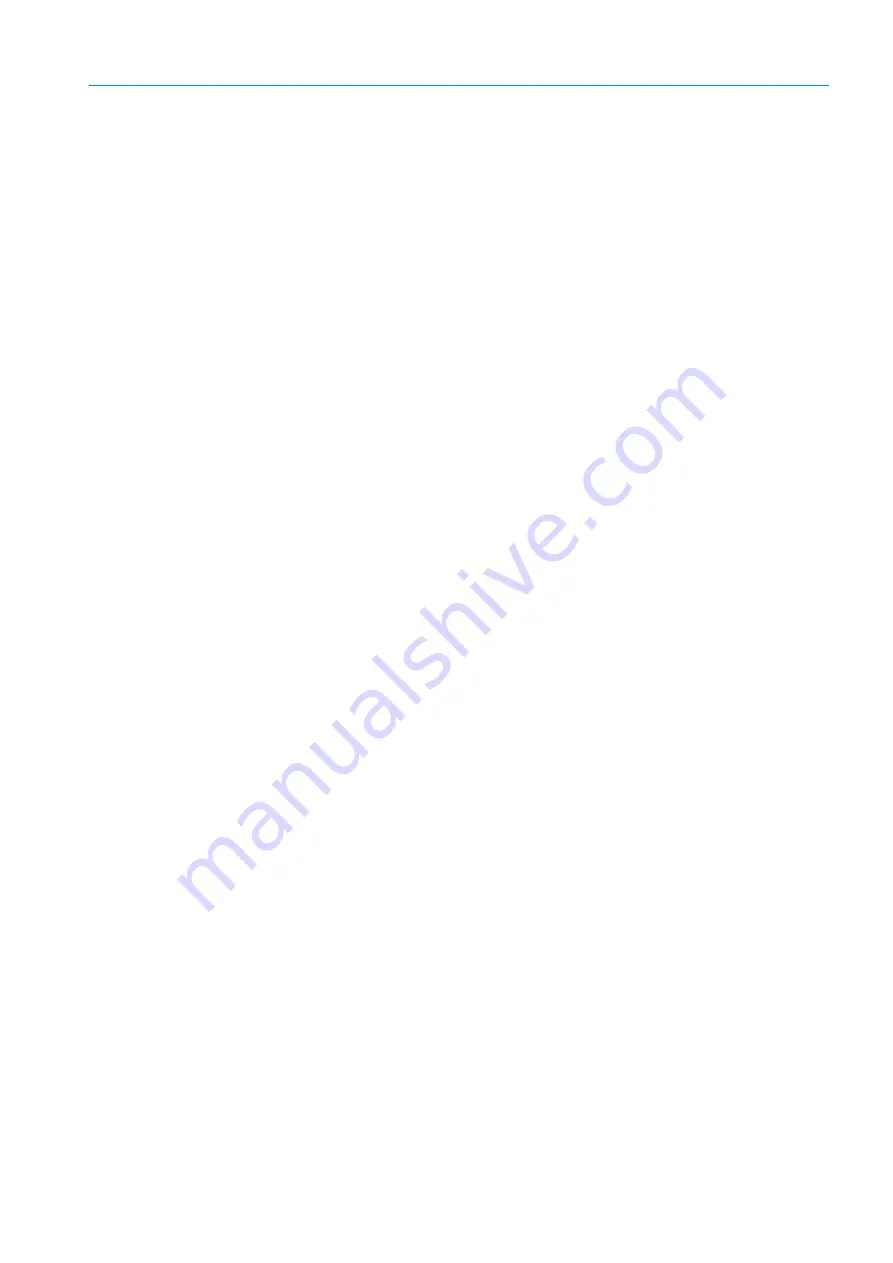
15
8024250/18HT/V2-0/2020-12| SICK
O P E R A T I N G I N S T R U C T I O N S | ZIRKOR200 Ex-G
Subject to change without notice
FOR YOUR SAFETY
2
2.3.3
Restrictions of use
●
The ZIRKOR200 Ex-G is certified for a process-side operating range of 800 mbar abs. to
1100 mbar abs. The use in different pressures is not conform to the EX-certification and
therefore not allowed.
●
Operate the ZIRKOR200 Ex-G within the described specifications (
). If the ZIRKOR200 Ex-G is operated outside the specifications, it does not con-
form to the Ex-certification and is therefore not allowed.