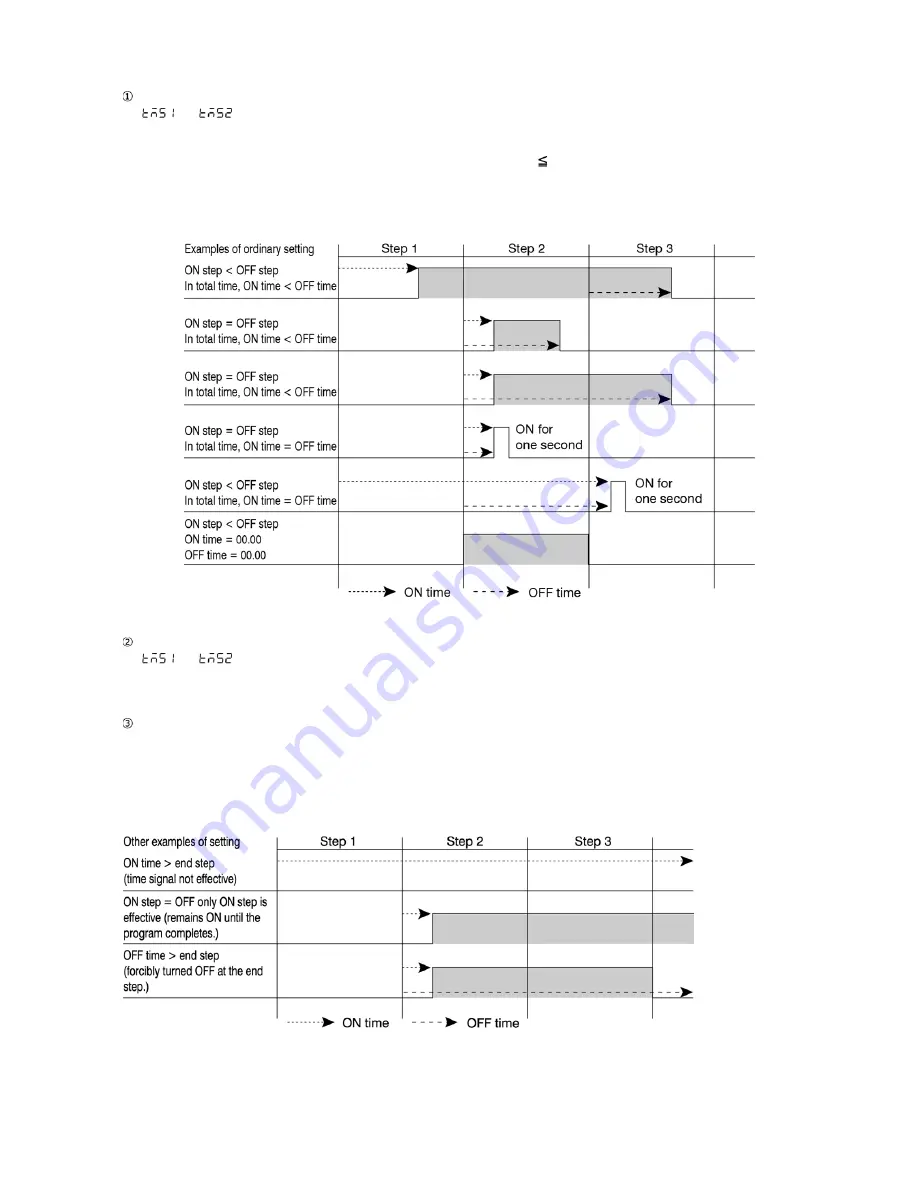
- 27 -
6-15. Time Signal
Time signal: Event output and status output can be produced for a designated period of time. Two points per pattern are
equipped and ON step, OFF step, ON time and OFF time can be set individually.
Time signal functions under the following conditions:
1)
or
is
set
as
status
output of event output.
2) OFF is not selected in Time signal ON step setting.
3) ON time is set within the end step.
4) In the total length of time elapsed since the start of program, ON time OFF time.
• In the case of ON step = OFF step and ON time = OFF time, time signal turns ON for one second.
• In the case of ON step < OFF step and ON time = OFF time in the total length of time elapsed since the start of program,
time signal turns ON for one second.
(Example of setting: 1 step 10 minutes, ON step = 1, ON time 15 minutes, OFF step = 2 and OFF time 5 minutes)
* When a time signal-related parameter is changed during Hold (HLD), the change is not reflected until HLD is released.
Reasons why time signal does not function (always OFF) (Time signal does not function in the following cases):
1)
or
is not set as status output of event output (including the case where these options are not added).
2) OFF is selected as Time signal ON step setting.
3) ON time exceeds the end step.
4) In the total length of time elapsed since the start of program, ON time > OFF time is set.
Other Matters related to Setting
1) The time of time signal is stopped during HLD and guarantee soak.
2) In case ON step and ON time are set and OFF step is OFF, once time signal turns ON, the end step also turns ON. (When
one or more program executions are set, both remain ON until they are completed.)
3) In case OFF time is set beyond the end step, the end step is forcibly turned OFF. When ON step is the first step and 00:00 is
set for ON time, it does not turn OFF.
4) In case ON time equals step time, it turns ON at the start of the next step.
5) When TS is assigned to a step of which the step time is 0, the action is the same as TS is assigned to the next step.