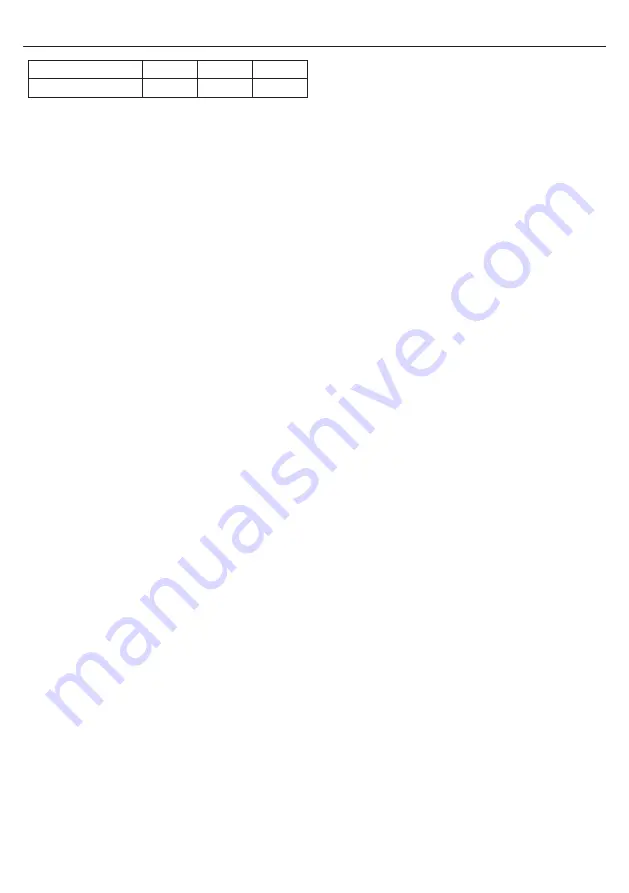
12
Room area (m2)
4
11
15
Maximum charge (kg)
<0.152
0.225
0.304
Prior to beginning work on systems containing flammable refrigerants,
safety checks are necessary to ensure that the risk of ignition is minimised.
For repair to the refrigerating system, the following precautions shall be
complied with prior to conducting work on the system.
Work procedure
Work shall be undertaken under a controlled procedure so as to minimise
the risk of a flammable gas or vapour being present while the work is being
performed.
General work area
All maintenance staff and others working in the local area shall be
instructed on the nature of work being carried out. Work in confined
spaces shall be avoided. The area around the workspace shall be sectioned
off. Ensure that the conditions within the area have been made safe by
control of flammable material
Checking for presence of refrigerant
The area shall be checked with an appropriate refrigerant detector prior to
and during work, to ensure the technician is aware of potentially toxic or
flammable atmospheres. Ensure that the leak detection equipment being
used is suitable for use with all applicable refrigerants, i.e. non-sparking,
adequately sealed or intrinsically safe.
Presence of fire extinguisher
If any hot work is to be conducted on the refrigeration equipment or
any associated parts, appropriate fire extinguishing equipment shall be
available to hand. Have a dry powder or CO2 fire extinguisher adjacent to
the charging area.
No ignition sources
No person carrying out work in relation to a refrigeration system which
involves exposing any pipe work shall use any sources of ignition in such a
manner that it may lead to the risk of fire or explosion.
All possible ignition sources, including cigarette smoking, should be kept
sufficiently far away from the site of installation, repairing, removing
and disposal, during which refrigerant can possibly be released to the
surrounding space. Prior to work taking place, the area around the
equipment is to be surveyed to make sure that there are no flammable
hazards or ignition risks. "No Smoking" signs shall be displayed.
Ventilated area
Ensure that the area is in the open or that it is adequately ventilated
before breaking into the system or conducting any hot work. A degree
of ventilation shall continue during the period that the work is carried
out. The ventilation should safely disperse any released refrigerant and
preferably expel it externally into the atmosphere.
Checks to the refrigeration equipment
Where electrical components are being changed, they shall be fit for the
purpose and to the correct specification. At all times the manufacturer’s
maintenance and service guidelines shall be followed.
If in doubt, consult the manufacturer's technical department for assistance.
The following checks shall be applied to installations using flammable
refrigerants:
•
The actual refrigerant charge is in accordance with the room size within
which the refrigerant containing parts are installed;
•
The ventilation machinery and outlets are operating adequately and are
not obstructed;
•
If an indirect refrigerating circuit is being used, the secondary circuit
shall be checked for the presence of refrigerant;
•
Marking to the equipment continues to be visible and legible. Markings
and signs that are illegible shall be corrected;
•
Refrigeration pipe or components are installed in a position where
they are unlikely to be exposed to any substance which may corrode
refrigerant containing components, unless the components are
constructed of materials which are inherently resistant to being
corroded or are suitably protected against being so corroded.
Checks to electrical devices
Repair and maintenance to electrical components shall include initial
safety checks and component inspection procedures. If a fault exists that
could compromise safety, then no electrical supply shall be connected to
the circuit until it is satisfactorily dealt with. If the fault cannot be corrected
immediately but it is necessary to continue operation, an adequate
temporary solution shall be used. This shall be reported to the owner of the
equipment so all parties are advised.
Initial safety checks shall include:
•
That capacitors are discharged: this shall be done in a safe manner to
avoid possibility of sparking;
•
That no live electrical components and wiring are exposed while
charging, recovering or purging the system;
•
That there is continuity of earth bonding.
Repairs to sealed components
During repairs to sealed components, all electrical supplies shall be
disconnected from the equipment being worked upon prior to any
removal of sealed covers, etc. If it is absolutely necessary to have an
electrical supply to equipment during servicing, then a permanently
operating form of leak detection shall be located at the most critical point
to warn of a potentially hazardous situation.
Particular attention shall be paid to the following to ensure that by
working on electrical components, the casing is not altered in such a
way that the level of protection is affected. This shall include damage to
cables, excessive number of connections, terminals not made to original
specification, damage to seals, incorrect fitting of glands, etc.
•
Ensure that the apparatus is mounted securely.
•
Ensure that seals or sealing materials have not degraded to the point
that they no longer serve the purpose of preventing the ingress of
flammable atmospheres. Replacement parts shall be in accordance with
the manufacturer’s specifications.
NOTE
:
The use of silicon sealant can inhibit the effectiveness of some types of
leak detection equipment. Intrinsically safe components do not have to be
isolated prior to working on them.
Repair to intrinsically safe components
Do not apply any permanent inductive or capacitance loads to the circuit
without ensuring that this will not exceed the permissible voltage and
current permitted for the equipment in use.
Intrinsically safe components are the only types that can be worked on
while live in the presence of a flammable atmosphere. The test apparatus
shall be at the correct rating.
Replace components only with parts specified by the manufacturer. Other
parts may result in the ignition of refrigerant in the atmosphere from a
leak.
Cabling
Check that cabling will not be subject to wear, corrosion, excessive
pressure, vibration, sharp edges or any other adverse environmental
effects. The check shall also take into account the effects of aging or
continual vibration from sources such as compressors or fans.
Detection of flammable refrigerants
Under no circumstances shall potential sources of ignition be used in the
searching for or detection of refrigerant leaks. A halide torch (or any other
detector using a naked flame) shall not be used.