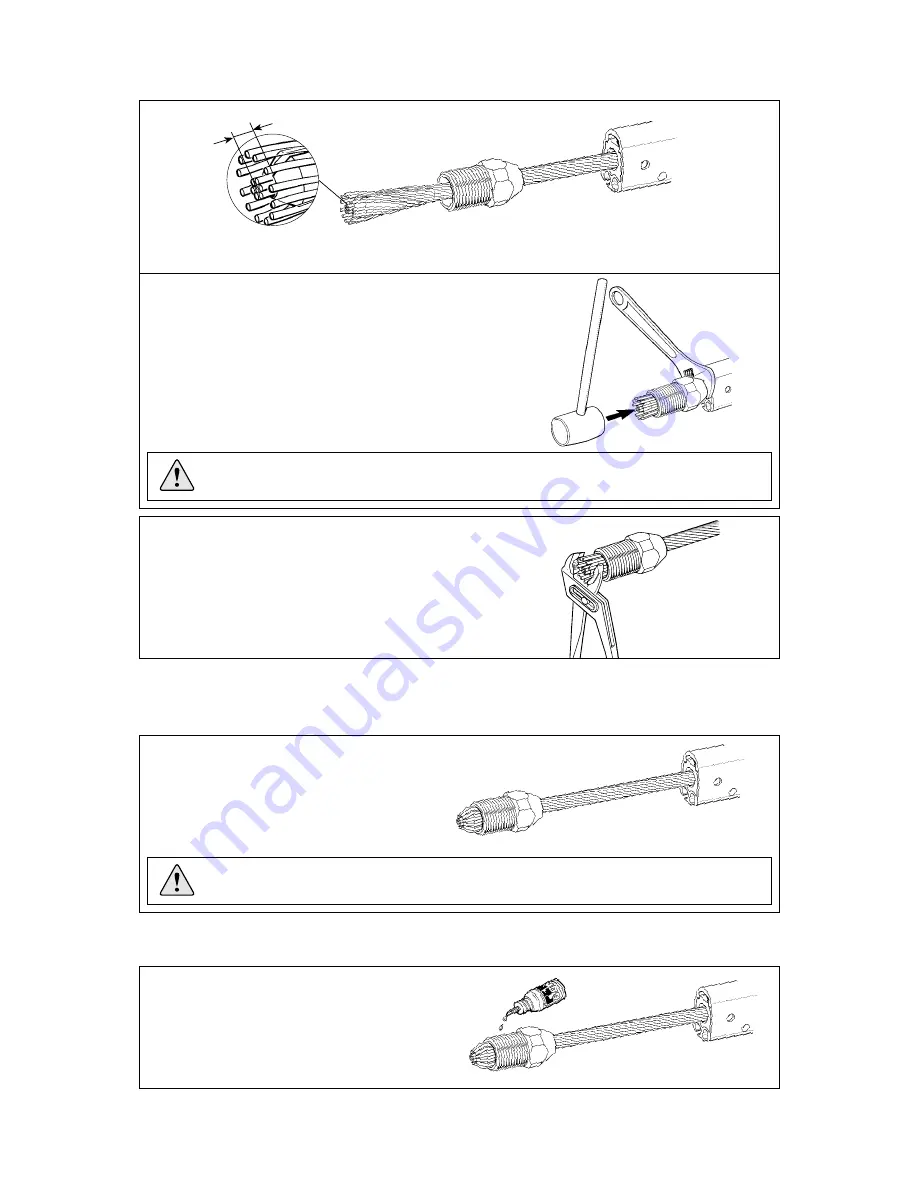
19
9.
Slide the wedge over the core (7 strands) of the wire . The core of the wire should protrude approx.
3 mm (1/8”) from the wedge.
10.
Remove the adhesive tape from the top eye terminal. Space the outer
strands of the wire evenly around the wedge and bring down the
socket so that the strands are held in place. Hold an adjustable
spanner between the 1000 mm extrusion and the socket. Tapping the
core of the wire, locate it firmly in the socket.
Check that the core of the wire protrudes approx. 3 mm (1/8”)
from the wedge. See fig. 4.2.c.
11.
Bend the outer strands inwards a little using a pair of pliers,
or tap the strands with a small hammer. In the latter case,
rest the socket’s thread on a soft surface (wood or similar) to
prevent damage.
NOTE! Check that no strands slip into the slot of the wedge.
13.
Unscrew and check that the outer strands are
evenly distributed around the wedge. If some
strands are crossed, correct their positions.
NOTE! Check that no strand has slipped into the slot of the wedge!
14. If assembly is unsuccessful and needs to be repeated, refer to the relevant sections of Chapter 17,
”Dismantling the Furlex”
.
Fig. 4.2.c
Fig. 4.2.d
Fig. 4.2.n
Fig. 4.2.e
15.
Apply another 2 or 3 drops of the locking
adhesive to the thread and screw the terminal
together, tightening it firmly. The terminal is
now permanently locked.
Fig. 4.2.f
3 mm
12. Insert the former into the threaded hole of the terminal part (or rigging screw). Lubricate the
socket´s thread with a long bead of locking adhesive. Screw the terminal part onto the socket and
tighten carefully, forcing the wire further into the terminal.