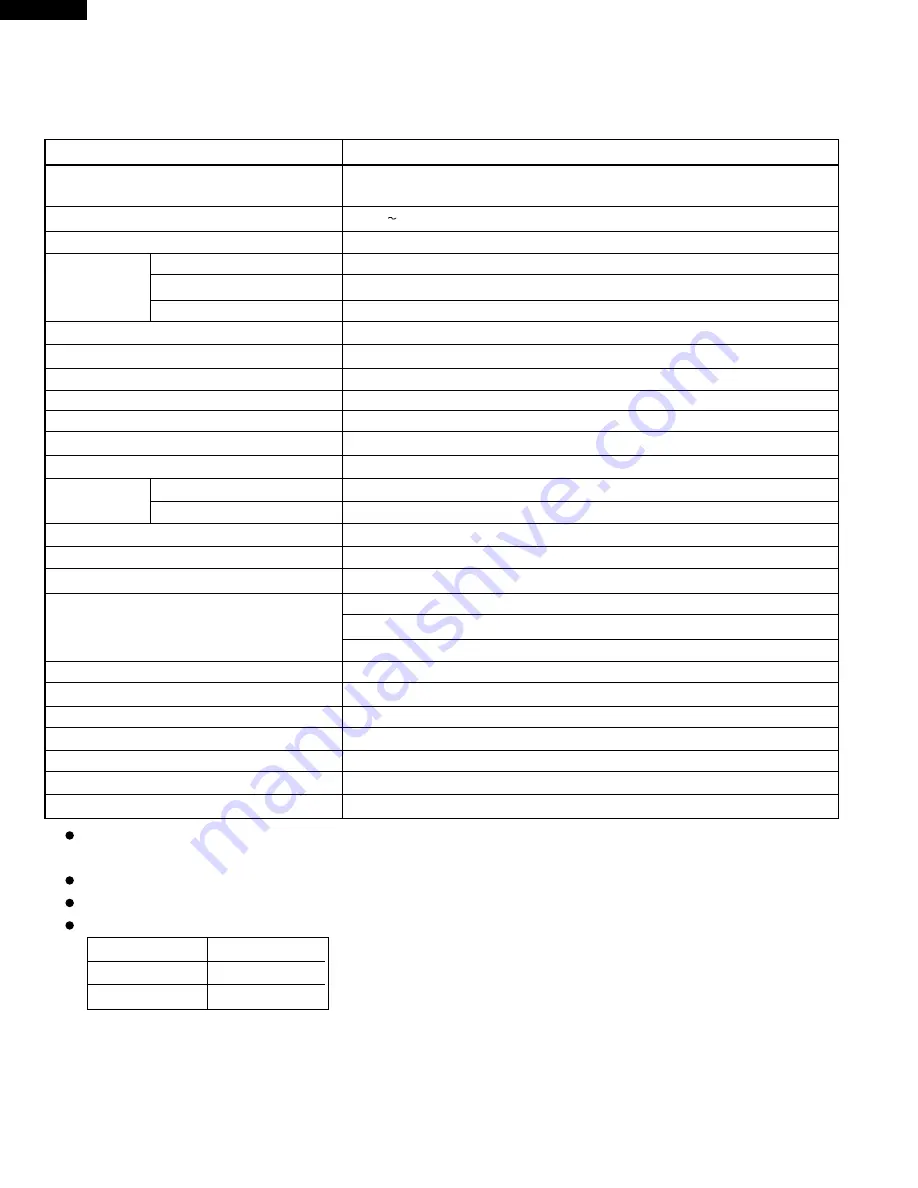
6
DW-71-H
The power consumption shown above is data obtained in condition of room temperature (27˚C) and relative humidity
60%.
The dehumidification enable area is based on JIS.
The power comsumption in stand by model is measured in the sate where the power plug is inserted into the socket.
Noise data
Operating state
Noise
Dehumidifying
Approx. 37 dB
Drying Clothes
Approx. 38 dB
Model
Rated dehumidifying capacity
Rated voltage
Rated frequency
Power
Rated current
consumption
Dehumidifying mode
Drying Clothes mode
Compressor
Cooler
Condenser
Defrosting system
Fan
Fan motor
Water tank
Defrosting
Defrosting timer
Defroster thermo-switch
Power switch
Operation mode selection switch
FULL switch
Indication system
Filter
Discharge water elbow
Overall size
Weight
Power supply cord
Dehumidification enable area
Refrigerant
SPECIFICATION
DW-71-H
6.3 L/day (daily dehumidifying capacity in conditions of room temperature
27˚C and relative humidity 60%)
230V
50Hz
1.0A
187W
190W
Rorary compressor, output 100W (model XB357RCA)
Plate type with forced draft
Plate type with forced draft
Hot gas defrosting
ø160 sirocco fan
Shading Coil type single-phase induction motor (2-Pole, output 3W, with temperature fuse)
Automatic stop when about 3 liters is stored. (capacity about 3.8 liters)
Timer IC (period about 40 min)
Thermistor detection
Push switch
Push switch
Microswitch (model V-55100)
Dehumidifying / Drying Clothes lamp: Green
Defrosting lamp: Green
FULL lamp: Orange
Front filter, Air clean filter
Made of resin (to be used for continuous water discharge)
370 mm (W) x 210 mm (D) x 485 mm (H)
Approx. 9.6 kg
Effective length: Approx. 1.8 meters
13 to 20 m
2
HFC-134a, 140g
Summary of Contents for DW-71-H
Page 17: ...17 DW 71 H CIRCUIT DIAGRAM AND EXPLANATION OF OPERATION Circuit diagram ...
Page 18: ...18 DW 71 H ...
Page 20: ...20 DW 71 H 3 Location of PWB parts 1 Power supply PWB Parts side 2 Operation PWB Parts side ...
Page 38: ...38 DW 71 H ...
Page 39: ...39 DW 71 H ...
Page 40: ...40 DW 71 H 96 SHARP CORP YU0 10E Printed in Japan ...