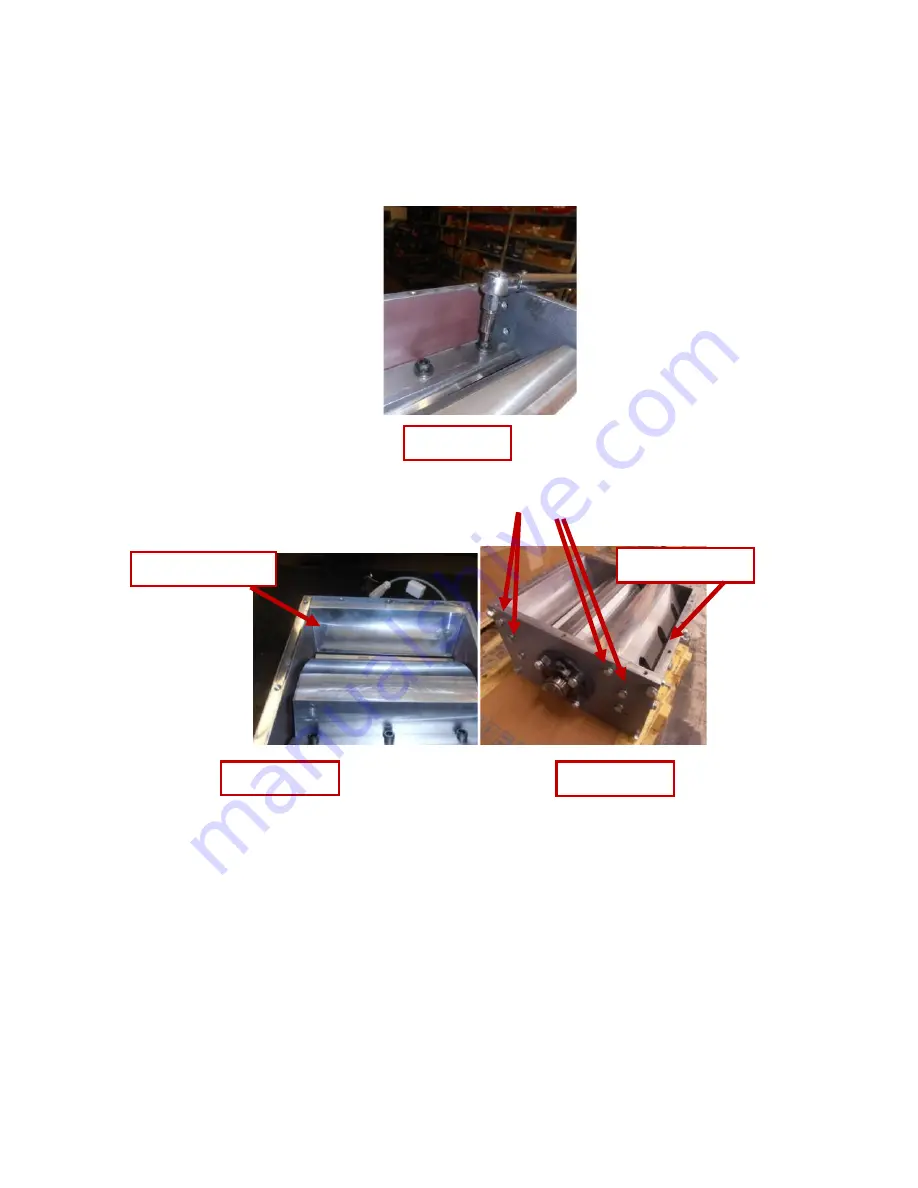
29
508.366.1488 | www.semshred.com
10.
Torque bed knives to 45-50 ft./lbs.
o
Requires torque 5/16” Allen drive socket bit.
o
Torque wrench should not be used as a socket wrench and should be calibrated to ensure proper
tightening to avoid damage. SEM offers a complete toolkit for this system.
o
Double check knife clearance after torqueing bolts.
11.
Attach front and rear deflectors as shown with eight 5/16”-18 x 1 1/4" hex bolt and 5/16” lock washer.
Requires 1/2" wrench
12.
Do a final check of bolt torques, assembly bolt tightness, and knife gapping.
Warning:
Failure to sharpen or replace knives will result in excess dust, frequent jamming of stage 2 chamber,
reduced throughput, excess vibration, and increased noise throughout the device.
Re-sharpening:
Knives can be re-sharpened 2-3 times provided they are not significantly damaged or worn. Knives
must be sharpened as a complete set
(two bed knives, three rotor knives). Contact SEM Customer Service for
details or for replacement knives.
Front Deflector
Rear Deflector
Figure 10
Figure 11
Figure 12