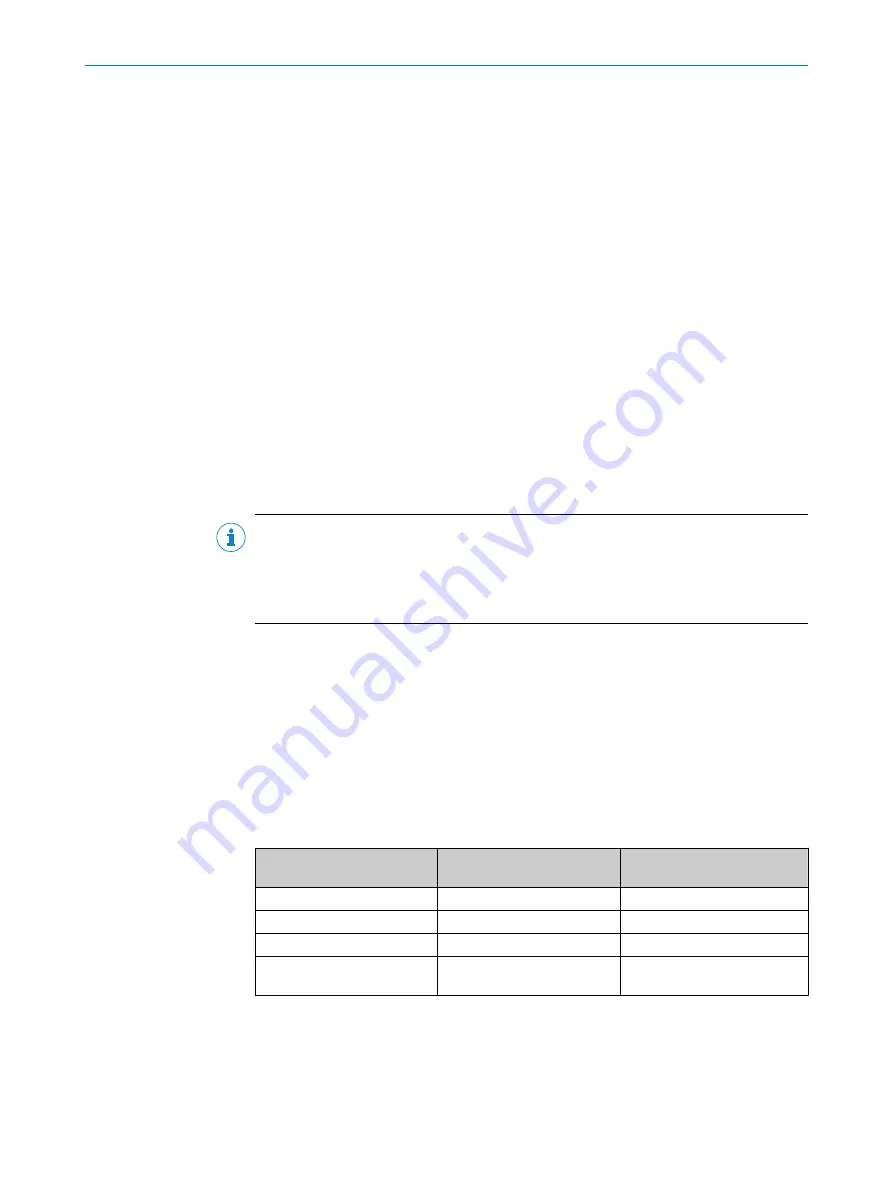
These measures must be selected in the SISTEMA project file for each user-defined
subsystem. In addition, the correct values must be chosen for those components that
are not part of the scope of delivery,
see "General requirements", page 30
.
4.4
Design
This chapter contains information about implementing the design of the functional
safety system. Any design-related contents of the relevant operating instructions also
apply. The following information is provided in the operating instructions for safety laser
scanners in particular:
•
Height of the scan plane
•
Protective field length
•
Protective field width
•
Stopping distance
•
Monitoring case switching time
4.4.1
Safety laser scanner
It is recommended to mount the safety laser scanner horizontally so that the scan
plane is 300 mm above the ground. This means a resolution of 70 mm can be used.
If the mounting height is less than 300 mm above the ground, the resolution must be
adjusted to 50 mm and the protective field must be enlarged.
NOTE
At a resolution of 50 mm, the maximum size of the protective field is reduced. The man‐
ufacturer must ensure that there is no possibility of avoiding the protective field.
If the height of the scan plane is greater than 300 mm, additional measures must be
taken to prevent crawling beneath.
4.4.2
Robot operating modes
Implementation of operating modes and the operating modes considered
Selecting between the robot operating modes is not a part of this safety system. You
must select the operating mode using the robot controller (e.g. with the operating mode
selector switch in the robot operating panel).
This safety system takes the following operating modes into account:
•
Automatic
•
Manual operating mode with reduced speed
Table 13: Functional scope depending on the selected operating mode
Function
Automatic operating mode
Manual operating mode with
reduced speed
Emergency stop
Active
Active
Safety-rated monitored speed Active
Not active
Initiate a protective stop
Active
Not active
Automatic mode stop (SAFF
safeguarding fence)
Active
Not active
Complementary information
•
You must configure the robot controller for the manual operating mode so that sig‐
nals for a protective stop and safety-rated monitored speed can be bridged.
•
Each time the user mode is changed, the safety system must be manually reset.
4
PROJECT PLANNING
22
O P E R A T I N G I N S T R U C T I O N S | sBot Speed – YA
8024620/16AH/2019-12-02 | SICK
Subject to change without notice