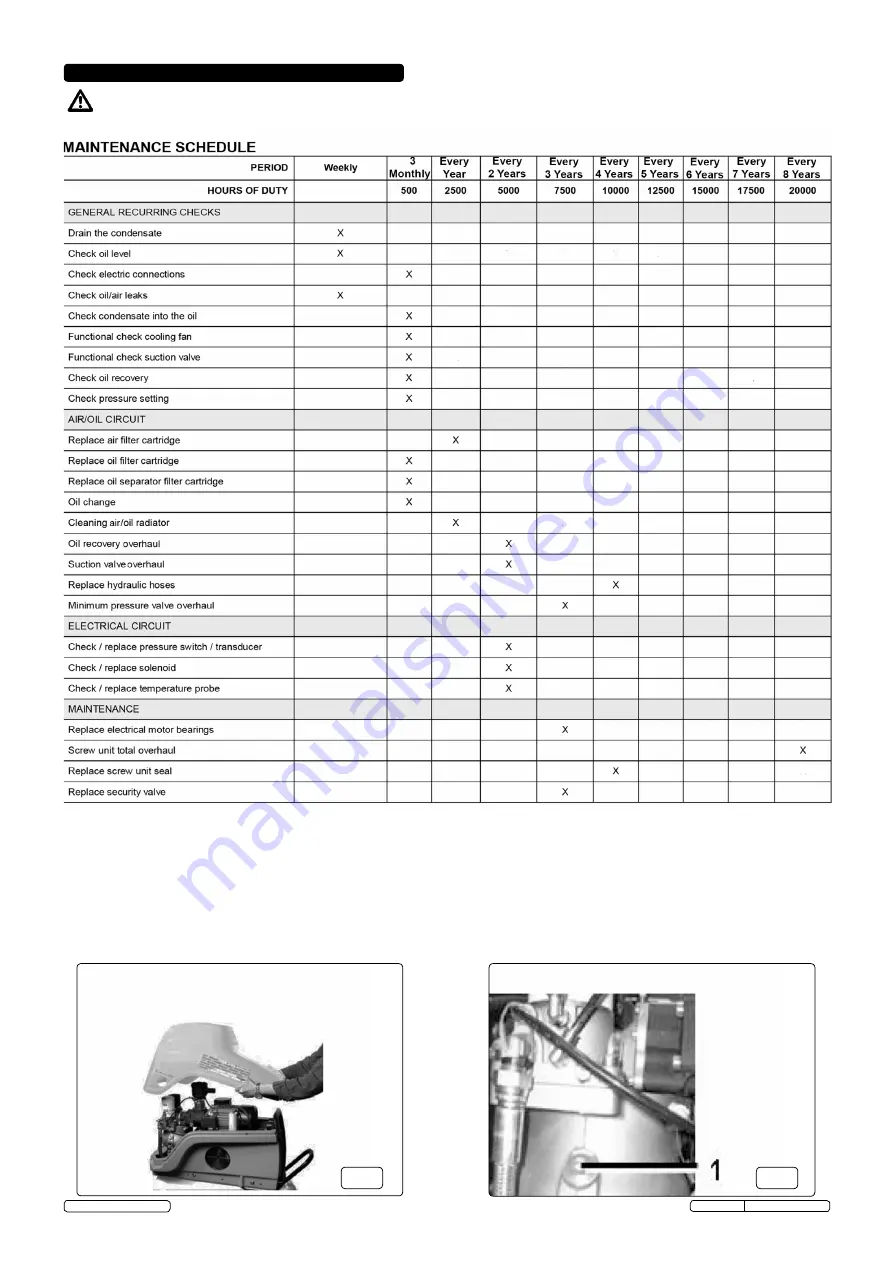
WARNING:
the safety instructions given in section 1 should be applied before any maintenance is attempted.
the machine
MUST
be isolated from the electric supply and drained of air before any of the operations shown below are undertaken.
Note
: If the compressor is used for more than 3000 hours/year the jobs indicated below are to be performed more often
Original Language Version
6. COMPRESSOR MAINTENANCE
the above described maintenance schedule has been planned bearing in mind all the installation parameters and recommendation
stated in these instructions.
You are advised to keep a record of all maintenance jobs performed on the compressor.
6.1.
DRAINING CONDENSATE.
Drain the condensate from the air tank at least once a week by opening the draining valve under the tank.
(fig.4)
6.2.
OIL CHANGE.
6.2.1.
change the oil following the initial 500 hours of use and then every 2500 hours and in any event once a year.
6.2.2.
In case of infrequent use (few hours of duty per day) you should change the oil every 6 months.
6.2.3.
recommended oil: D46 grade screw compressor oil.
remove the shroud
remove the plug (1) (with intenal hex head) situated above
the sight glass.
ssc11003 Issue: 1 - 03/05/13
© Jack sealey Limited
fig.5
fig.6
Summary of Contents for SSC11003
Page 9: ......