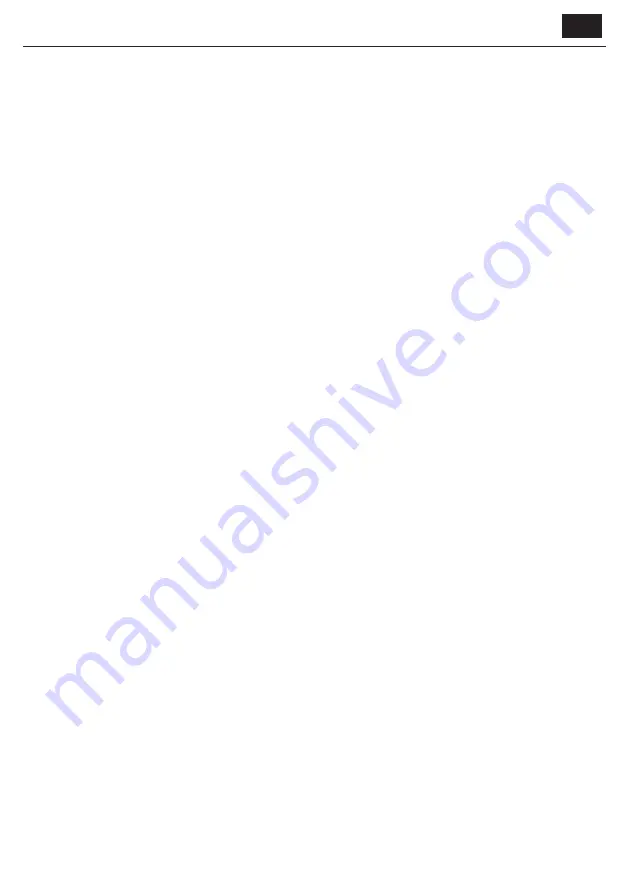
EN
Leak detection methods
The following leak detection methods are deemed acceptable for all
refrigerant systems.
Electronic leak detectors may be used to detect refrigerant leaks but, in
the case of flammable refrigerants, the sensitivity may not be adequate,
or may need re-calibration. (Detection equipment shall be calibrated in a
refrigerant-free area.) Ensure that the detector is not a potential source of
ignition and is suitable for the refrigerant used. Leak detection equipment
shall be set at a percentage of the LFL of the refrigerant and shall be
calibrated to the refrigerant employed, and the appropriate percentage of
gas (25 % maximum) is confirmed.
Leak detection fluids are suitable for use with most refrigerants but the
use of detergents containing chlorine shall be avoided as the chlorine may
react with the refrigerant and corrode the copper pipe-work.
If a leak is suspected, all naked flames shall be removed/extinguished.
If a leakage of refrigerant is found which requires brazing, all of the
refrigerant shall be recovered from the system, or isolated (by means of
shut off valves) in a part of the system remote from the leak. For appliances
containing flammable refrigerants, oxygen free nitrogen (OFN) shall then
be purged through the system both before and during the brazing process
Removal and evacuation
When breaking into the refrigerant circuit to make repairs – or for any other
purpose – conventional procedures shall be used. However, for flammable
refrigerants it is important that best practice is followed since flammability
is a consideration. The following procedure shall be adhered to:
•
remove refrigerant;
•
purge the circuit with inert gas;
•
evacuate;
•
purge again with inert gas;
•
open the circuit by cutting or brazing.
The refrigerant charge shall be recovered into the correct recovery
cylinders. For appliances containing flammable refrigerants, the system
shall be “flushed” with OFN to render the unit safe. This process may need
to be repeated several times. Compressed air or oxygen shall not be used
for purging refrigerant systems.
For appliances containing flammable refrigerants, flushing shall be
achieved by breaking the vacuum in the system with OFN and continuing
to fill until the working pressure is achieved, then venting to atmosphere,
and finally pulling down to a vacuum.
This process shall be repeated until no refrigerant is within the system.
When the final OFN charge is used, the system shall be vented down
to atmospheric pressure to enable work to take place. This operation is
absolutely vital if brazing operations on the pipe-work are to take place.
Ensure that the outlet of the vacuum pump is not close to any ignition
sources and that ventilation is available.
Charging procedures
In addition to conventional charging procedures, the following
requirements shall be followed.
•
Ensure that contamination of different refrigerants does not occur when
using charging equipment. Hoses or lines shall be as short as possible to
minimise the amount of refrigerant contained in them.
•
Cylinders shall be kept upright.
•
Ensure that the refrigeration system is earthed prior to charging the
system with refrigerant.
•
Label the system when charging is complete (if not already).
•
Extreme care shall be taken not to overfill the operefrigeration system.
Prior to recharging the system, it shall be pressure-tested with the
appropriate purging gas.
The system shall be leak-tested on completion of charging but prior to
commissioning. A follow up leak test shall be carried out prior to leaving
the site.
Decommissioning
Before carrying out this procedure, it is essential that the technician
is completely familiar with the equipment and all its detail. It is
recommended good practice that all refrigerants are recovered safely.
Prior to the task being carried out, an oil and refrigerant sample shall be
taken in case analysis is required prior to reuse of reclaimed refrigerant. It is
essential that electrical power is available before the task is commenced.
a. Become familiar with the equipment and its operation.
b. Isolate system electrically.
c. Before attempting the procedure, ensure that:
ū mechanical handling equipment is available, if required, for handling
refrigerant cylinders;
ū all personal protective equipment is available and being used
correctly;
ū the recovery process is supervised at all times by a competent
person;
ū recovery equipment and cylinders conform to the appropriate
standards.
d. Pump down refrigerant system, if possible.
e. If a vacuum is not possible, make a manifold so that refrigerant can be
removed from various parts of the system.
f. Make sure that cylinder is situated on the scales before recovery takes
place.
g. Start the recovery machine and operate in accordance with
manufacturer's instructions.
h. Do not overfill cylinders. (No more than 80 % volume liquid charge).
i. Do not exceed the maximum working pressure of the cylinder, even
temporarily.
j. When the cylinders have been filled correctly and the process
completed, make sure that the cylinders and the equipment are
removed from site promptly and all isolation valves on the equipment
are closed off.
k. Recovered refrigerant shall not be charged into another refrigeration
system unless it has been cleaned and checked.
Labelling
Equipment shall be labelled stating that it has been decommissioned and
emptied of refrigerant. The label shall be dated and signed. For appliances
containing flammable refrigerants, ensure that there are labels on the
equipment stating the equipment contains flammable refrigerant.
Recovery
When removing refrigerant from a system, either for servicing or
decommissioning, it is recommended good practice that all refrigerants
are removed safely.
When transferring refrigerant into cylinders, ensure that only appropriate
refrigerant recovery cylinders are employed. Ensure that the correct
number of cylinders for holding the total system charge are available.
All cylinders to be used are designated for the recovered refrigerant
and labelled for that refrigerant (i.e. special cylinders for the recovery of
refrigerant). Cylinders shall be complete with pressure-relief valve and
associated shut-off valves in good working order. Empty recovery cylinders
are evacuated and, if possible, cooled before recovery occurs.
The recovery equipment shall be in good working order with a set of
instructions concerning the equipment that is at hand and shall be suitable
for the recovery of all appropriate refrigerants including, when applicable,
flammable refrigerants. In addition, a set of calibrated weighing scales
shall be available and in good working order. Hoses shall be complete
with leak-free disconnect couplings and in good condition. Before using
the recovery machine, check that it is in satisfactory working order, has
been properly maintained and that any associated electrical components
are sealed to prevent ignition in the event of a refrigerant release. Consult
manufacturer if in doubt.
The recovered refrigerant shall be returned to the refrigerant supplier
in the correct recovery cylinder, and the relevant waste transfer note
arranged. Do not mix refrigerants in recovery units and especially not in
cylinders.
If compressors or compressor oils are to be removed, ensure that they have
been evacuated to an acceptable level to make certain that flammable
refrigerant does not remain within the lubricant. The evacuation process