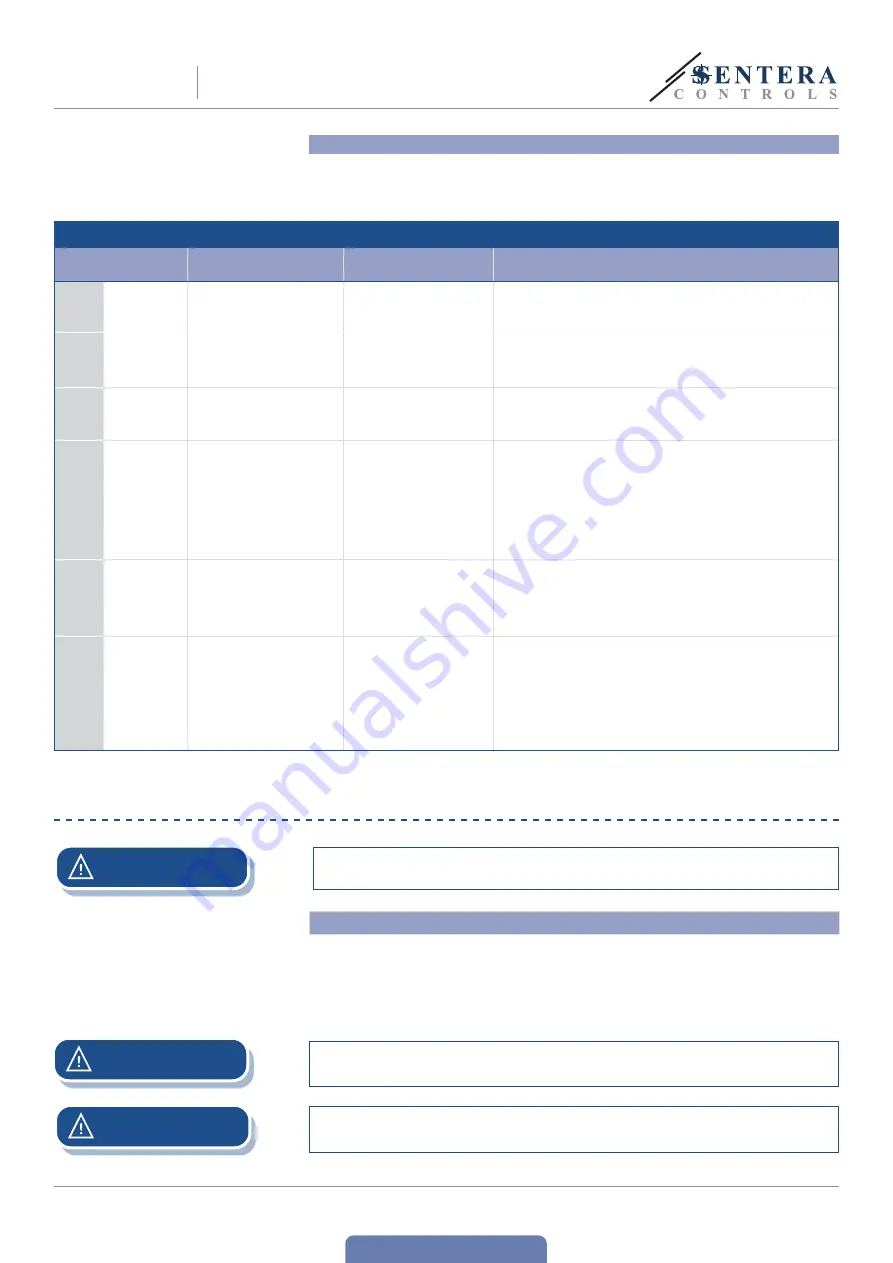
www.sentera.eu
MIW-RTVS1-EN-000 - 03 / 11 / 2020
11 - 12
TRANSFORMER FAN SPEED CONTROLLER WITH
MODBUS RTU COMMUNICATION
RTVS1
Explanation of specific Modbus registers
The unit has factory pre-set parameters written in Modbus map. It can function
without any other settings. However, there are some special registers you may need
to set depending on you combination of products. These are listed in
Table 2
below.
Table 2 Voltage steps
Modbus holding
registers
Description
Values
Remark
11
Control Set
Automatic control – takes value
from sensor. Manual Control –
takes value from register 12
Auto Forward mode;
Manual mode;
Auto Reverse mode
It is possible to change the control of the article only when the switching
of the current command has finished.
13
Output Update
Interval
Time delay to update the
output in automatic mode
5 s—600 s
If the value of the sensor connected is changing too fast this is the
register that provides control of the time between two consecutive
switching.
16
Hysteresis delta
The difference between
the upwards switching and
downwards switching step
percentage
2—10 %
This value is subtracted from the threshold when the article is switching
from high to low input value. Hysteresis value is 2 – 10%, it means for
threshold 20%, the “threshold – hysteresis” = 18% for Δ = 2%.
17
Communication
Lost Output
State
Set output when Modbus
communication is lost
OFF;
Last step selected
Set to 0 = OFF, when there is Modbus Timeout set, when the device
encounters Timeout - RTVS1 enters STOP mode, output is
0. If the remote sensor is lost – device enters state 0 = OFF. Both
communications lost, article goes to OFF.
When set to 1 = Last step selected, on Modbus Timeout occurrence and
sensor is connected – article continues to operate in regarding of the
input from the sensor, if sensor is lost – the article stays on the last
step selected. If both communications are lost, device stays on the last
step selected.
In Auto modes, if there is no communication to the control/monitoring
station, the article continues to operate autonomously while the sensor
is connected.
18
Sensor output
register value
number
Select which sensor output will
be used as input to the device
Digital potentiometer;
Temperature;
Relative Humidity;
CO
2
/CO
2
eq;
CO/TVOC;
NO
2
Sensor output register value number, define which sensor value will be
taken for control of the device switching. The restrictions that apply
are for Sentera Sensors only, and the SPV device. When SPV device is
connected this value becomes automatically 1 and cannot be changed
until other sensor is connected.
21—25
Input value
step 1—5
Input value to switch to output
steps 1—5
Switches to output step X at
X % input value and steps
down to output previous step
at X % - Hysteresis delta
(HR16) set
Input Value Step X – the steps will be activated over these thresholds.
If register value is 0 – this step will be skipped as a holding step, but
it will be used as intermediate step if needed to switch to upper/lower
step. Minimum difference between steps thresholds is 11%, that way any
overlapping of the switching and the hysteresis is avoided.
VERIFICATION OF INSTALLATION
Use only tools and equipment with non-conducting handles when working on
electrical devices.
ATTENTION
Safe operation depends on proper installation. Before start up, ensure the following:
■
The mains supply is connected correctly.
■
Protection is provided against electrical shock.
■
The cables are the appropriate size and fuse-protected.
■
There is sufficient air flow around the unit.
ATTENTION
The unit is supplied with electrical energy at voltages high enough to inflict personal
injury or threat to health. Take the relevant safety measures.
ATTENTION
Disconnect and confirm that there is no live current flowing to the unit before servicing.