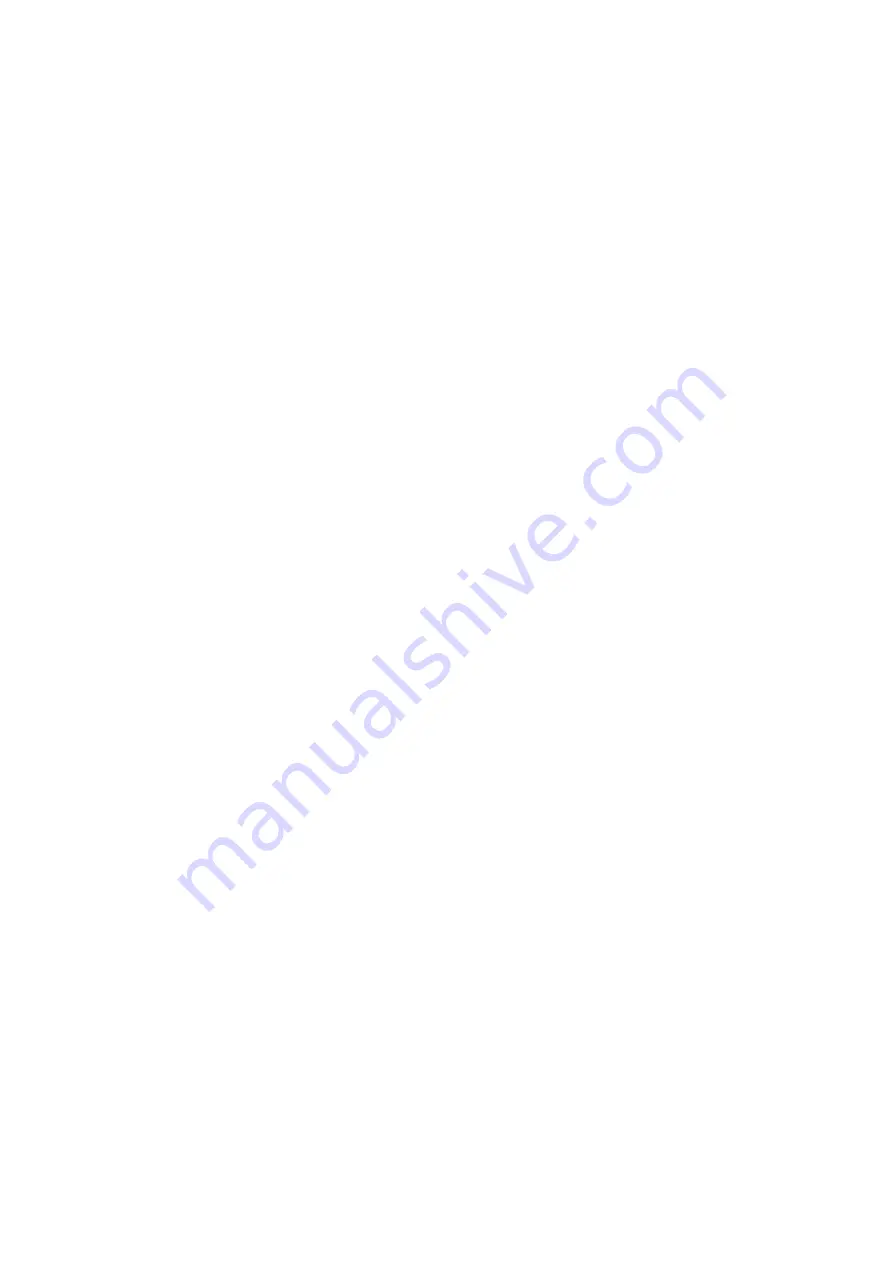
19
They are according to other principles of their selection and as far as the parameters of a set of synergistic can still be corrected by the system described
in paragraph 7.3.1, it adjustable parameters in manual mode can not be changed according to the rules synergistic.
Please note that after calling packet memory settings and change any welding parameter changes made will not be automatically saved in this package.
After a few seconds (8 seconds) the new settings are loaded to the cache device, but will not be stored permanently on a specific number of memory.
Will function, until you change one parameter, or after a reboot. To return to the settings stored, you must call them from a particular memory stored
number.
7.3.2.1 brazing
Function Manual, the manual selection of parameters is particularly useful for braze welding. Using the three welding parameters must be set optimal set
capable of producing a proper weld. When selecting parameters to be selected low and high voltage wire feed speed. It is recommended to use argon as
a shielding gas, but good results can also use a mixture of argon with CO
2 (
82/18). Due to the required shape of the weld inductance should be selected
a shielding gas, but good results can also use a mixture of argon with CO
2 (
82/18). Due to the required shape of the weld inductance should be selected
a shielding gas, but good results can also use a mixture of argon with CO
2 (
82/18). Due to the required shape of the weld inductance should be selected
empirically depending on the thickness and type of material being welded. As additional material is most commonly used copper-based binder. These
wires are labeled CuSi3 or SG -CuAl.
It is recommended to use the handle of not more than 3m equipped with a Teflon cartridge.
7.3.3 welding of aluminum alloys
In synergy mode, you can select one of two programs for aluminum welding. The programs were selected for welding wire ALSi5 type ER 4043, primarily
intended for aluminum casting and wire AlMg5 type ER 5356, which is suitable for welding all types of constructions and profiles. Welding aluminum is
not a simple function, the welder requires experience, knowledge and behavior of certain practices that will facilitate the welds on aluminum elements.
Device in a synergistic adjusts the output of the corresponding grade materials and types of wires. Depending on your needs, make the appropriate
adjustment of the voltage and the inductance to get the desired effect.
It should first of all remember a few important things that greatly affect the appearance of the joint and affect the correct welding process.
Before starting work on the welding of aluminum components, follow these steps:
Device:
•
Ensure that the feed rollers are designed to work with aluminum groove is shaped like the letter "U" and are dedicated to the appropriate
diameter of the welding wire. Using the wrong rollers will cause deformation of the wire and the problems in the welding process.
•
Ensure that the feed rolls are not too tight. Excessive tension wire may cause feeding problems.
•
Make sure that the handle is equipped with a teflon cartridge guide intended for aluminum. The use of steel elements used to feed the steel
wire will cause feeding problems.
•
Make sure that the contact tip is the right size and is suitable for aluminum wire
•
It is worth mentioning the contribution of part of the wire guide in the tray to the version of Teflon, which improves wire feed, as is the case in
the torch.
Workplace:
•
Pay attention to proper site preparation welding work: hall should be clean, have good ventilation and should maintain a low humidity.
The presence of iron oxide dust or dusts from the steel elektropowietrznym gouging is unacceptable.
•
Position for welding aluminum industrial vacuum cleaners should be vacuumed once a day, after work.
•
Clothing should be clean welders gloves can not be greasy.