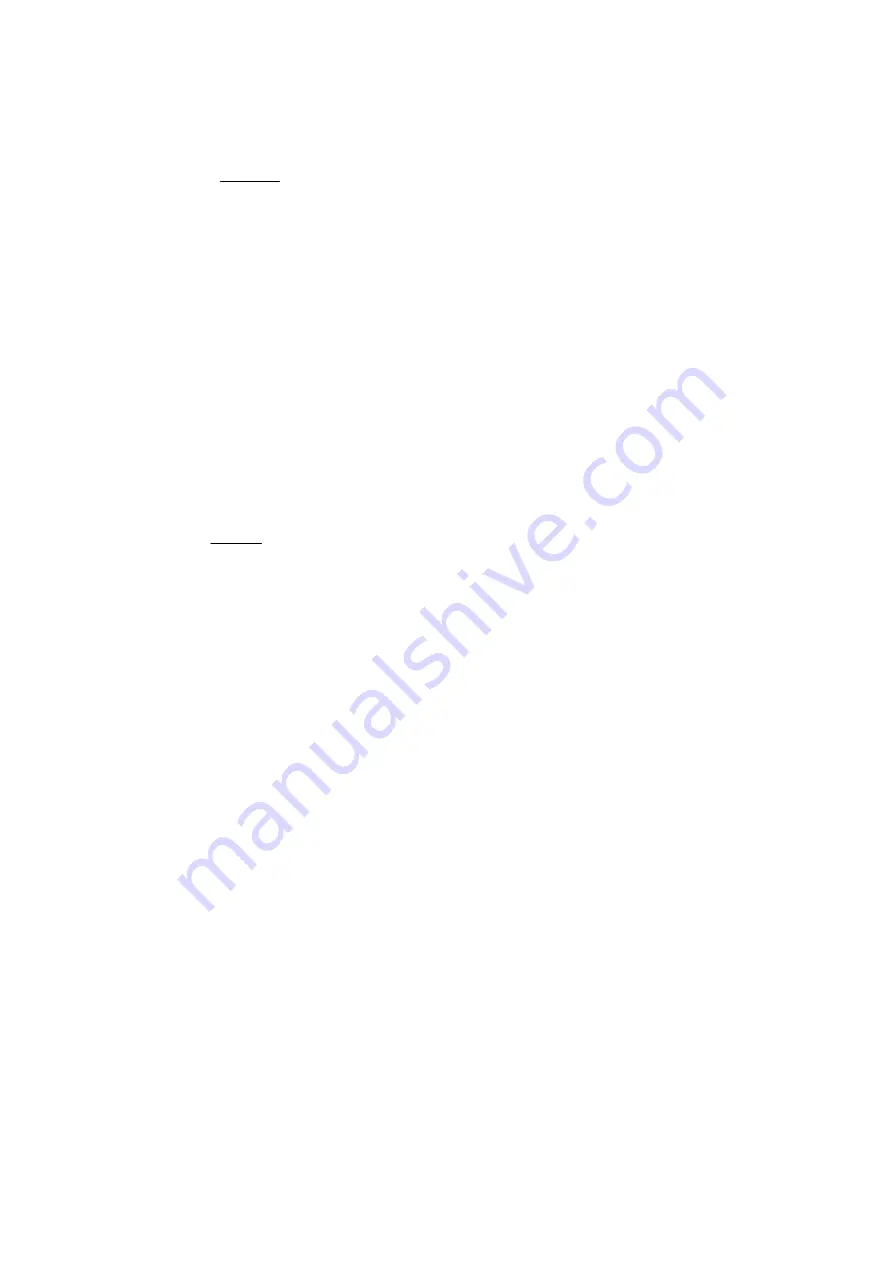
3-9
3. Find the number of row (an) to decelerate from current acceleration step number to next step by
substituting the calculated acceleration step number into the following equation.
"an" should be rounded off to an integer.
n
Yn)
-
(Y
=
an
an:
Number of row to decelerate from current acceleration step number to next step
Y:
Current acceleration step number (=Current acceleration step time)
Yn:
Acceleration step number at "n"th step ahead (=Acceleration step time at "n"th
step
ahead
n:
Step to decelerate (n=1,2,3…,40)
(For example : LTPD247)
For example: If there is a dot line which holds the maximum value of "an" at 20th step ahead from the current step.
1 The calculated pulse width is assumed as t=0.888msec.
2 Find the acceleration step number from Table3-4.
Current acceleration step time of motor
:
313
μ
s -> Acceleration step number=120
Calculated acceleration step time of motor
:
445
μ
s -> Acceleration step number=60
(Necessary acceleration step time based on the calculated activation pulse width is 0.888/2
×
1000
=
444
μ
s
The nearest acceleration step time which is longer than 444
μ
s and smallest is 445
μ
s.)
3 Find the number of row of acceleration step to decelerate from current acceleration step number to next step (an) using the
following
equation.
a20=
20
60)
(120
−
=3
According to the maximum value a20=3 by calculated value of "an" (a1 to a40), next acceleration step time of the next step
should be 317
μ
s at the 117th acceleration step which reduced the row by three rows from the current 120th acceleration step.
If the actual thermal head activation time exceeds the estimated acceleration step time, drive the printer
drive motor so that the motor driving composition of 1st step at 1st dot line and 2nd step at 1st dot line
divides the thermal head activation time equally.
(4) Reacceleration
control
Follow the procedure below if :
Unable to accelerate the speed due to deceleration control.
The speed has been reduced at a certain speed and then accelerates the speed again.
The next step time after reducing the speed is the nearest acceleration step time, which should be
shorter than the previous acceleration step time and longest.
(For example : LTPD247)
According to Table 3-4, if the motor acceleration step time of the previous step is 900
μ
s, the next step should be the 16th
acceleration step (885
μ
s).
Hereinafter, accelerate the speed sequentially up to the maximum motor drive pulse rate P
M
according to
Table 3-4 or Table 3-5.