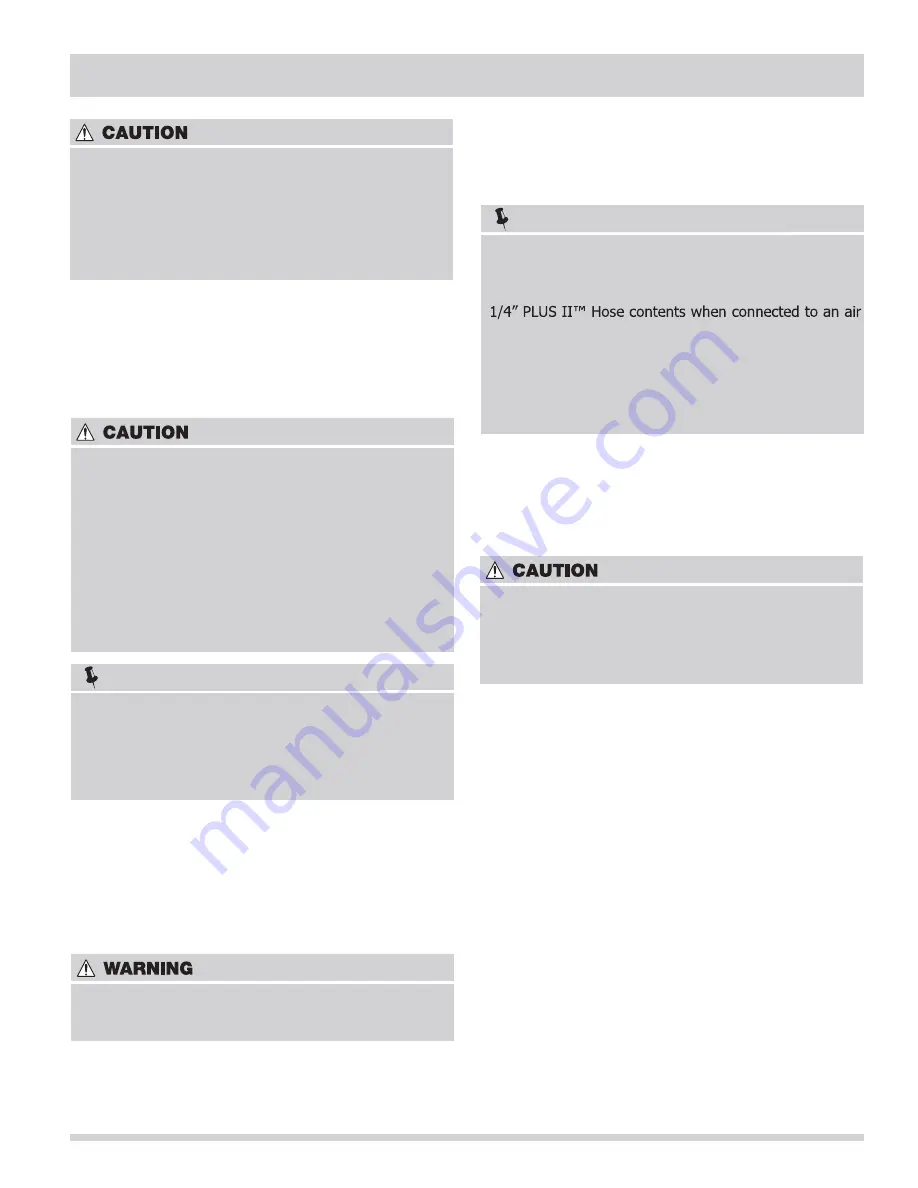
Section
5
Sealed System
5
-17
9. Close the manifold valve connected to the vacuum
pump. Watch the compound gauge for several
minutes. If the reading rises, there is a leak in
the system and must be repaired. If no leak is
indicated, stop the vacuum pump. The system is
now ready for recharging.
A. Recharging refrigerant tank must have at least
eight (8) ounces more refrigerant than required to
recharge.
B. Plug in heater blanket if needed, and bring pressure
up 30 pounds above gauge pressure at ambient
temperature. Do not exceed maximum temperatures.
If high vacuum equipment is used, just crack
both manifold valves for a few minutes and
then open slowly for the two full turns
counterclockwise. This will prevent the
compressor oil from foaming and being drawn
into the vacuum pump.
Check the serial plate for the correct refrigerant
type. It is extremely important to verify the
type of refrigerant in the system before starting
any sealed system repairs. After charging the
system with liquid, be certain to wait at least 5
minutes before starting the compressor to give
the refrigerant a chance to disperse throughout
the system. Otherwise the compressor could
be damaged by attempting to pump excessive
quantities of liquid.
ÒÑÌÛ
R410A systems should be liquid charged. This is done
via a dip tube in the refrigerant tank. However, if your
refrigerant tank does not have a dip tube then you
must invert the refrigerant tank to ensure only liquid is
transferred.
DO NOT HEAT REFRIGERANT TANK OVER 125°F
(52°C).
10. Use the Data Plate on the unit to determine amount
of refrigerant to be added, plus the .78 ounces that
is needed to allow for the addition of the filter-drier
to the sealed system. Set scale to zero.
11. Open refrigerant tank valve.
12. Open high side valve on manifold gauge set and
allow the predetermined amount of refrigerant to
flow into the sealed system, then close refrigeration
tank valve.
13. Allow system to sit for five minutes to allow for
pressure equalization.
14. Turn on air conditioner compressor. Run compressor
for a few minutes and monitor system pressures.
15. When satisfied unit is operating correctly, clamp the
process tube with pinch-off tool with the unit still
running. Using a tubing cutter, cut the process tube
about 2 inches from the pinch-off tool. Use Sil-fos
solder and solder process tube closed.
16. Turn off the product and allow the unit to set for
a few minutes. Check the process tube for
refrigerant leaks.
Final Leak Test
1. With the air conditioner turned OFF leak test all
low-side system components.
2. Turn unit ON and run until the condenser is warm.
Leak test the high-side system components.
Disconnect refrigerant tank heater blanket at
this time to prevent refrigerant tank pressure
from exceeding its maximum limits and
maximum temperature.
ÒÑÌÛ
When calculating refrigerant to be added during
recharging, the refrigerant remaining in the hoses must
be accounted for.
conditioning system (typical conditions):
Manifold red hose (subcooled LIQUID)
R-410A (0.29 ounces per foot)
Manifold blue hose (superheated VAPOR)
R-410A (0.011 ounces per foot)
Summary of Contents for AF-S100RX
Page 8: ......