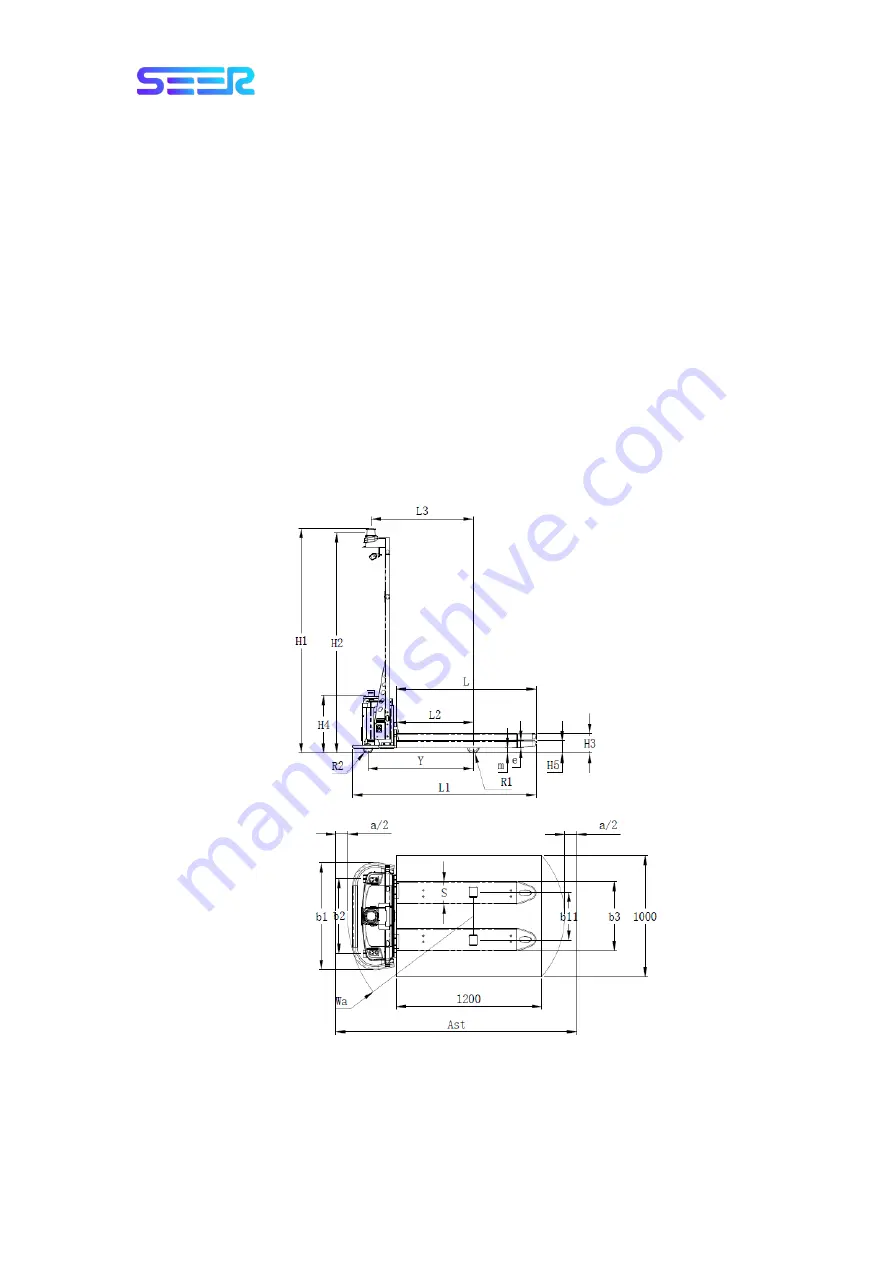
3. Product Introduction
SMF-MP10S User guide V1.1 Shanghai Seer Intelligent Technology Corporation
8
3. Product Introduction
3.1 Overview
SMF-MP10S (Seer Mini Fork) is a laser SLAM mini automatic forklift. The product provides
core map building, positioning and navigation functions to help users quickly realize various
applications of mobile robots.
This product is developed and manufactured by Shanghai Seer Intelligent Technology
Corporation. All rights © are reserved by Shanghai Seer Intelligent Technology Corporation.
Although some names in this document and possible other names are not marked with the
registered trademark symbol®, but they are registered trademarks of Shanghai Seer
Intelligent Technology Corporation, including
仙工智能
, SEER and SRC.
3.2 Product Dimensions
3.2.1 Dimensions of Robot