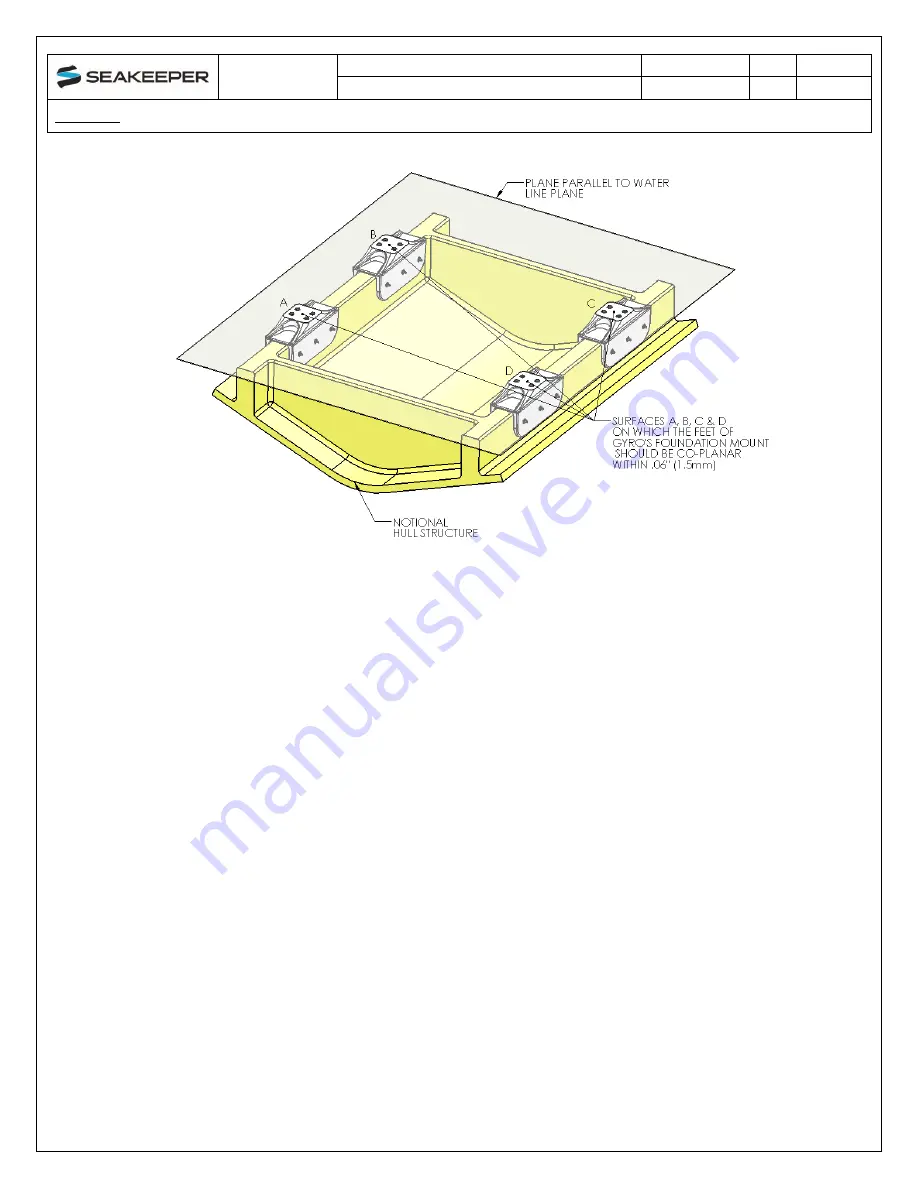
INSTALLATION
MANUAL
Product:
Document #:
Rev:
Page:
SEAKEEPER 9 / 7HD
90222
6
16 of 20
Section 1: MECHANICAL INSTALLATION
4) Thoroughly clean with alcohol or acetone all areas of girders to be bonded to remove
any contaminates. Use new paper towels for cleaning, not shop rags.
5) Remove any paint or gel-coat from bond surfaces so that adhesive will bond directly to
laminate fibers and resin as shown in Figure 8.
6)
Thoroughly sand girder bond surfaces with 80 grit sandpaper. (IMPORTANT
–
BOND STRENGTH MAY BE REDUCED IF THIS STEP IS SKIPPED.)
7) Wipe surfaces clean from dust with alcohol or acetone using new paper towels, not shop
rags.
8) Re-position installation fixture on girders and double-check that the adhesive gap is
within the adhesive manufacturer’s maximum recommended thickness. Seakeeper
recommends a maximum gap of 3 mm if using Plexus MA590.
Note if bonding saddles to a metal structure, contact the adhesive manufacturer for hull
preparation instructions.
FIGURE 10
– COPLANAR PROPERTIES OF FOUNDATION