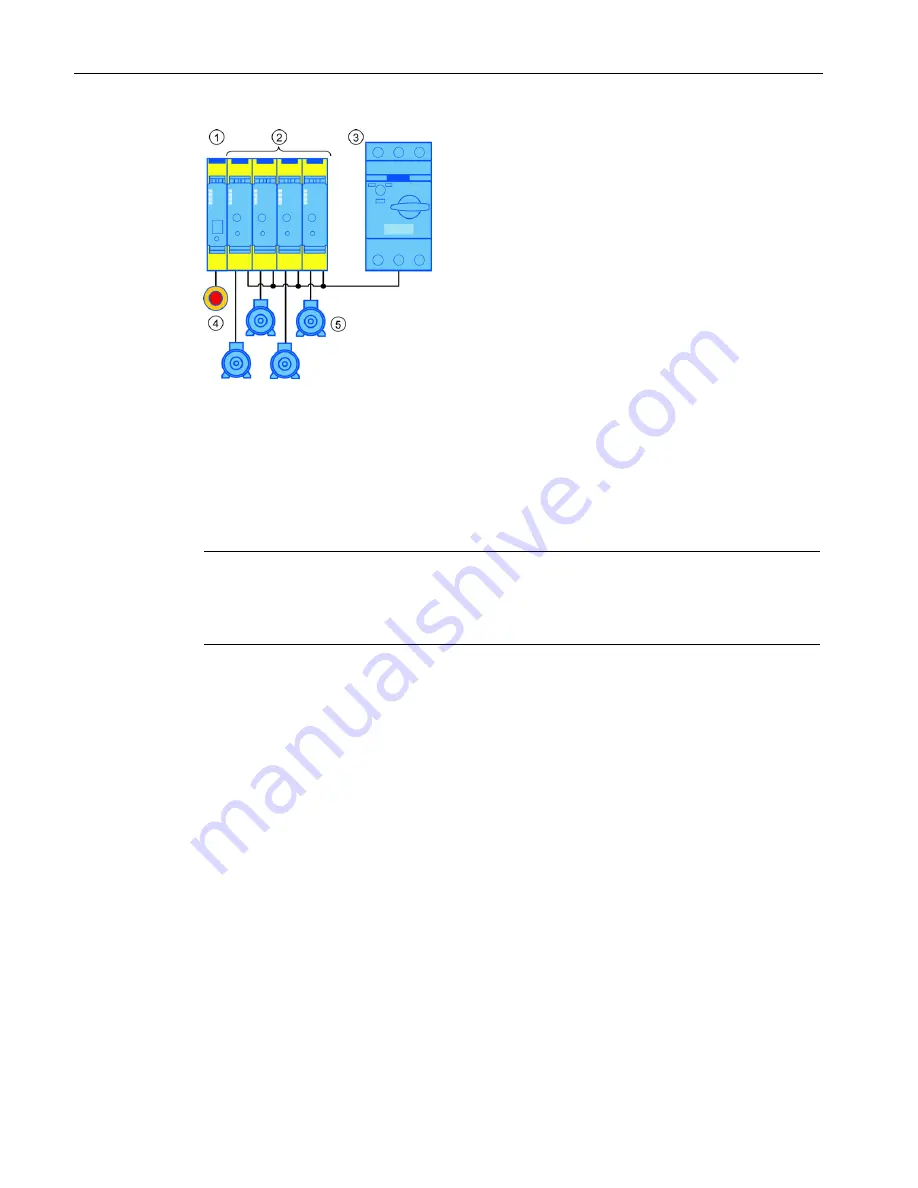
Configuration
4.6 Examples/applications
SIRIUS 3RM1 motor starter
70
Manual, 11/2013, A5E0345285095020A/RS-AB/002
①
SIRIUS 3SK1 Advanced basic unit
②
SIRIUS 3RM1 Failsafe (3RM11 Failsafe or 3RM13 Failsafe) safety-related motor starters
③
SIRIUS 3RV2 motor starter protector
④
EMERGENCY-STOP button
⑤
Motor
Figure 4-3
Configuration with 3SK1 safety relay and device connectors
Note
No hybrid operation of Failsafe and Standard 3RM1 motor starters
Hybrid operation of 3RM11/3RM13 Failsafe motor starters with 3RM10/3RM12 Standard
motor starters is not admissible.
You will find further information in the manual for the 3SK1 safety relay on the Internet with
regard to operation in safety-related applications; see Chapter "Further documentation
(Page 11)". Follow the safety instructions and information contained there.
Reference
For more typcial circuits, please refer to the "Typical circuits (Page 143)" appendix.