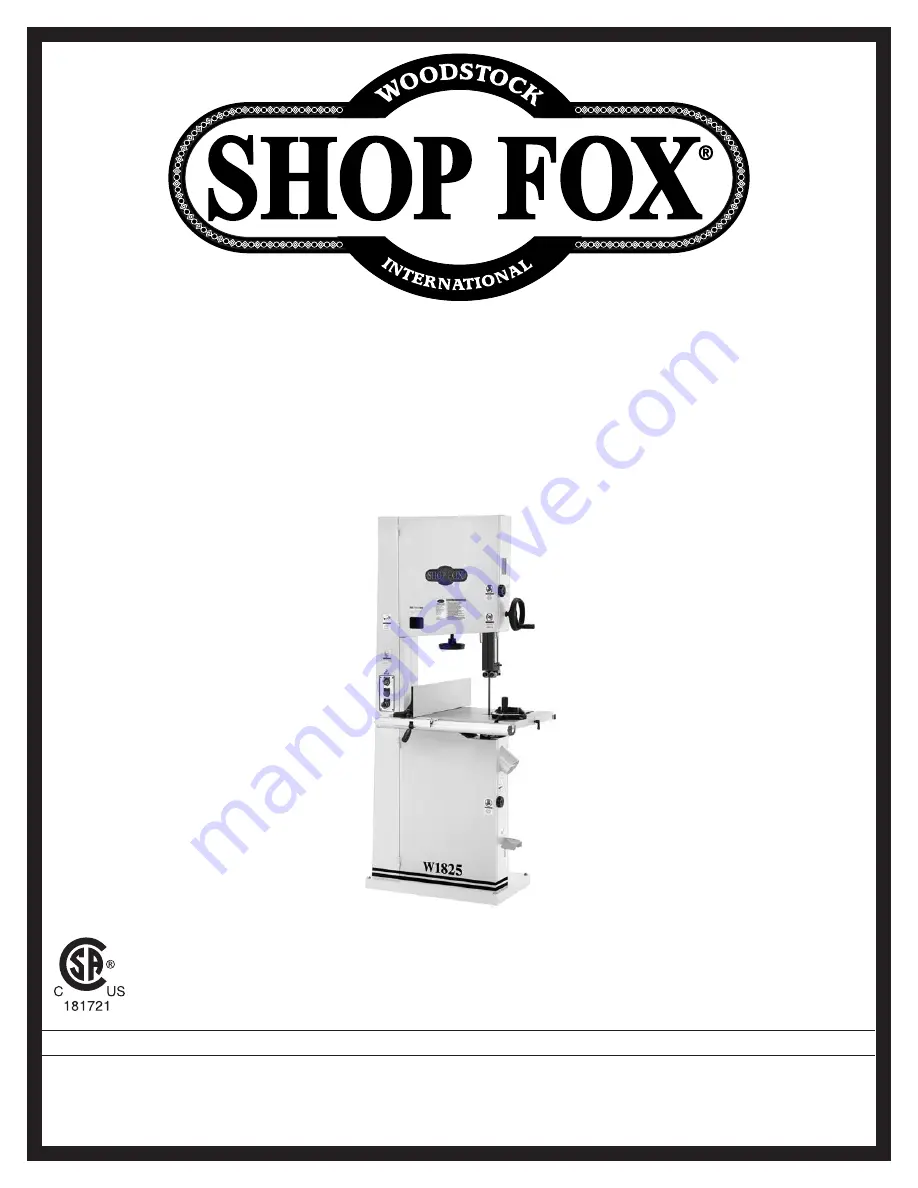
OWNER'S MANUAL
(FOR MODELS MANUFACTURED SINCE 07/15)
MODEL W1825
19" HEAVY DUTY
BANDSAW
Phone: (360) 734-3482 • Online Technical Support: [email protected]
COPYRIGHT © JUNE, 2012 BY WOODSTOCK INTERNATIONAL, INC. REVISED NOVEMBER, 2017 (AB)
WARNING: NO PORTION OF THIS MANUAL MAY BE REPRODUCED IN ANY SHAPE OR FORM WITHOUT
THE WRITTEN APPROVAL OF WOODSTOCK INTERNATIONAL, INC.
#14950KN Printed in Taiwan
V2.11.17
Summary of Contents for W1825
Page 73: ...Model W1825 For Machines Mfd Since 07 15...
Page 76: ......