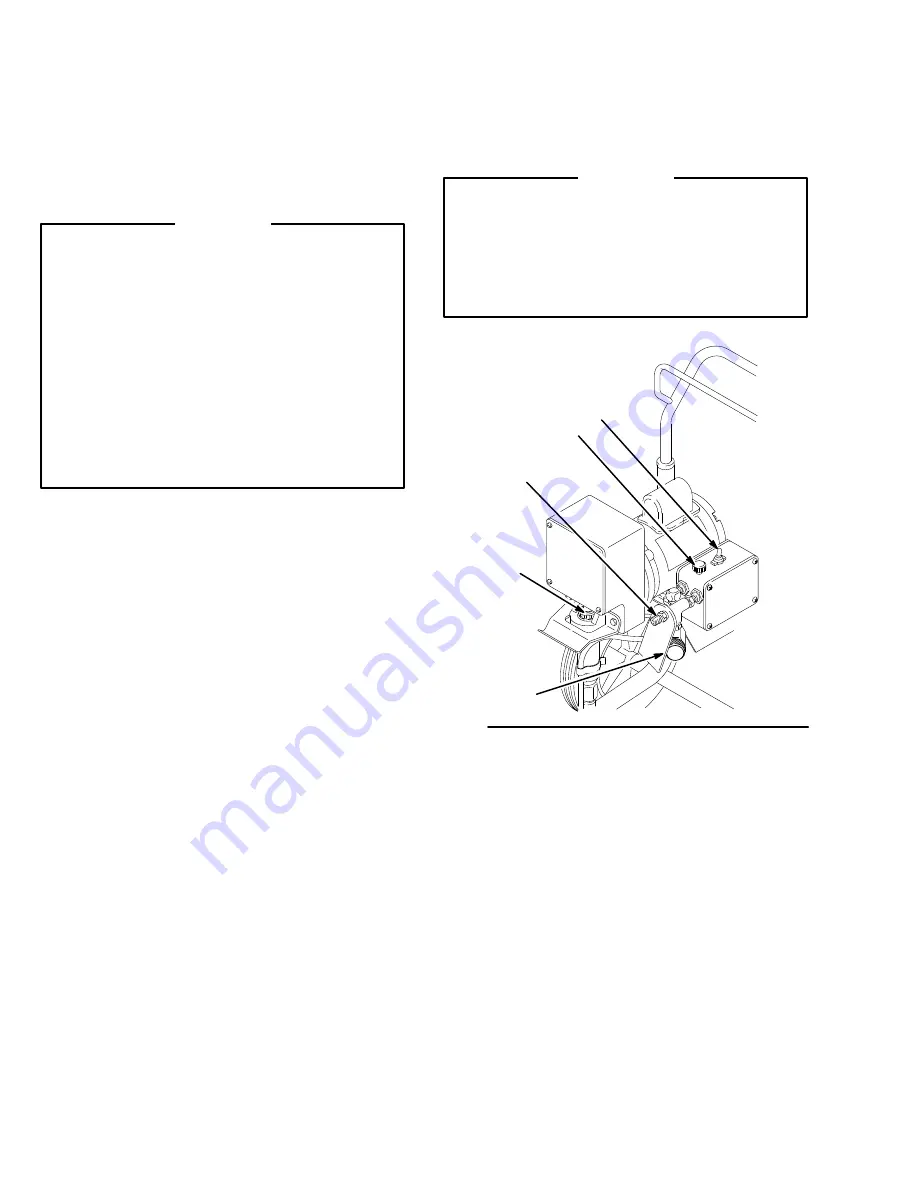
10
820-007
Setup
1.
Connect the hose and gun. Remove the plastic
cap from the outlet nipple (C), and connect a
50 ft. (15 m) (minimum length) fluid hose to it.
Connect the other end of the hose to the spray
gun. Don’t use thread sealant, and don’t install the
spray tip yet!
To avoid damaging the pressure control, which may
result in poor equipment performance and compo-
nent damage, follow these precautions:
1.
Always use a minimum of 50 ft. (15.2 m) nylon
spray hose.
2.
Never use a wire braid hose as it is too rigid to
act as a pulsation dampener.
3.
Never install any shutoff device between the
outlet of the pressure control and the main
hose.
4.
Never allow flushing water or water base paint
to freeze in the system.
CAUTION
2.
Fill the packing nut/wet cup (D) 1/3 full with
throat seal liquid, supplied. Keep the wet cup filled
to help protect and prolong the life of the pump’s
throat packings.
3.
Be sure the electrical service is 120 VAC, 60
Hz, 15 Amp (minimum) and that the outlet you use
is properly grounded.
Use a grounded extension cord which has 3 wires
of a minimum 12 gauge size, and a maximum of
200 ft. (61 m) long. Longer lengths may affect
sprayer performance.
Do not remove the grounding prong of the power
supply cord plug, and do not use an adapter.
4.
Set the pressure control by turning the knob (B)
to the lowest setting.
5.
Be sure the ON/OFF switch (A) is OFF.
6.
Plug the power supply cord into a grounded
electrical outlet that is at least 20 ft. (6 m) away
from the spray area to reduce the chance of a
spark igniting the spray vapors.
7.
An optional filter kit, part no. 820–080, is avail-
able. Instructions are included with it.
8.
Flush the pump. An important part of the care
and maintenance of your sprayer is proper flush-
ing. Refer to page 12.
CAUTION
Never operate the sprayer without the drain valve
(19) in place. The drain valve is used to help relieve
system pressure and to help prime the sprayer.
Do not attach a spray hose to the drain valve; do-
ing so could result in costly damage to the pressure
control.
0740
Fig. 1
A
B
C
D
19
9.
Prepare the paint as instructed by the manufac-
turer. Remove any skin that may have formed. Stir
the paint to dissolve pigments. Strain the paint
through a fine, nylon–mesh bag (available at most
paint dealers) to remove particles that might clog
the spray tip.
This is probably the most important
step toward trouble–free spray painting.
New paint seldom needs thinning. Add solvent to
old and remixed paints to replace the solvent lost
through evaporation. Do not add too much solvent
as thin paint is hard to control and doesn’t cover
very well. Follow the paint manufacturer’s recom-
mendations on thinning.
Summary of Contents for 820-001
Page 3: ...3 820 007 Notes...