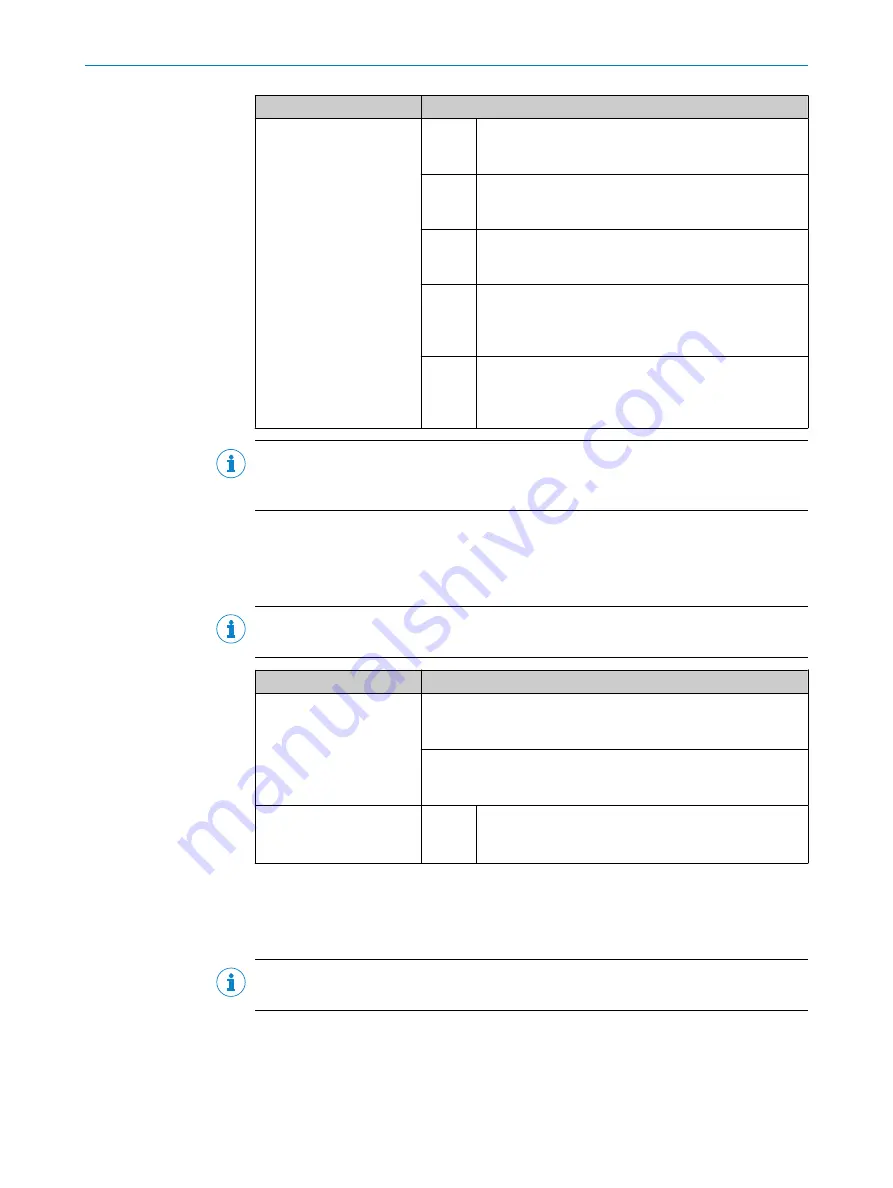
Properties
Value
Coding
0
No device inspection: No inspection is performed on
this IO-Link port regarding the correct device ID, manu‐
facturer ID or serial number.
1
Type-compatible device (V1.0): An inspection is only per‐
formed on the IO-Link port with regard to the correct
device ID and manufacturer ID.
2
Type-compatible device (V1.1): An inspection is per‐
formed on the IO-Link port with regard to the revision
ID, device ID and manufacturer ID.
3
Type-compatible device (V1.1) with restore: An
inspection is performed on the IO-Link port with regard
to the revision ID, device ID and manufacturer ID. Data
storage (reading and writing) is permitted.
4
Type-compatible device (V1.1) with restore: An inspec‐
tion is performed on the IO-Link port with regard to the
revision ID, device ID and manufacturer ID. Data storage
(writing) is allowed.
NOTE
For data storage, "Expected Vendor ID" and "Expected Device ID" must be set and must
match the connected device (for details see
7.1.2.2.1.4
Expected manufacturer ID
Expected Vendor ID
can be used to specify the vendor ID with which a connected IO-Link
device must match.
NOTE
The manufacturer ID is only checked at inspection level "1" to "4".
Properties
Value
PROFINET access
Commissioning protocol for all IO-Link device submodules (except
"Digital input", "Digital output"; slot 2, subslot 2 to 5)
Byte 6 to 7: Expected manufacturer ID
SIG200-IO-Link master (slot 2, subslot 1)
Index 0xB100/0xB101/0xB102/0xB103, byte 6 to 7: Expected
manufacturer ID
Coding
Any
Expected manufacturer ID of the IO-Link device con‐
nected to the IO-Link port (unsigned integer 16)
Example: Manufacturer ID SICK AG = 26
7.1.2.2.1.5
Expected device ID
Expected Device ID
can be used to specify the device ID with which a connected IO-Link
device must match.
NOTE
The device ID is only checked at inspection level "1 "to "4".
7
SIG200 CONFIGURATION
36
O P E R A T I N G I N S T R U C T I O N | Sensor Integration Gateway - SIG200
8017853.1D0S/2021-11-04 | SICK
Subject to change without notice