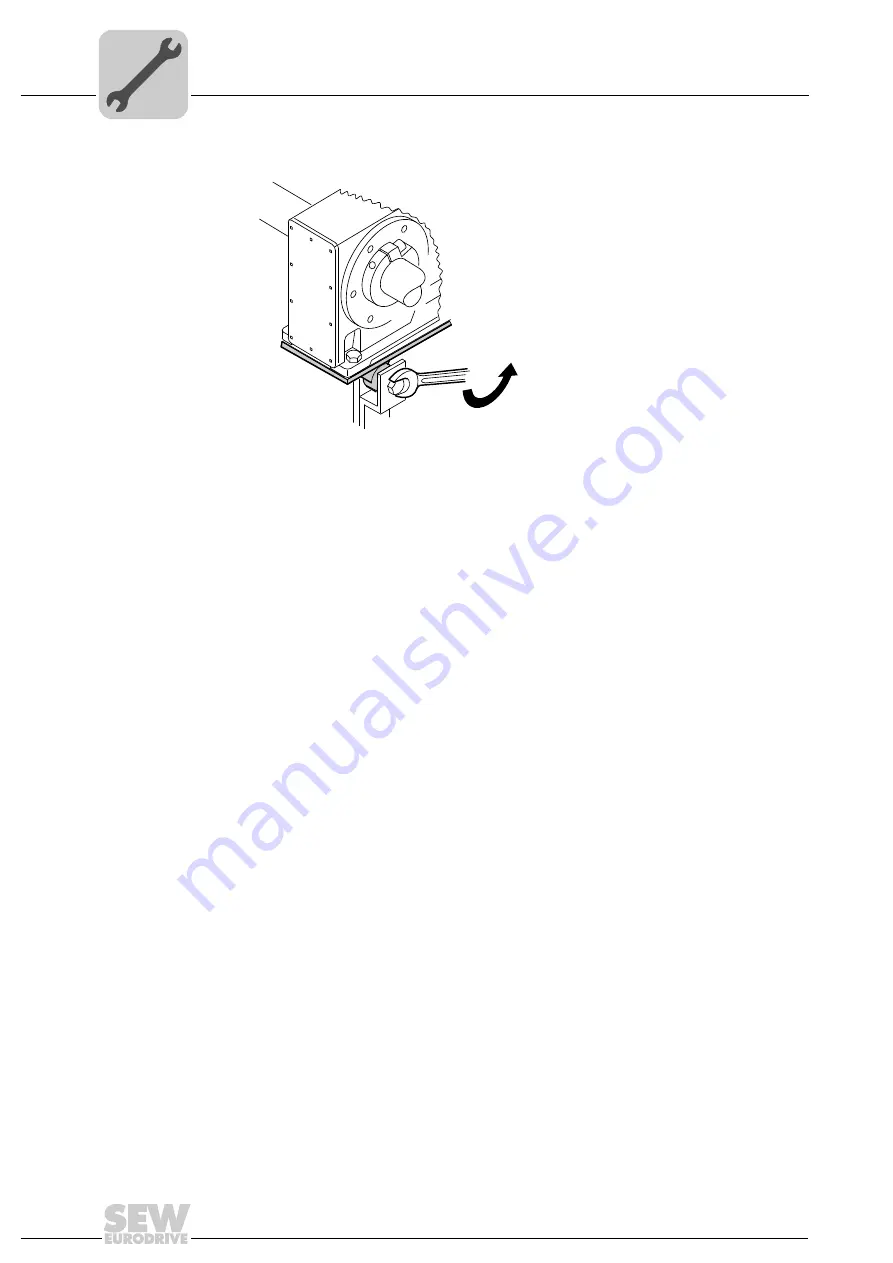
48
Assembly and Operating Instructions – Gear Units R..7, F..7, K..7, K..9, S..7, SPIROPLAN® W
4
Shaft-mounted gear units with TorqLOC
®
Mechanical Installation
18.Securely tighten the torque arm; observe chapter "Torque arm for shaft-mounted
gear units" (page 29).
5129142283
Artisan Technology Group - Quality Instrumentation ... Guaranteed | (888) 88-SOURCE | www.artisantg.com