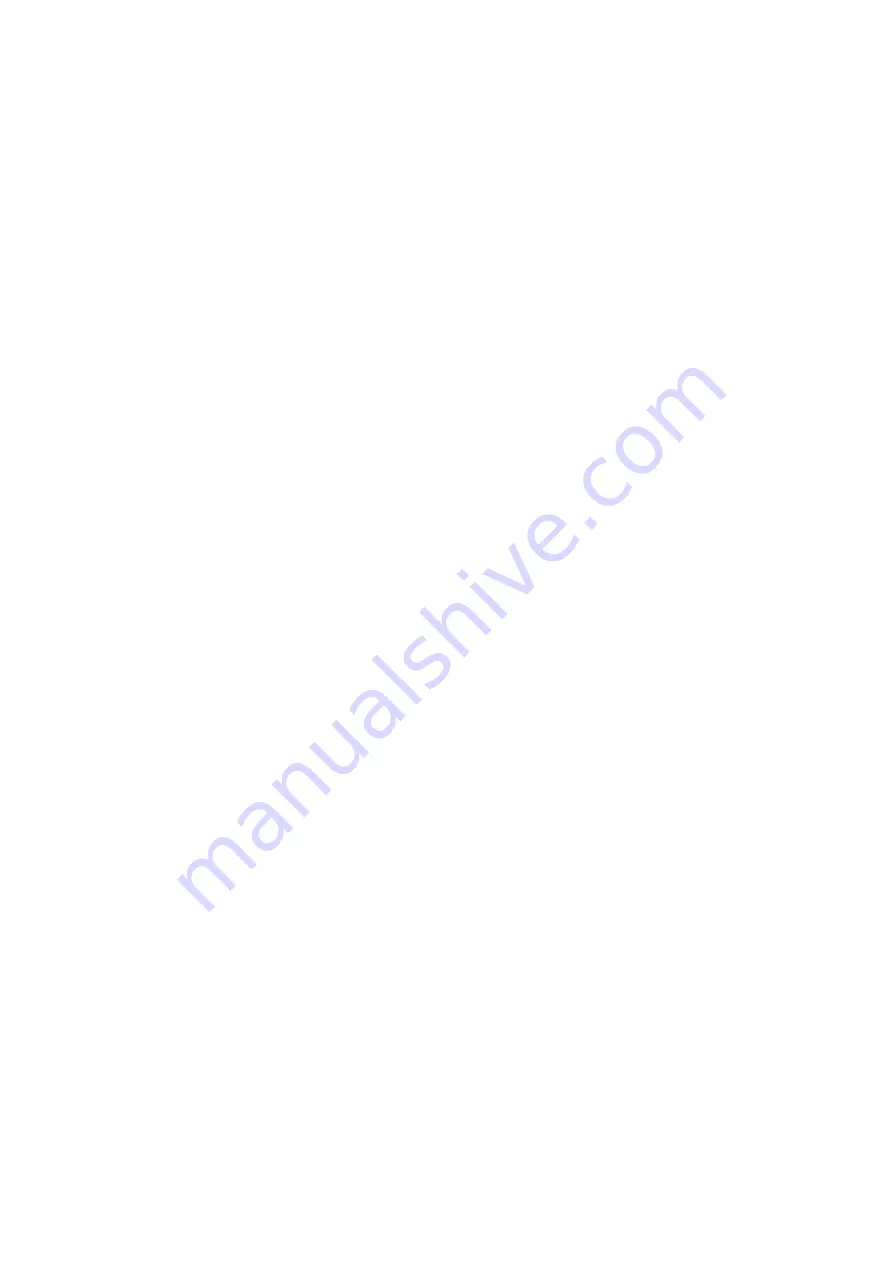
3-8
3.3.5 Motor
Drive
Method
Drive the motor by the following methods.
(1) Motor drive pulse rate
During paper feeding, the motor should be driven equal or lower the following maximum motor drive
pulse rate.
LTPD247 Maximum motor drive pulse rate (P
M
) : 3200 pps
LTPD347 Maximum motor drive pulse rate (P
M
) : 2400 pps
(2) Acceleration
control
When driving the motor, the acceleration control is required to maintain the paper feed force of start up.
If acceleration of the motor does not perform correctly, the motor may step out if it has a heavy workload.
Accelerate the speed sequentially up to the maximum motor drive pulse rate P
M
according to the Table
3-4 or Table 3-5 Acceleration Steps.
Acceleration should be performed by the acceleration step time below, that is output the phase.
1. Drive the start step as same as acceleration step time at Start acceleration step.
2. Drive the first step as same as acceleration step time at 1st acceleration step.
3. Drive the second step as same as acceleration step time at 2nd acceleration step.
4. Hereinafter, drive the "n"th step as same as acceleration step time at "n"th acceleration step.
5. After accelerating up to the maximum motor drive pulse rate P
M
, drive the motor at a constant speed.
Available to print during acceleration.
(3) Deceleration
control
The activation time of the thermal head may be longer than the motor step time depending on the type of
the thermal paper, content of the printing and use conditions. In that case, decelerate the motor speed by
extending the acceleration step time until the thermal head activation has been completed.
In the case of reducing the motor speed, the deceleration control based on the estimated motor speed is
required for preventing paper feed failure caused by the steep change of the motor speed. Decelerate
the speed properly, otherwise the motor may not rotate properly due to the steep change of the motor
speed.
To prevent the steep change of the motor speed, follow the deceleration method as shown below.
Every dot line, predict the dot line that needs to decelerate after the next step.
The predicted range is 20 dot lines (40 steps) ahead from the next step.
If there is/are the dot line(s) that need(s) to decelerate, find the number of row (=an) for decelerating at
the next step from the current acceleration step number.
Determine the next acceleration step time (= acceleration step number) based on the maximum value of
calculated "an" (a1 to a40).
Find each "an" from the next step to the 40th step by following the procedure.
1. Find the thermal head activation time based on the equation of "3.5.1 Calculation of Activation Pulse
Width".Calculate the Printing energy(E) and Adjusted voltage (V) using the temperature detected by
thermistor and the thermal head drive voltage at that time.
Calculate the Activation cycle(W)(the time from the start of the preceding activation to the start of the
current activation) using "an" which is found at the previous step.
If an
≤
0 such as during acceleration or driving constantly at maximum speed, use an=0.
2. Find the current acceleration step on Table 3-4 or Table 3-5, and then find the nearest acceleration
step number which is longer than a half of the calculated thermal head activation time and smallest.