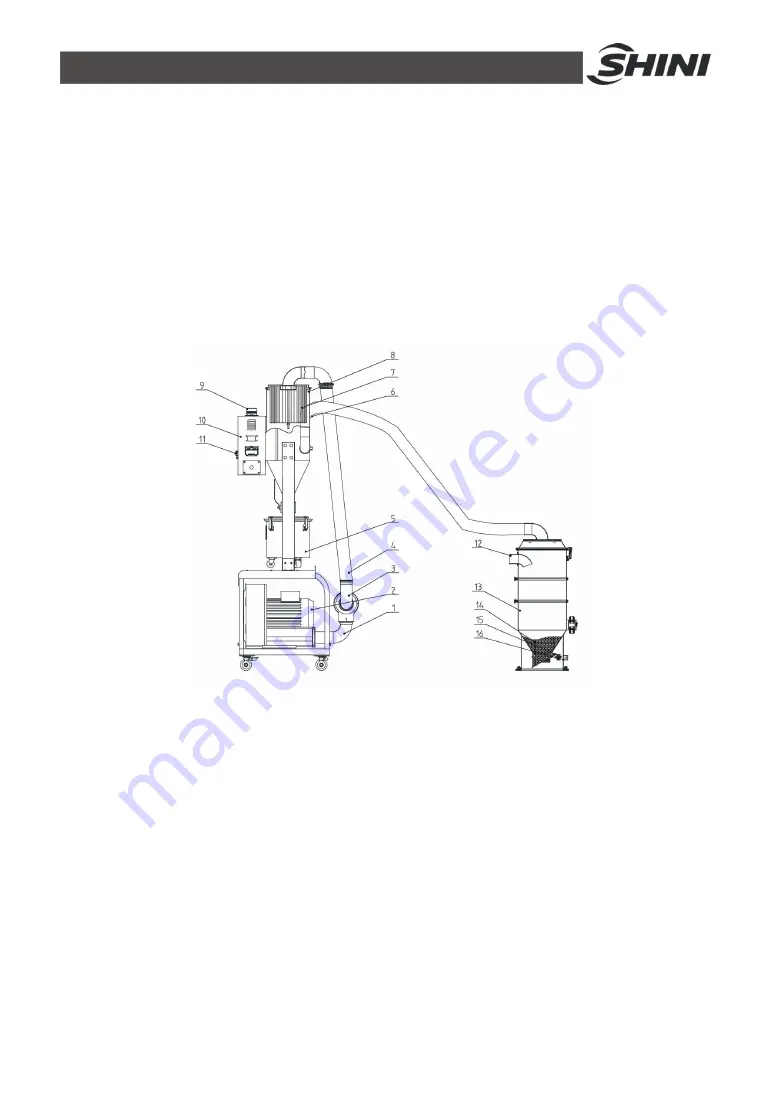
13(33)
2. Structure Characteristics and Working Principle
2.1 Main Functions
SAL-UG series "Euro" Separate-vacuum hopper Loaders are suitable for
conveying plastic granules over long distance. Utilizing high efficiency vacuum
blower to produce vacuum in material hopper, plastic materials will then be fed
into material hopper by outside pressure.
2.1.1 Working Principle
Names of Parts
:
1. Blower suction pipe
2. Blower
3. Vacuum breaking diaphragm valve
4. Steel wire hose
5. Dust collecting barrel
6. Air suction pipe
7. Air filter
8. Dust separating barrel
9. Alarm light
10. Electric cabinet
11. Main switch
12. Material inlet
13. Material hopper
14. Material
15. Discharging plate
16. Reed switch
Picture 2-1: Working Principle
After startup, when the reed switch (16) detected there
’
s no materials, the blower
(2) starts working to generate negative-pressure vacuum inside the hopper (13).
Meanwhile, the discharging plate (15) is closed, and materials (14) in the storage
Summary of Contents for SAL-10HP-UG
Page 1: ...SAL UG Separate vacuum Hopper Loader Date Sep 2020 Version Ver C English ...
Page 2: ......
Page 5: ...5 33 ...