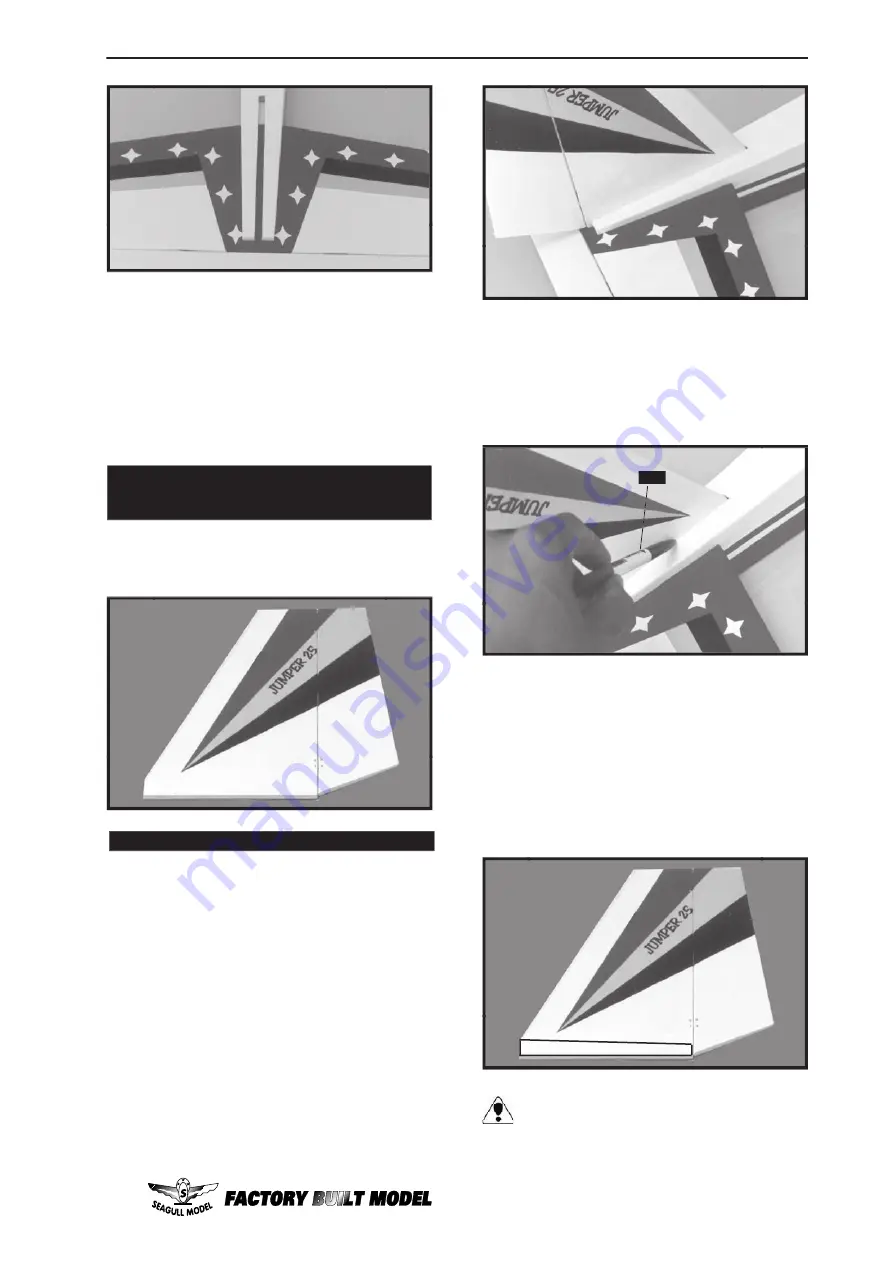
Jumper 25
Instruction Man u al
13
10) After the epoxy has fully cured,
re move the masking tape or T-pins used to
hold the sta bi liz er in place. Carefully inspect
the glue joints. Use more ep oxy to fi ll in
any gaps that may exist that were not fi lled
previously and clean up the excess using a
pa per towel and rubbing alcohol.
VERTICAL STABILIZER
INSTALLATION
PARTS REQUIRED
{1} Vertical Stabilizer with Rudder
ALIGNING THE VERTICAL STABILIZER
1) Using a modeling knife, remove the
cov er ing from over the precut hinge slot cut
into the lower rear portion of the fuselage. This
slot ac cepts the low er rud der hinge.
2) Slide the vertical stabilizer into the slot
in the top of the fu se lage. The rear edge of
the sta bi liz er should be fl ush with the rear
edge of the fu se lage and the lower rudder
hinge should engage the precut hinge slot in
the lower fu se lage. The bottom edge of the
stabilizer should also be fi rmly pushed against
the top of the hor i zon tal stabilizer.
3) While holding the vertical stabilizer
fi rm ly in place, use a pen and draw a line on
each side of the ver ti cal sta bi liz er where it
meets the top of the fuselage.
4) Remove the stabilizer. Using a
mod el ing knife, re move the cov er ing from
below the lines you drew. Also re move the
cov er ing from the bot tom edge of the stabilizer
and the bottom and top edges of the fi ll er
block. Leave the cov er ing in place on the
sides of the fi ller block.
When cutting through the covering to
re move it, cut with only enough pres sure
to only cut through the covering it self.
Cut ting into the balsa struc ture may weak en
it.