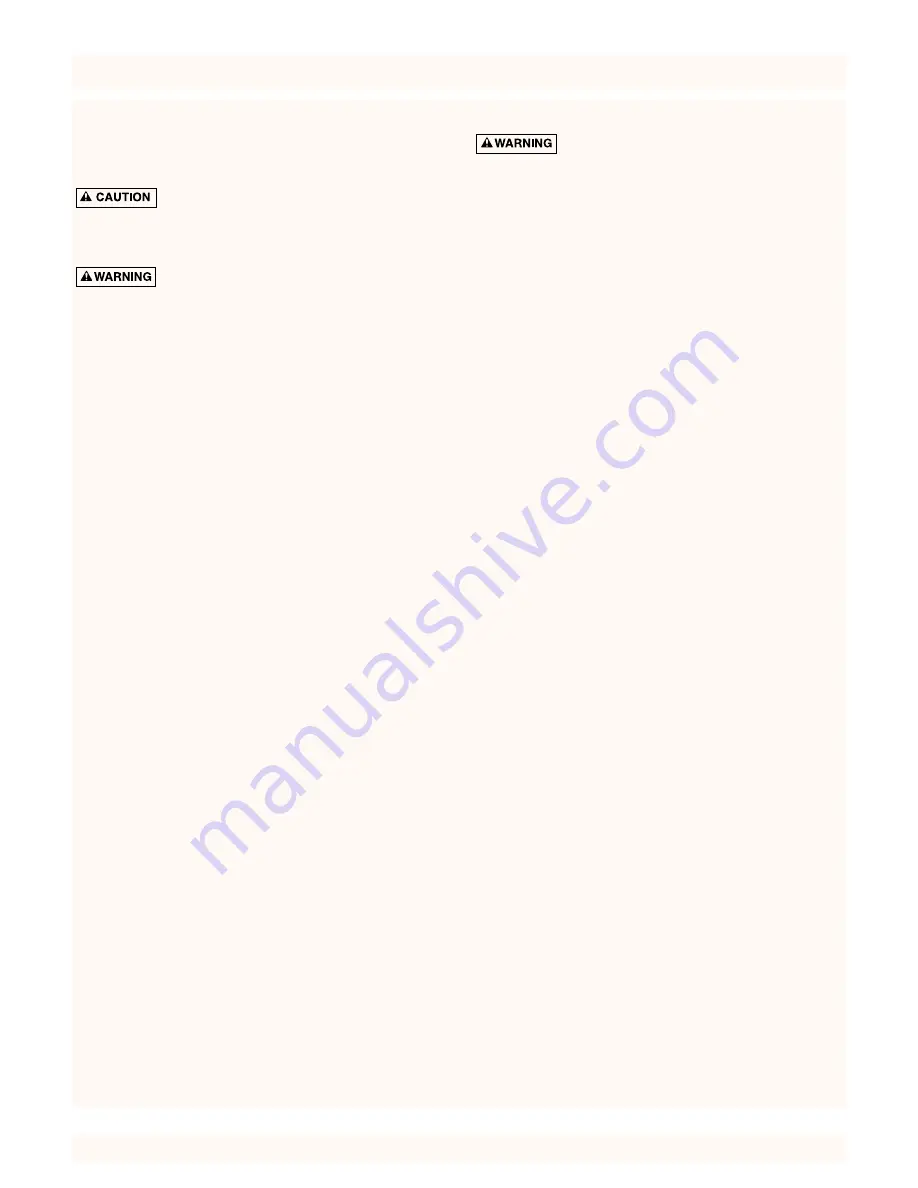
OPERATION
Priming the Pump
NOTE:
To properly prime the pump, install a pipe tee in the
discharge piping, similar to that shown in Figures 1 and 2 on
Page 3.
Never run pump dry.
Running pump with-
out water may cause pump to overheat, dam-
aging seal and possibly causing burns to persons handling
pump. Fill pump with water before starting.
Explosion Hazard.
Never run pump against
closed discharge. To do so can boil water in-
side pump, causing hazardous pressure in unit, risk of ex-
plosion and possibly scalding persons handling pump.
To prevent damage to internal parts, do not start
motor until pump has been filled with water
.
To prime pump:
1. Remove priming plug (Figure 1, Page 3).
2. Fill pump with water.
3. Replace priming plug, using Teflon tape on plug threads;
tighten plug.
4. Start the pump. Water should be pumped in 1-2 minutes.
If not, repeat steps 1, 2 and 3.
On shallow depths to water (ten feet or less), the pump
will more than likely prime the first time after following
the outlined procedure.
From ten to 20 foot depths, it is very likely you will have
to shut the pump off and reprime per the outlined pro-
cedure several times.
5. If, after priming pump several times, no water is pumped,
check the following:
A. Be sure suction pipe is in the water.
B. Be sure suction pipe has no leaks.
C. Be sure the pump is not trying to lift water too high.
(See “Piping in the Well,” Page 4).
6. As long as foot valve and check valve function correctly
and suction pipe does not develop leaks, pump should
not need repriming in normal service.
MAINTAINING YOUR PUMP
Lubrication
It is not necessary to lubricate the pump or its motor. The
motor bearings are lubricated for life. The mechanical shaft
seal in the pump is water lubricated and self-adjusting.
Draining for Winter
When the pump is to be disconnected from service or is in
danger of freezing, it must be drained. To drain it, turn off
power and relieve all pressure on the system. Remove pres-
sure switch tubing from the side of the pump housing.
Remove the priming plug to vent the pump. Drain the pres-
sure tank; drain all piping to a point below the freeze line.
To drain an air volume control (AVC), remove the tubing
from it and turn the AVC upside down. This will permit any
water in the AVC to drain into tank.
Disassembly and Assembly of Pump
Risk of electrical shock.
Be sure unit is
grounded and power disconnected before at-
tempting any work on pump or motor.
Your SEARS pump is designed for ease in servicing. Should
repair or replacement of the motor or seal be needed, the
pump and piping do not need to be disconnected or dis-
turbed.
1. Disassemble pump as follows:
A. Disconnect power.
B. Remove pressure switch tube from pump body and
allow pump to drain.
C. Remove four hexnuts and lockwashers (Key Nos. 24
and 23, Page 11) which hold the pump body to the
motor.
D. Remove motor, seal plate, impeller, rubber pad and
diffuser (Key Nos. 1, 3, 7, 8 and 9, Page 11) as a unit.
You may have to pry gently with two screwdrivers be-
tween the motor flange and the pump body to sepa-
rate pump and motor.
2. Reassembly of pump:
A. Install O-Ring gasket on seal plate (Key Nos. 5 and 3,
Page 11).
B. Pick up a
small
amount of petroleum jelly on one fin-
ger and spread evenly over seal plate and venturi O-
Ring gasket for lubrication during reassembly.
Be
careful
not to nick or tear O-Ring.
C. Replace motor onto pump body; be sure rubber pad
(Key No. 8, Page 11) stays in place on top of diffuser.
Remount base on lower studs. Tighten four hexnuts
and lockwashers snugly (35-45 inch-lbs. torque).
Do
not overtighten.
D. Replace pressure switch tubing and motor wiring.
E. Prime pump according to instructions above.
F. Check for leaks.
Removing Motor for Service
and Replacing Shaft Seal
If it is necessary to separate motor and seal plate, always re-
place the shaft seal. We suggest you purchase this item,
U109-6A, and have it on hand for future use.
NOTICE:
The seal consists of two parts, a rotating member
and a ceramic seat. The surfaces of the seal are easily dam-
aged. Read instructions carefully.
Remove motor as follows:
1. Disassemble pump per instructions above.
2. Remove diffuser and impeller as follows (Key Nos. 9 and
7, Page 11).
A. Remove screws holding diffuser.
B. Loosen two screws and remove motor canopy from
motor (Key No. 1, Page 11).
C. Place 7/16” open end wrench on motor shaft flat.
D. Turn impeller counterclockwise when facing it.
6