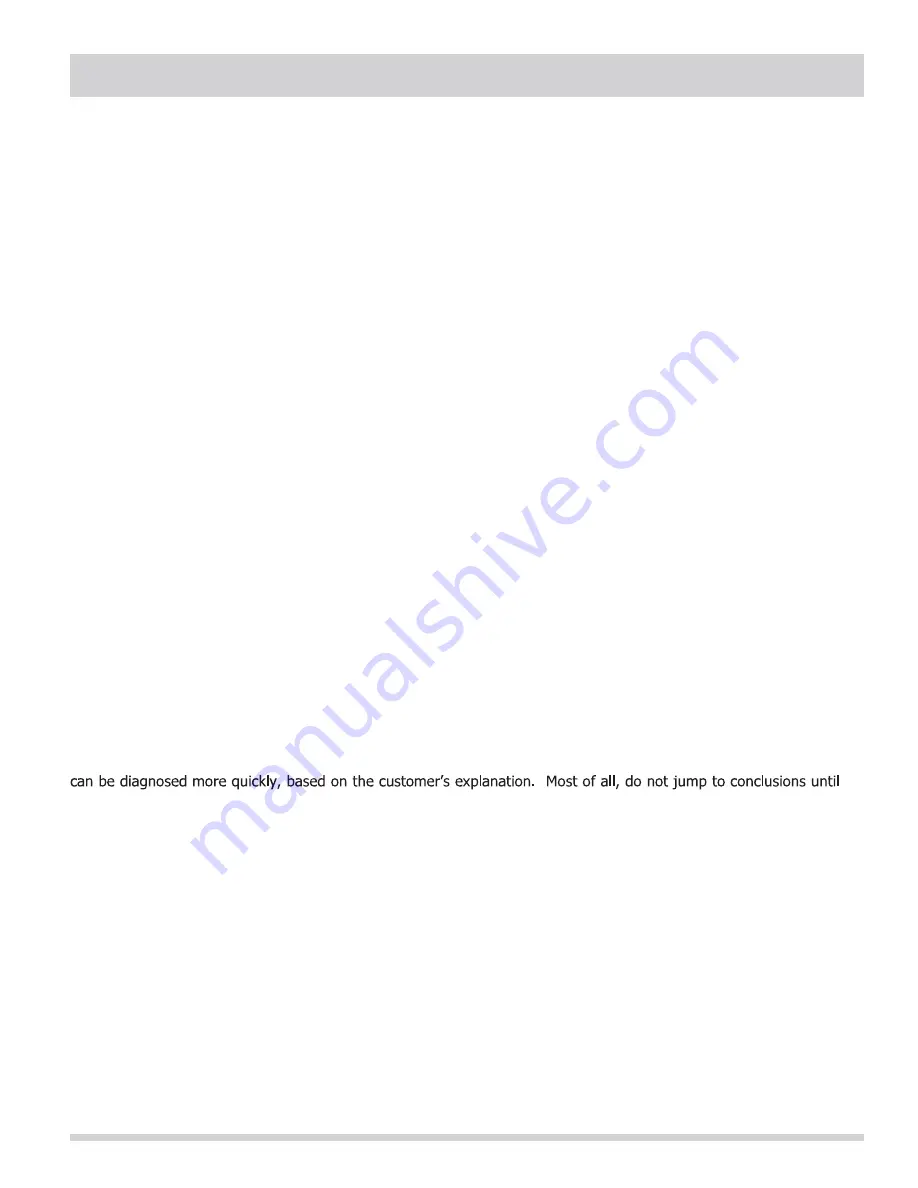
Section
5
Sealed System
5
-3
Safe Handling Practices for R-410A
1. Always wear protective goggles when working with refrigerant. If liquid refrigerant gets in your eye, permanent
blindness may result.
2. Do not allow refrigerant to come in contact with your skin. Refrigerant has a very low boiling point, which will
cause frostbite.
3. All refrigerant handling, charging, and recycling operations should be performed in locations with adequate
ventilation of at least four air changes per hour. Avoid prolonged breathing of the vapor. Prolonged inhalation of
refrigerant is extremely dangerous; death can occur without warning.
4. Do not use a recovery unit in the vicinity of spilled or open containers of gasoline, thinners, or any other
flammable liquid or vapor unless the equipment is expressly designed (explosion proof designs) for such
environments. Do not operate where flammable vapor is present.
5. Do not leave any recovery or recycling machine on and unsupervised.
6. Do not attempt to fill any vessels, containers, refrigerant tanks, charging equipment, or storage tanks that are not
D.O.T. approved and equipped with a safety-vent valve. Do not transfer refrigerant to non-refillable refrigerant
tanks.
7. Do not fill any storage tank or vessel with refrigerant beyond 80% of its capacity.
8. Do not disconnect or tamper with the electrical high-pressure, low-pressure, or liquid-level safety shut-off.
9. The pressure of R-410A is significantly higher than R-22. This does not mean that R-410A, or equipment
containing R-410A is unsafe, but it does mean you need tools and equipment that were designed for this higher
pressure. You must use AC equipment; refrigerant tanks and service tools have been re-engineered to handle the
higher pressure.
10. When servicing R-410A equipment make sure you use reversing valves, expansion valves, filter-driers, and other
components specifically designed for R-410A.
11. Refrigerant tanks used for new R-410A and recovered R-410A, have been redesigned for the higher pressure.
Service equipment must also be designed for R-410A:
High-pressure manifold gauge and hose sets (must have 4000 psi burst pressure and 800 psi working pressure).
High-pressure recovery machine certified for use with R-410A.
High-pressure recovery tanks, such as DOT 4BA400 or 4BW400.
Service Diagnostic Tips
A prime requisite on the initial contact is: Always allow the customer to explain the problem. Many times the trouble
you have heard the full story and have evaluated the information obtained from the customer. Then proceed with
your diagnosis.
Before starting a test procedure, connect the product service cord to the power source, through a wattmeter,
combined with a voltmeter. Then make a visual inspection and operational check of the air conditioner to determine
the following:
1. Is the product properly leveled?
2. Is the product located for proper dissipation of heat from the condenser? Check install location.
3. Feel condenser. With compressor in operation, condenser should be hot, with gradual reduction in temperature
from entry to exit of condenser.
4. Is evaporator fan properly located on motor shaft?
5. Is the thermostat sensing element properly positioned?
6. Observe frost pattern on evaporator.
7. Check control setting.
For air-conditioners, check room size, temperature, amount of people, windows, and other factors that increase the
load on the product. After this phase of diagnosis is completed, a thorough operational check should be made of the
refrigeration system.
Summary of Contents for AF-S100RX
Page 8: ......