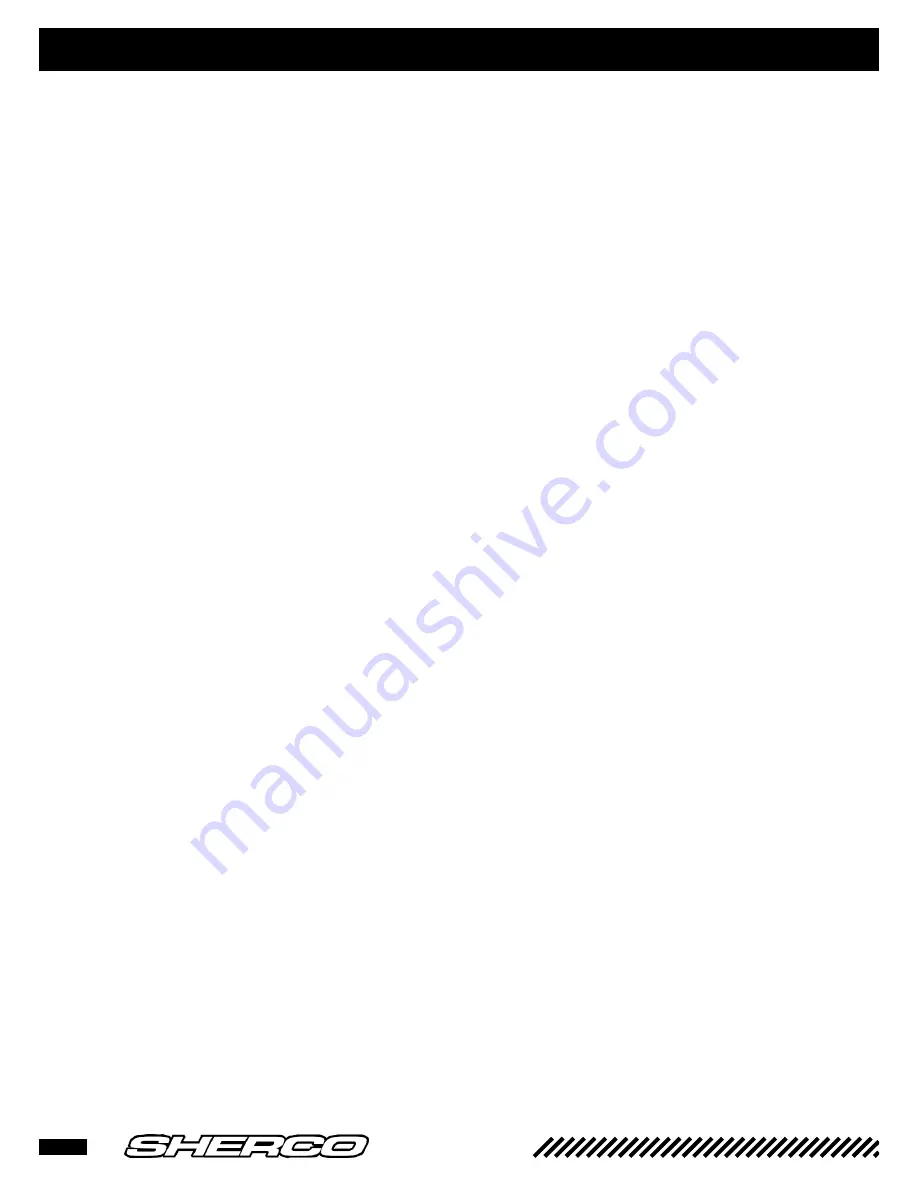
125 SE-
R
4
PREAMBLE
The present manual is primarily intended for certified mechanics working in an
appropriately equipped workshop.
Performing the various operations requires both a solid knowledge in mechanics and the set
of SHERCO tools specific to the 125 SE-R engines.
This workshop manual serves as a complement to the SHERCO 125 SE-
R user’s manual.
Summary of Contents for 125 SE-R 2017
Page 1: ...MANUEL D ATELIER I WORKSHOP MANUAL I MANUAL DE TALLER...
Page 44: ...125 SE R 44 I I WIREMAP Main bundle 6827...
Page 45: ...45 WIREMAP...
Page 46: ...125 SE R 46 I I WIREMAP Light beam 125 SE R...
Page 47: ...47 WIREMAP Racing light beam 125 SE R...
Page 48: ...125 SE R 48 I I WIREMAP Accessory bundle...
Page 49: ...49...