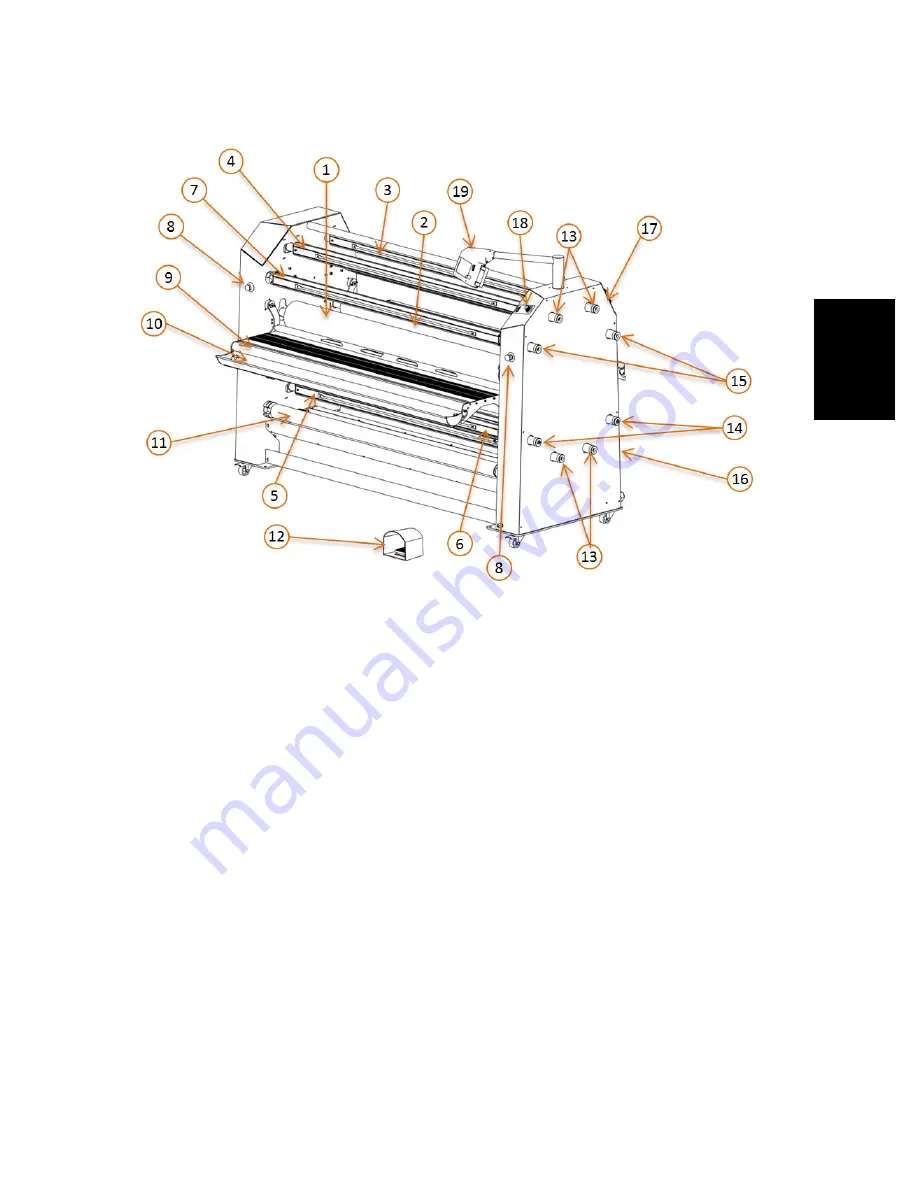
Description
21
E
n
g
lis
h
4.2 Parts identification
Figure 5: Parts Idenification.
1. Main roll (top front)
2. Pull roll (top rear)
3. Swing out supply shaft (top rear)
4. Swing out supply shaft (top front)
5. Swing out supply shaft (bottom Front)
6. Take up autogrip shaft (bottom front)
7. Take up autogrip shaft (top front)
8. Emergancy Stop
9. Infeed table
10. Roll trough
11. Roll feed idler
12. Foot switch (front)
13. Supply shaft brakes
14. Combi shaft brake / clutches
15. Take up clutches
16. Power circuit breaker
17. Rear control panel
18. Front control panel
19. Easy Operator Interface
TM
(EOI)
Summary of Contents for 65ProMD
Page 3: ...Introduction 3 English...
Page 8: ......
Page 31: ...Machine Operation 31 English...
Page 33: ...Machine Operation 33 English...
Page 36: ...36 7003338 User Manual 65 Pro MD Setting the Nip Height...
Page 55: ...Machine Operation 55 English Figure 1 Blank Webbing Diagram...