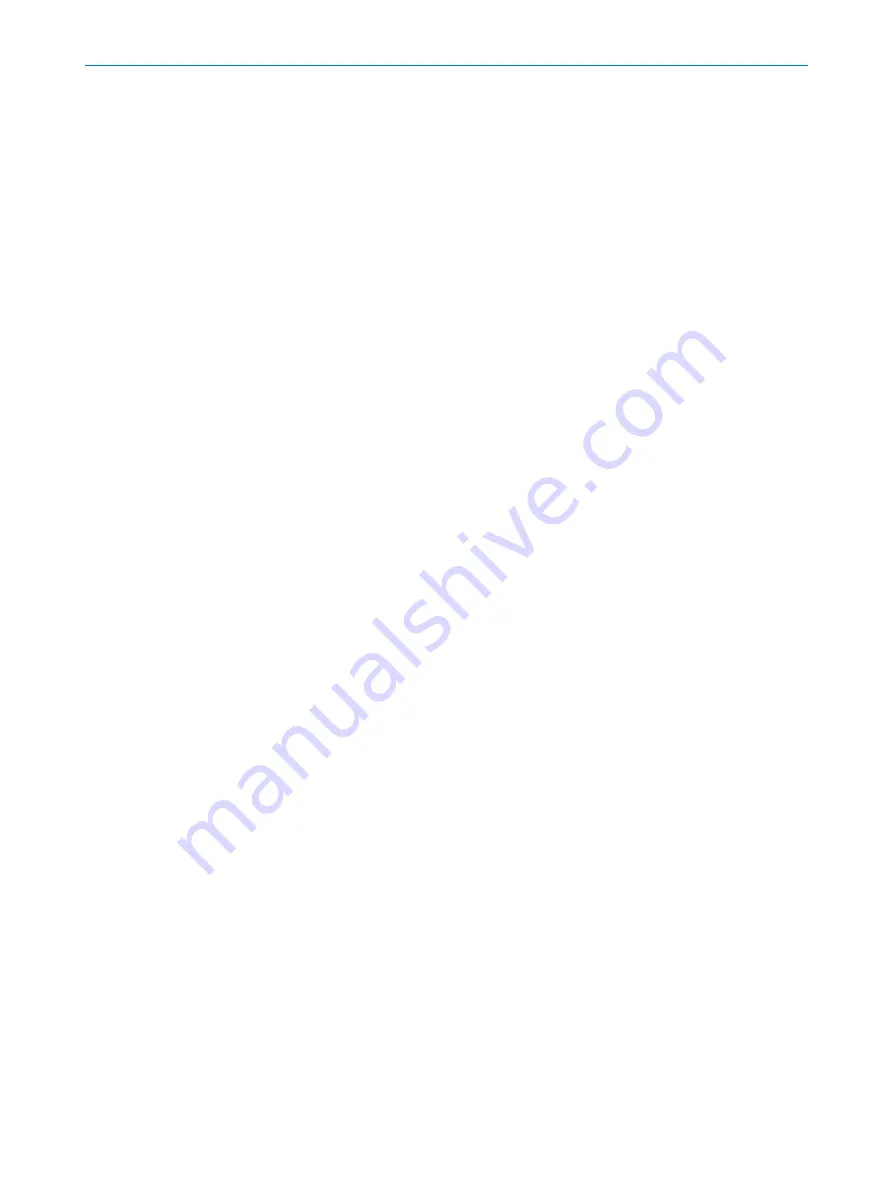
13
Annex
13.1
Compliance with EU directives
T4000 Multi, safety switch
SICK AG, Erwin-Sick-Strasse 1, D-79183 Waldkirch, Germany
You can call up the EU declaration of conformity and the current operating instructions
for the protective device by entering the part number in the search field at
(part number: see the type label entry in the “Ident. no.” field).
Direct link to EU declaration of conformity:
The undersigned, representing the manufacturer, herewith declares that the product is
in conformity with the provisions of the following EU directive(s) (including all applicable
amendments), and that the standards and/or technical specifications stated in the EU
declaration of conformity have been used as a basis for this.
•
MACHINERY DIRECTIVE 2006/42/EC
•
RE DIRECTIVE 2014/53/EU
•
ROHS DIRECTIVE 2011/65/EU
Waldkirch: 2018-03-06
ppa. Walter Reithofer
Vice President R & D
(GBC Industrial Safety)
authorized for technical documentation
ppa. Birgit Knobloch
Vice President Operations
(GBC Industrial Safety)
Notified body: No. 0340, DGUV Test, Prüf- und Zertifizierungsstelle Elektrotechnik, Gus‐
tav-Heinemann-Ufer 130, 50968 Köln
EC type examination:
•
ET19020
ANNEX
13
8022726/2019-05-07 | SICK
O P E R A T I N G I N S T R U C T I O N S | T4000 Multi
43
Subject to change without notice