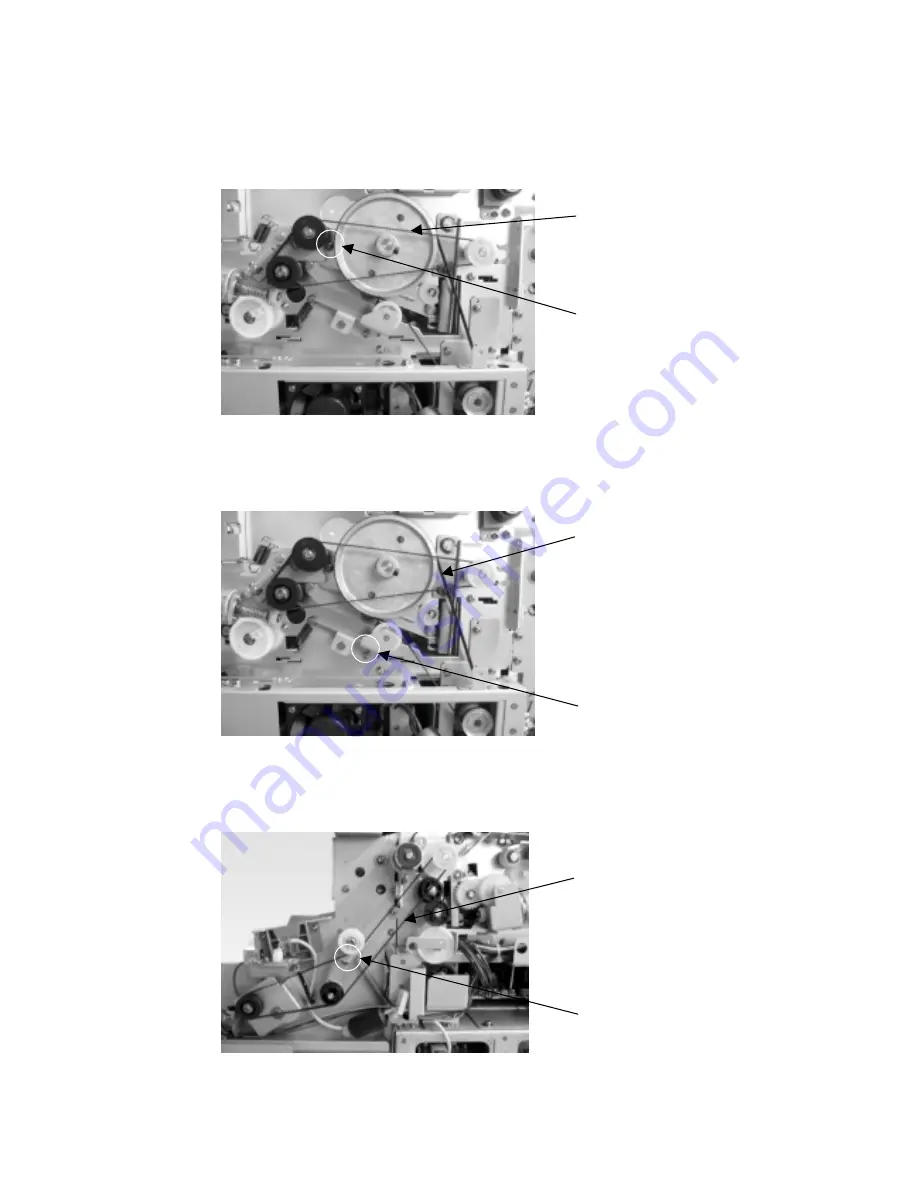
YQE8-J0092E
16
3.2 Timing Belts Adjustment
3.2.1 For Feed Roller Drive
①
Loosen Tension Pulley Screw.
Tension pulley presses timing belt at appropriate strength by spring.
②
Tighten Tension Pulley Screw.
3.2.2 For Feed Roller Drive
①
Loosen Tension Pulley Screw.
Tension pulley presses timing belt at appropriate strength by spring.
②
Tighten Tension Pulley Screw.
3.2.3 For Roll Paper Drive
①
Loosen Tension Pulley Screw.
Tension pulley presses timing belt at appropriate strength by spring.
②
Tighten Tension Pulley Screw.
Timing Belts
Tension Pulley Screw
Timing Belts
Tension Pulley Screw
Timing Belts
Tension Pulley Screw