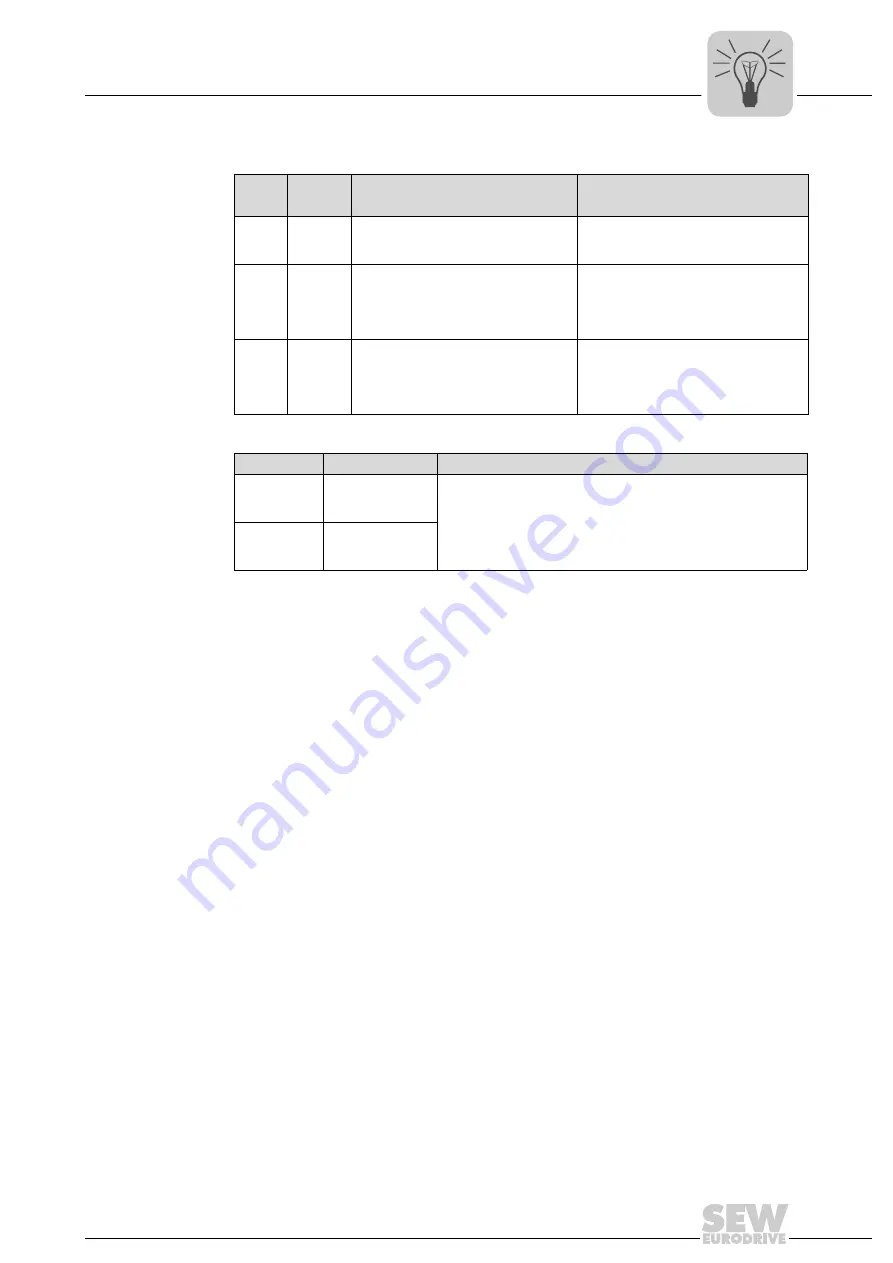
7
Operation
Status LEDs for MOVIFIT®-FC
Operating Instructions – MOVIFIT
®
-FC
119
"BUS-F" LED
The following table shows the statuses of the "BUS-F" LED:
"link/act 1" and
"link/act 2" LEDs
The following table shows the statuses of the "link/act 1" and "link/act 2" LEDs:
RUN
BUS-F
Meaning
Remedy
Green
Off
MOVIFIT
®
is currently exchanging data
with the PROFINET master (data
exchange).
-
Green
Flashing
green,
flashing
green/
red
The flashing function in the PROFINET
master configuration is activated to
visually localize the stations.
-
Green
Red
•
Connection to the PROFINET
master has failed.
•
MOVIFIT
®
does not detect a link.
•
Bus interruption
•
PROFINET master not in operation.
•
Check the PROFINET connection of
MOVIFIT
®
.
•
Check the PROFINET master.
•
Check all cables in your PROFINET
mains.
LED
Status
Meaning
link/act 1
Ethernet port 1
link = green
act = yellow
•
link = Ethernet cable connects device with other Ethernet
stations.
•
act = active, Ethernet communication active
link/act 2
Ethernet port 2
link = green
act = yellow
Summary of Contents for MOVIFIT-FC
Page 2: ...SEW EURODRIVE Driving the world ...
Page 169: ......
Page 170: ......
Page 171: ...SEW EURODRIVE Driving the world ...