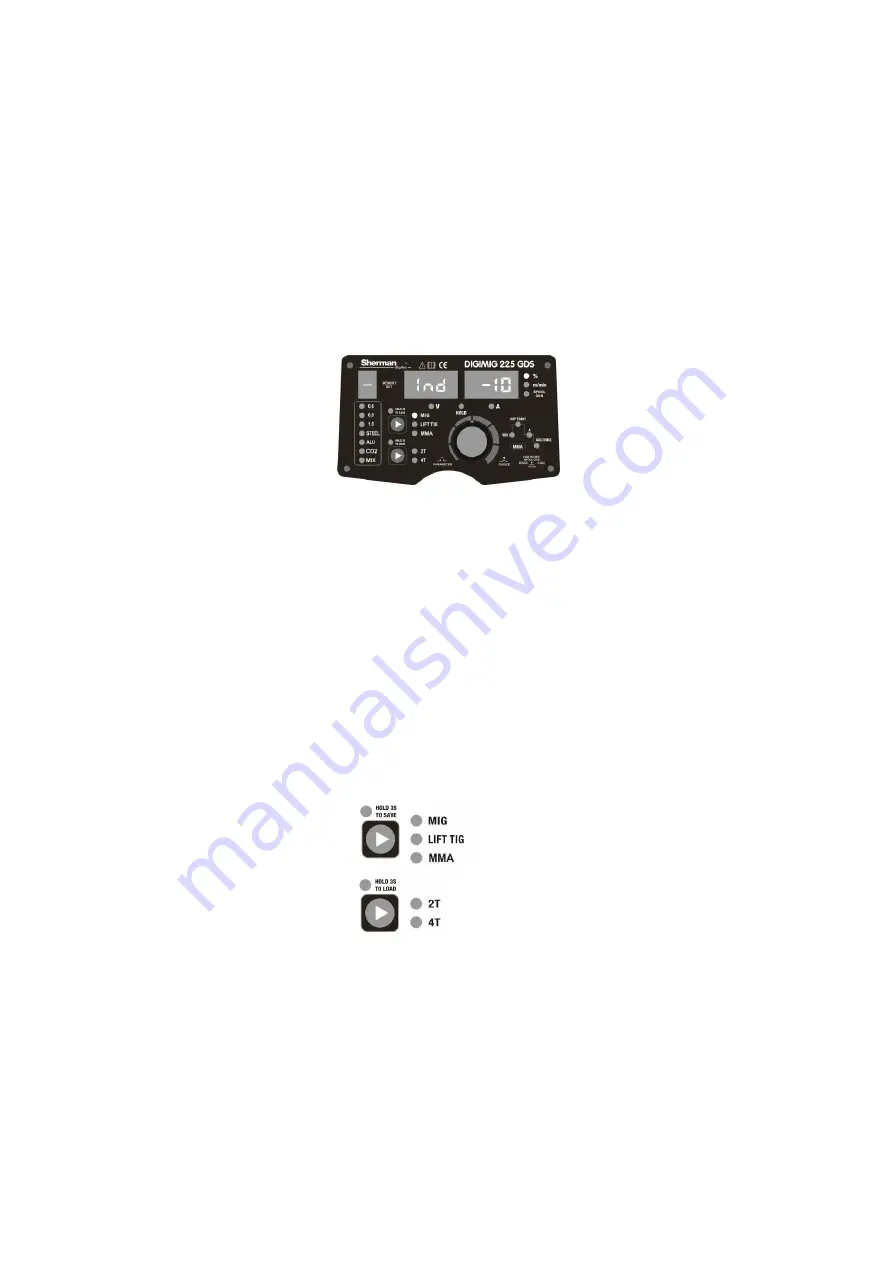
18
Changing the value of inductance also affects the reduction of spatter during arc welding CO
2.
The inductance value is greater than (+) reducing the
Changing the value of inductance also affects the reduction of spatter during arc welding CO
2.
The inductance value is greater than (+) reducing the
Changing the value of inductance also affects the reduction of spatter during arc welding CO
2.
The inductance value is greater than (+) reducing the
amount of spatters when the value is negative (-), increases the amount of spatter. Optimal setting inductance value depends on several factors and may
deviate from the standard recommendations and therefore should be chosen experimentally during the welding tests.
Adjustment of this parameter also allows for brazing thin (3 mm) of the galvanized wires made of copper alloy CuSi3 shielded pure argon or, in certain
cases mixtures of Ar / CO
2
the ratio (82/18).
cases mixtures of Ar / CO
2
the ratio (82/18).
cases mixtures of Ar / CO
2
the ratio (82/18).
To adjust the inductance must press the knob (F) until the left display shows "Ind." Turn the knob to change the inductance of the recommended range:
- 10% (hard arc / weld convex / greater spatter) / + 10% (soft arc / weld flat / less spatter).
7.3.1.1 Saving and loading memory settings for programs in synergy mode
In synergic welding mode DIGIMIG 225GDS can save 10 independent programs containing MIG welding parameters and functions of the device
settings. Recording mode and charging is described in point. 6 B and E.
7.3.2 Manual mode
The device has the ability to switch at any time of the operation mode of action version of the synergistic manual mode. It is advisable to preset welding
conditions described in section 7.3.1, which allows for selection of an optimal voltage and wire feed speed for typical welding parameters. If the weld
quality is not adequate voltage must be adjusted constantly working in synergy mode. If the results are not satisfactory to be referred to as change from
synergies to manual control device, which allows independent adjustment of three welding parameters: welding voltage, wire feed speed, and the
inductance
arc. To switch to manual mode must be simultaneously pressed for
3 seconds both buttons memory
The device switches to manual mode will be disabled, LEDs panel (C), which is a signal that the apparatus came mode synergistic, and the last
parameter setting welding mode synergistic (voltage, wire feed speed and inductance) is a set of active possible for independently controlling . You can
then sequentially pressing the knob (F) to select each of the three welding parameters and the adjustment made in accordance with the expectations of
the operator.
7.3.2.1 Saving and loading memory settings for programs in manual mode
The unit working in manual mode is ready to save welding parameters in a separate package of 10 sets of manual (0-9). To save and load these sets
follow the same way as in section 6 B and E. But keep in mind that the saved parameters manually shaped and synergistic