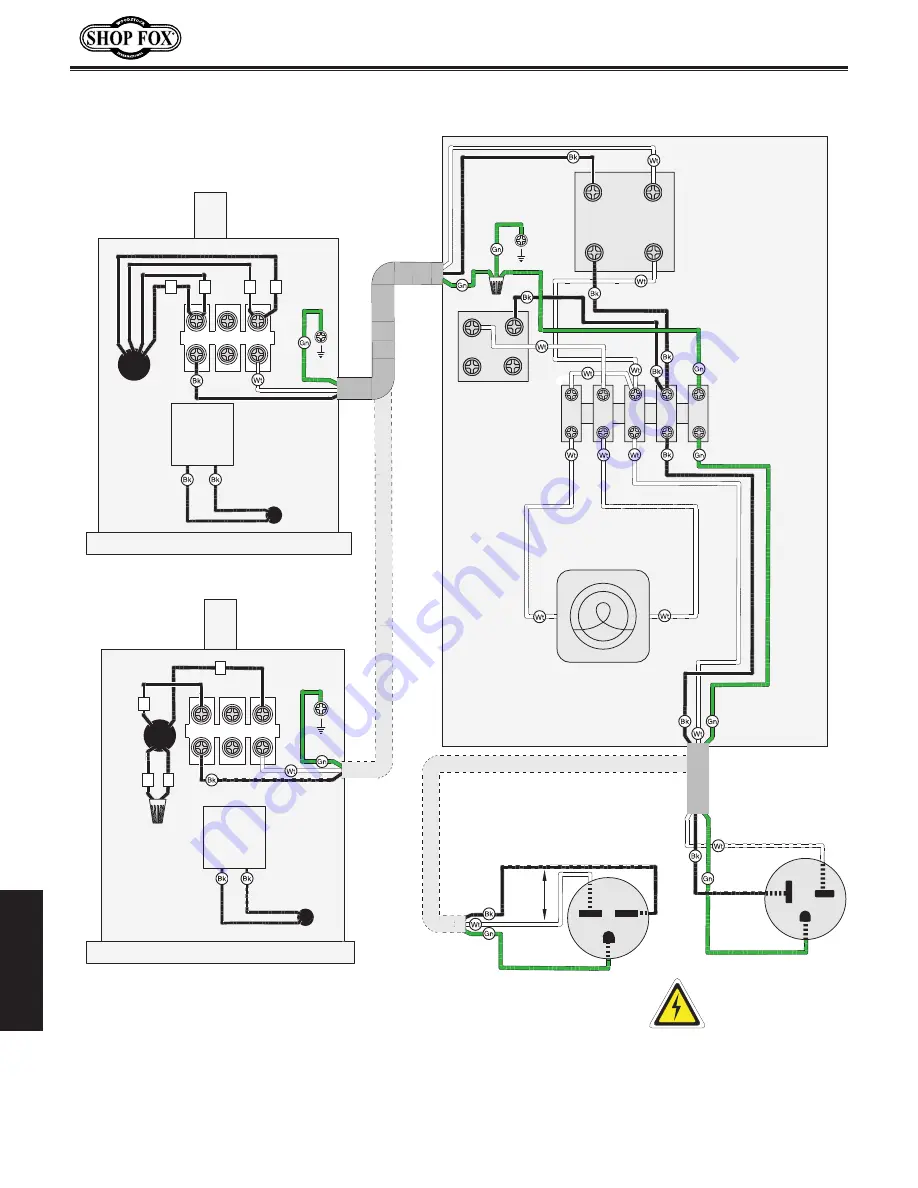
-32-
M1039 12-Speed Drill Press
SE
RV
IC
E
POWER SWITCH
LIGHT SWITCH
(120V ONLY)
LIGHT
SOCKET
(120V Only)
Start
Capacitor
400uF
250VAC
Start
Capacitor
400uF
250VAC
Hot
Hot
Ground
240 VAC
6-15 Plug
(As Recommended)
Neutral
Hot
Ground
120 VAC
5-20 Plug
(Installed)
Rewired to 240V
Ground
Ground
MOTOR
Prewired
(120V)
MOTOR
Rewired
(240V)
Ground
2 4
Rewired to 24
0V
3
4
2
1
3
1
Wiring.Diagram