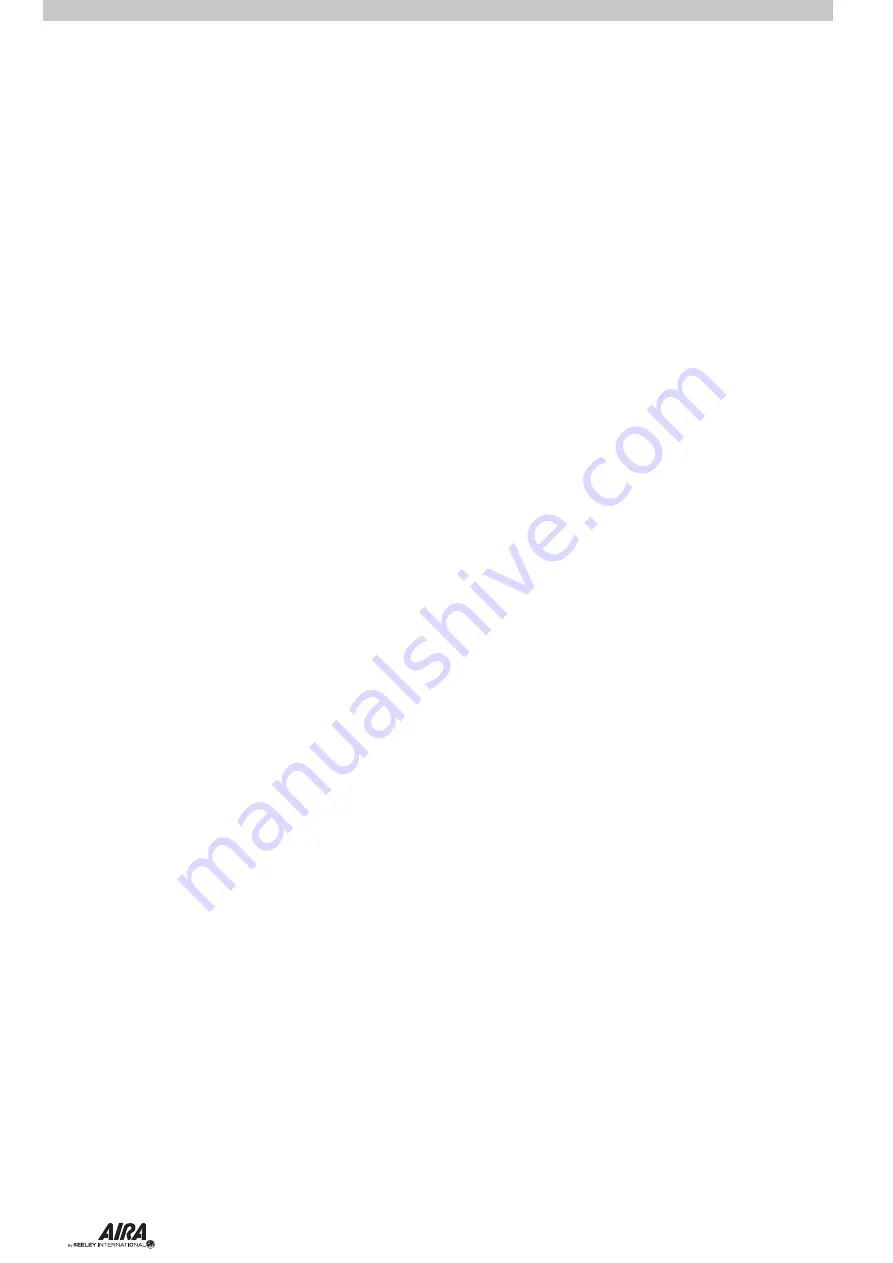
24
|
COMMISSIONING INFORMATION
4.6 SETTING PAD SATURATION
1.
Locate the water adjuster/taps. Depending on the cooler model there could be up to four pumps installed in the
unit. The discharge line from each pump line will have a dedicated adjuster/tap.
2.
If the unit is new, then the pump flow rate adjuster/tap will likely be found to be in the ½ open position.
3.
The evaporative unit must be installed, plumbed and float levelled as per Seeley International instructions. The
airflow rate should be adjusted to meet specifications.
4.
Pre-set each of the adjustor/taps to the ½ open position and fit all pad frames into place.
5.
Start the unit fan on high speed and turn on the pumps. All pad frames should now be fitted such that water is
flowing to each pad but is not subject to draw-off or carryover around the pad frames. Always check for signs of
splashing on interior unit components.
6.
The filter pads on the operating unit must now be observed. Check the outside of the unit for signs that the pads
are becoming damp. It may take a few minutes for dampness to appear.
7. After 10 minutes check the running unit again. Take note of any pads that still have dry sections. Stop the unit,
remove the filter pad/s that provides access to the respective adjuster/tap and open the flow adjuster/tap slightly for
any pad(s) that were found to be dry. Never adjust the water flow rate with the unit running.
8.
If a pad has been found to be very wet, and in danger of flooding, then close the corresponding adjuster/tap a small
amount and re-test.
9.
Continue these procedures until all the pads are just damp and no flooding is visible on the pads. Stop the unit and
check for signs of water draw-off or carry-over inside the unit (ie. water droplets on pulleys, motor, bearings, scroll,
impeller etc.) If carry-over has occurred then adjust (reduce) the water flow to the respective pad(s) and restart the
unit.
10.
The aim is to have all the pads suitably damp but not flooded.
11.
Continue this procedure until suitable wetting has been achieved.
Notes:
a). The filter pad evaporation rate changes with entering air (ambient) conditions. The water flow rate should be set
with this in mind and may have to be readjusted later due to seasonal weather changes.
b). When performing scheduled maintenance it is recommended that the flow rate for each pump should be checked.
c). The electrical current flow to the fan motor should be verified to ensure that it falls within the rating specified on the
fan motor nameplate
d). Excessive airflow can cause water carryover by increasing the pad’s face velocity. Airflow should remain within the
maximums specified for the unit.
e) Filter pads with obstructed or blocked passages are more prone to water carryover. Blocked pads may have to be
replaced if the blockage cannot be cleaned out. Otherwise, the water flow/airflow may be temporarily reduced to
compensate. This will result in reduced capacity.
f) As pads age they can accumulate unmovable dirt and accumulations. This may reduce the water flow rate the pad
is able to handle without producing water carryover.
g) Whenever the unit’s water bleed rate has been adjusted the water flow to the pads should be rechecked.
Avoid Flooded Pads!
If the water flow rate to the filter pads is too high water draw-off or carryover will occur, often resulting in unit damage
and premature component failures. In some cases water droplets can be sucked into the blower/fan wheel scroll and
blown down the attached dropper or duct system.
When commissioning or servicing the unit look for tell-tale signs of flooded pads such as water washed bearings,
rust on the dropper/plenum, water stains on the sides of the blower housing, fan scroll, and on the dropper/plenum.
Over time water carryover will result in premature bearing failures, excessive corrosion, and damage to electrical
components in the unit.
Damage due to water carryover is not covered by warranty.
4.7 COMMISSIONING RESULTS
All commissioning results should be recorded with a copy to be stored in the control box for reference during
maintenance.