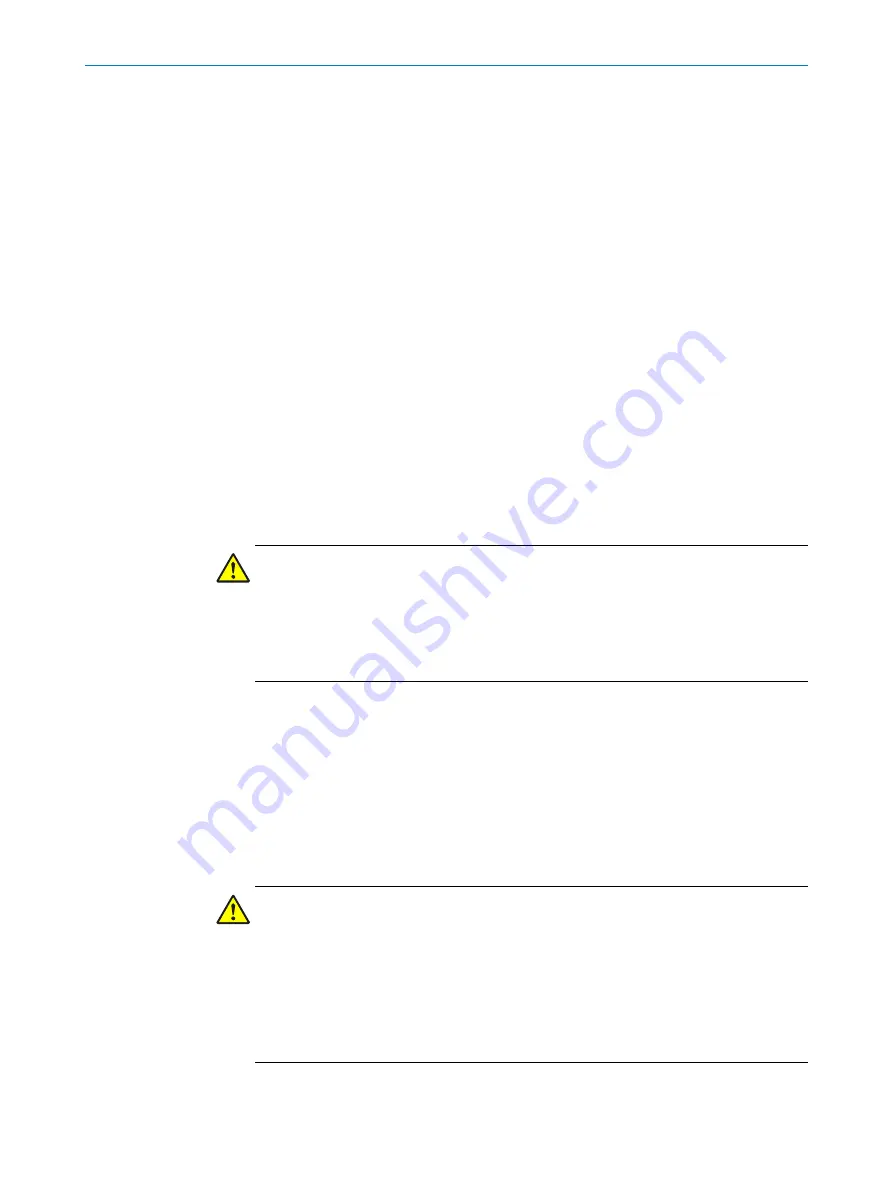
Distance
If several safety switches are mounted on the machine, they must be mounted at a min‐
imum distance to one another
Alignment
The sensor and actuator must be mounted so that their sensing faces are directly
aligned facing each other,
see "Dimensional drawings", page 40
.
Actuating direction
The actuator must approach the sensing face of the sensor when the guard is closed.
4.4
Integration into the electrical control
Switch-on commands that put the machine in a dangerous state may only be activated
when the protective device is closed. When the machine goes into a dangerous state, a
stop command must be triggered if the protective device is opened. Depending on the
safety concept, the signal is analyzed by safety relays or a safety controller, for example.
The control that is connected and all devices responsible for safety must comply with
the required performance level and the required category (for example, according to
ISO 13849-1).
4.4.1
Safety outputs
DANGER
Hazard due to lack of effectiveness of the protective device
In the case of non-compliance, it is possible that the dangerous state of the machine
may not be stopped or not stopped in a timely manner.
b
Make sure that the following control and electrical requirements are met so the
protective function can be fulfilled.
•
The output signals of the safety outputs must not be connected to each other.
•
The two signals must be processed separately in the machine controller.
•
The machine must switch to the safe state at any time if at least one safety output
switches to the OFF state.
•
The safety outputs (relay outputs) KA (13/14) and KB (23/24) must be provided
with external fuse protection (use fuse 6 A gG or miniature circuit-breaker 6 A with
characteristic B or C).
•
A cross-circuit between safety output KA (13/14) and safety output KB (23/24)
can be detected only by external clocking. A cross-circuit in the cable can be
excluded by protected cable routing.
DANGER
Hazard due to lack of effectiveness of the protective device
In the case of non-compliance, it is possible that the dangerous state of the machine
may not be stopped or not stopped in a timely manner.
Downstream contactors must be positively guided and monitored depending on applic‐
able national regulations or required reliability of the safety function.
b
Make sure that downstream contactors are monitored (external device monitoring,
EDM).
4
PROJECT PLANNING
14
O P E R A T I N G I N S T R U C T I O N S | T4000 Multi
8022726/2019-05-07 | SICK
Subject to change without notice