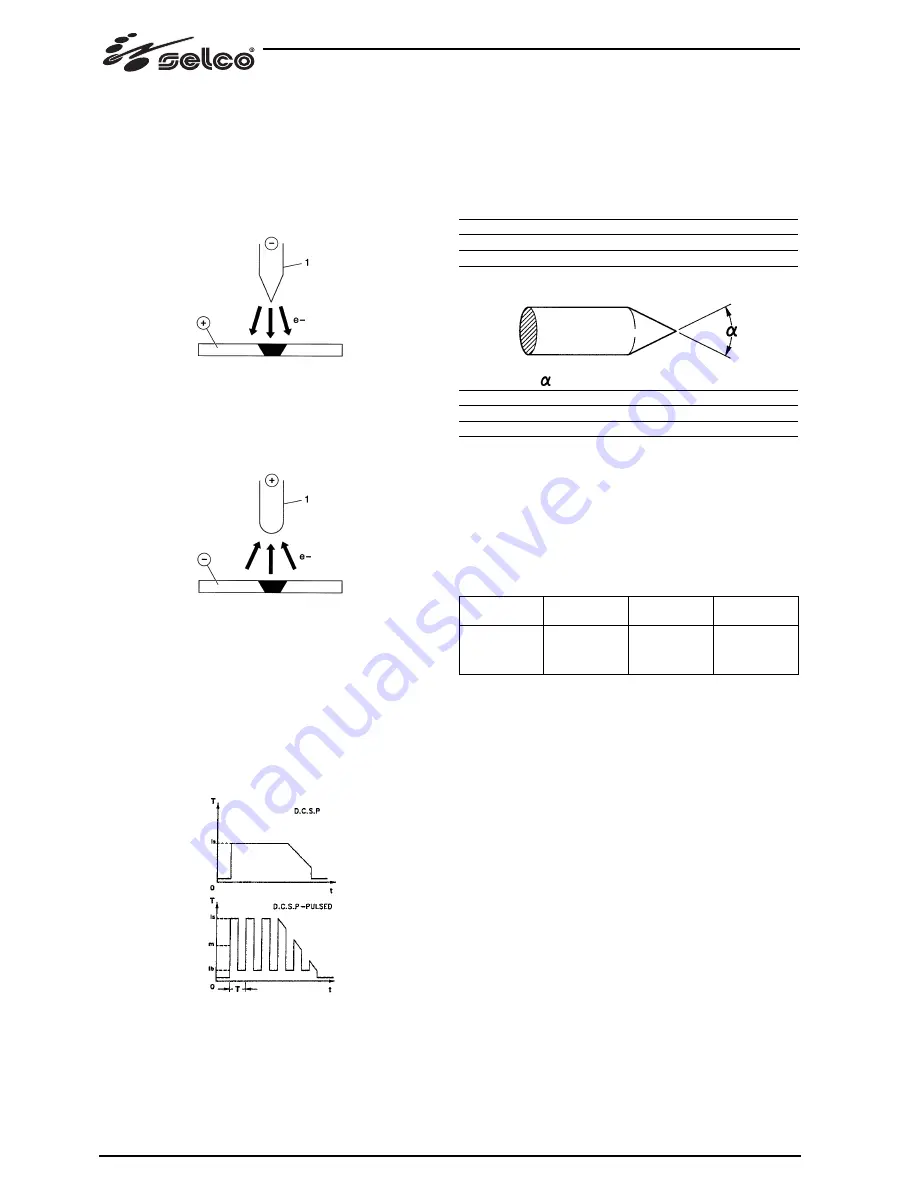
48
Welding polarity
D.C.S.P. (Direct Current Straight Polarity)
This is the most used polarity and ensures limited wear of the
electrode (1), since 70% of the heat is concentrated in the
anode (piece).
Narrow and deep weld pools are obtained, with high travel
speeds and low heat supply.
Most materials, except for aluminium (and its alloys) and mag-
nesium, are welded with this polarity.
D.C.R.P. (Direct Current Reverse Polarity)
The reverse polarity is used for welding alloys covered with a
layer of refractory oxide with higher melting temperature com-
pared with metals.
High currents cannot be used, since they would cause excessive
wear on the electrode.
D.C.S.P.-Pulsed (Direct Current Straight Polarity Pulsed)
The use of pulsed direct current allows better control, in particu-
lar operating conditions, of the welding pool width and depth.
The welding pool is formed by the peak pulses (Ip), while the
basic current (Ib) keeps the arc ignited.
This operating mode helps to weld thinner metal sheets with
less deformations, a better form factor and consequently a lower
danger of hot cracks and gas penetration.
Increasing the frequency (MF) the arc becomes narrower, more
concentrated, more stable and the quality of welding on thin
sheets is further increased.
7.2.1 Steel TIG welding
The TIG procedure is very effective for welding both carbon and
alloyed steel, for first runs on pipes and for welding where good
appearance is important.
Straight polarity is required (D.C.S.P.).
Preparing the edges
Careful cleaning and preparation of the edges are required.
Choosing and preparing the electrode
You are advised to use thorium tungsten electrodes (2% thorium-
red coloured) or alternatively cerium or lanthanum electrodes
with the following diameters:
Ø electrode (mm)
current range (A)
1.0
15÷75
1.6
60÷150
2.4
130÷240
The electrode must be sharpened as shown in the figure.
(°)
current range (A)
30
0÷30
60÷90
30÷120
90÷120
120÷250
Filler metal
The filler rods must have mechanical characteristics comparable
to those of the parent metal.
Do not use strips obtained from the parent metal, since they
may contain working impurities that can negatively affect the
quality of the welds.
Shielding gas
Tipically, pure argon (99.99%) is used.
Welding
current (A)
6-70
60-140
120-240
Ø Electrode
(mm)
1.0
1.6
2.4
Gas nozzle
n° Ø (mm
)
4/5 6/8.0
4/5/6 6.5/8.0/9.5
6/7 9.5/11.0
Argon flow
(l/min)
5-6
6-7
7-8
7.2.2 Copper TIG welding
Since TIG welding is a process characterized by high heat con-
centration, it is particularly suitable for welding materials with
high thermal conductivity, like copper.
For TIG welding of copper, follow the same directions as for TIG
welding of steel or special instructions.
Summary of Contents for Genesis 284 PSR
Page 50: ...50...
Page 76: ...76...
Page 102: ...102...
Page 198: ...198...
Page 270: ...270...
Page 274: ...274 1 3 1 4 11 35 1 5...
Page 275: ...275 1 6 8 1 7 EN IEC 60974 10 B A A EN60974 10 A pace maker Point of Commom Coupling PCC...
Page 276: ...1 8 IP S IP23S 12 5 mm 60 2 2 1 2 2 10 2 3 400V 15 15 2 1 5 276...
Page 277: ...277 2 4 MMA 1 2 3 4 TIG 1 2 TIG 3 4 1 2 3 4...
Page 284: ...284 3 9 1 50 1 3 3a 3b 3c 3d 3e 2 encoder 1 1 4 encoder encoder 1 4 4 3 encoder 2...
Page 290: ...290 4 5 MT300 5 6...
Page 291: ...291 Reset encoder...
Page 292: ...292...
Page 296: ...296...
Page 300: ...GENESIS 504 PSR 300...
Page 304: ...304...