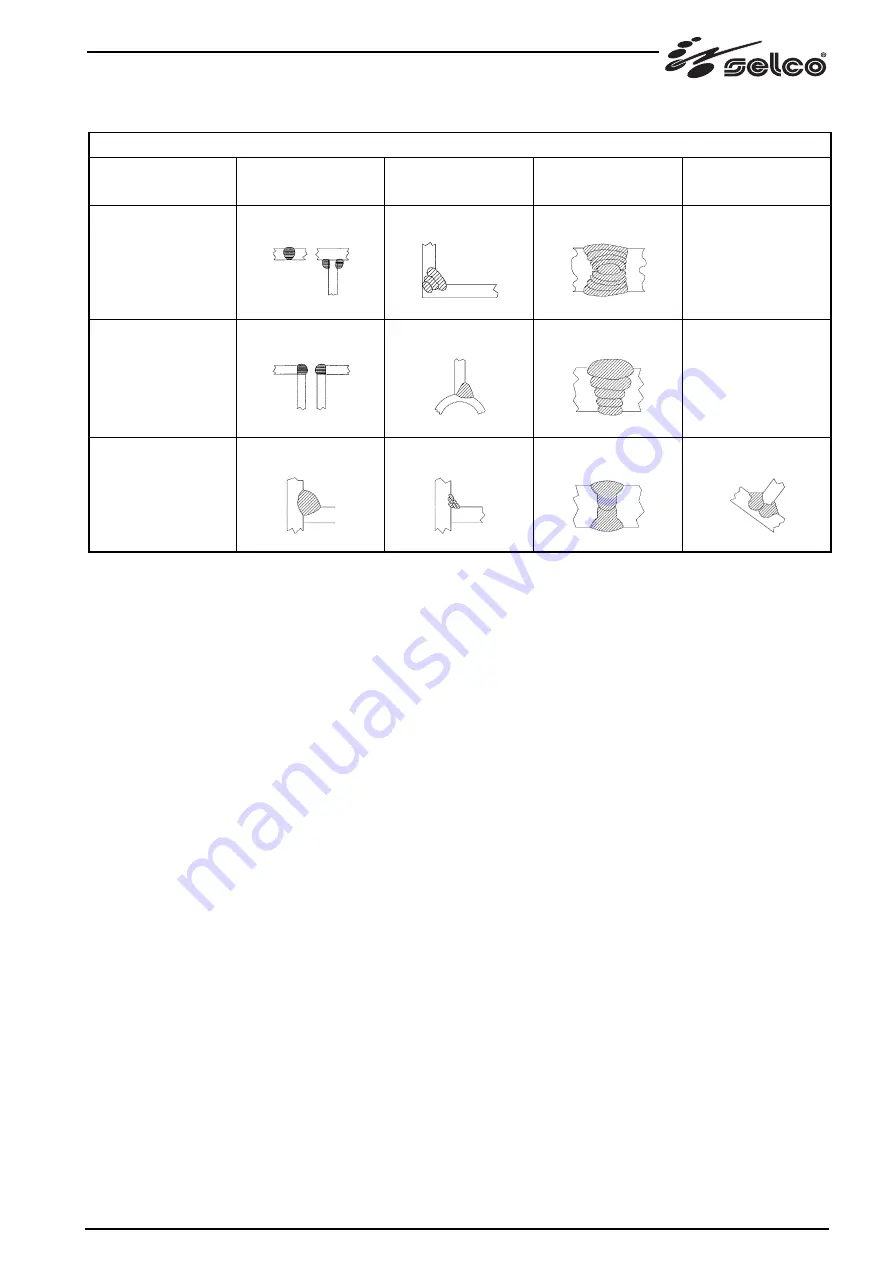
59
SELECTION GUIDE OF WELDING PARAMETERS WITH REFERENCE TO THE MOST TYPICAL APPLICATIONS AND MOST
COMMONLY USED WIRES
Wire diameter - weight per metre
Voltage
arc (v)
0,8 mm
1,0-1,2 mm
1,6 mm
2,4 mm
Low penetration for thin
materials
60 - 160 A
100 - 175 A
Good penetration and
melting control
Good flat and vertical
melting
Not used
16 - 22
SHORT - ARC
24 - 28
GLOBULAR-ARC
(transition area)
30 - 45
SPRAY - ARC
120 - 180 A
Automatic welding down-
wards
250 - 350 A
Automatic welding
with high voltage
200 - 300 A
Automatic fillet welding
150 - 250 A
Low penetration with
adjustment to 200 A
150 - 250 A
Automatic welding
with multiple runs
200 - 350 A
Good penetration
downwards
300 - 500 A
Good penetration, high
deposit on thick materials
500 - 750 A
150 - 200 A
Not used
300 - 400 A
Gases
MIG-MAG welding is defined mainly by the type of gas used: inert for MIG welding (Metal Inert Gas), active for MAG welding
(Metal Active Gas).
- Carbon dioxide (CO2)
Using CO2 as a shielding gas, high penetrations and low operating cost are obtained with high feeding speed and good mechani-
cal properties. On the other hand, the use of this gas creates considerable problems with the final chemical composition of the
joints as there is a loss of easily oxidisable elements with simultaneous enrichment of carbon in the weld pool.
Welding with pure CO2 also creates other types of problems such as excessive spatter and the formation of carbon monoxide porosity.
- Argon
This inert gas is used pure in the welding of light alloys whereas, in chrome-nickel stainless steel welding, it is preferable using
argon with the addition of oxygen and CO2 in a percentage of 2% as this contributes to the stability of the arc and improves the
form of the bead.
- Helium
This gas is used as an alternative to argon and permits greater penetration (on thick material) and faster wire feeding.
- Argon-Helium mixture
Provides a more stable arc than pure helium, and greater penetration and travel speed than argon.
Argon-CO2 and Argon-CO2-Oxygen mixture
- These mixtures are used in the welding of ferrous materials especially in SHORT-ARC operating mode as they improve the specific
heat contribution. They can also be used in SPRAY-ARC. Normally the mixture contains a percentage of CO2 ranging from 8% to
20% and O2 around 5%.
Summary of Contents for Genesis 3200 GSM
Page 32: ...32...
Page 90: ...90...
Page 120: ...120...
Page 150: ...150...
Page 180: ...180...
Page 210: ...210...
Page 326: ...326 1 3 1 4 11 35 1 5 1 6...
Page 327: ...327 8 1 7 EN IEC 60974 10 B A A EN60974 10 A pace maker Zmax Ssc Point of Commom Coupling PCC...
Page 328: ...1 8 IP S IP23S 12 5 mm 60 2 2 1 2 2 10 2 3 400V 230V 15 15 2 1 5 328...
Page 344: ...5 6 Reset 344...
Page 345: ...345 encoder...
Page 346: ...346...
Page 347: ...347 7 7 1 MMA Hot Start Arc Force antisticking 7 2 TIG TIG Tungsten lnert Gas 3370 C H F lift...
Page 352: ...352...
Page 357: ...357...
Page 360: ...360...