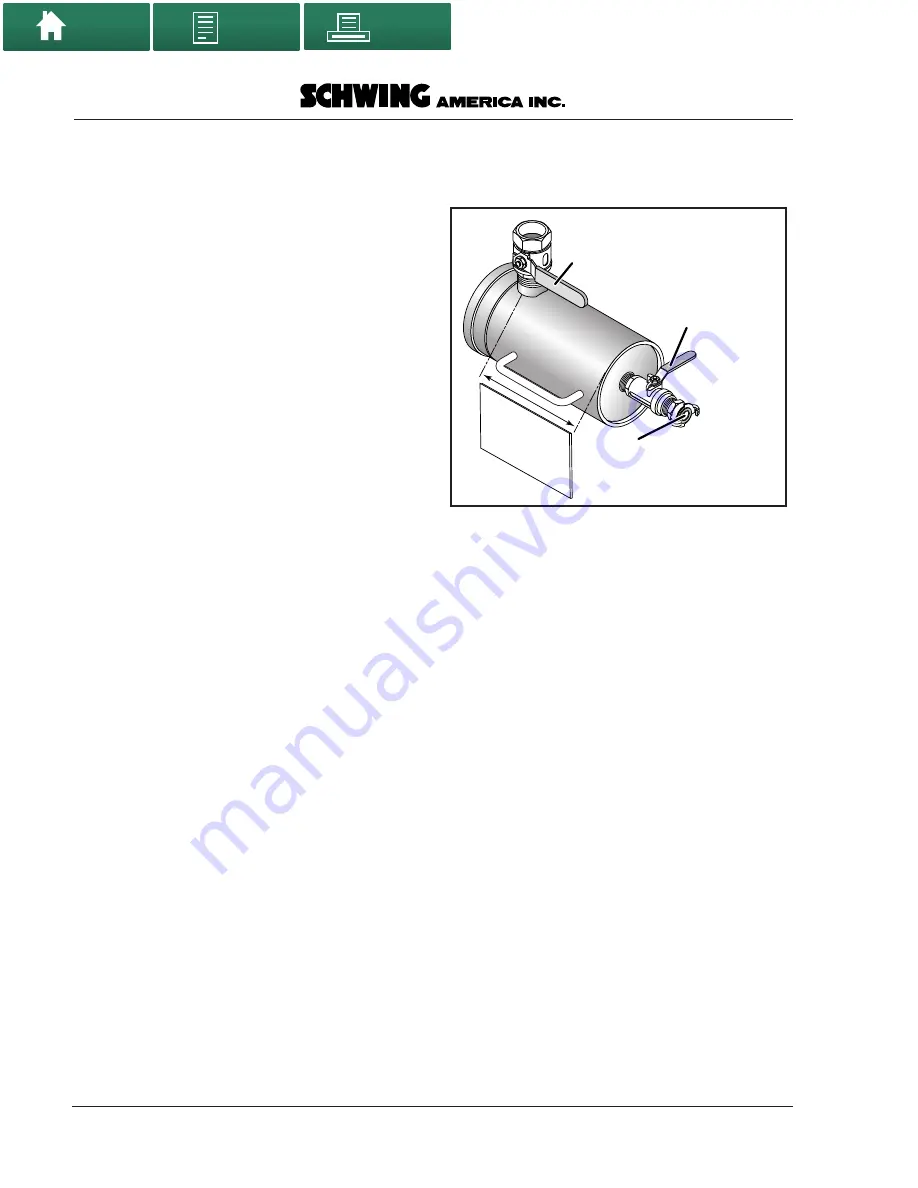
Operation
32
7/27/12
Operation Manual - SP 305
3.
Pump out the delivery system with source
water pressure.
Reverse the pump to remove
any pressure in the delivery system. Stop the
pump and engine. Disconnect the delivery
system from the concrete valve outlet. Install a
sponge ball in the delivery system. Place a water
blowout cap on the delivery system. Hook a hose
between the water source and the water blowout
cap and pump water into the delivery system
until the sponge ball appears at the other end.
This method doesn’t always work, because the
source water pressure may not be high enough to
move the concrete through the delivery system.
4.
Blow the delivery system with compressed air.
We do not recommend this method, because
compressed air can be very dangerous if not
handled correctly. Use it only as a last resort.
Complete safety rules for using compressed air
are discussed in the
Safety Manual
.
Never use
compressed air to clean out rubber hose
because the hose will jump around and move
through the air by the force of the pressure in the
hose. You cannot hold or stand on the hose to
steady it because the forces will exceed your
weight, even if you are a huge person. You
cannot have an entire crew of people holding the
hose because the force will exceed all of their
weights combined. If you have only steel pipe to
clean, it is possible to use air, but it can still be
dangerous.
Always control the discharge end
of the pipeline. Either a catch basket must be
used, or the discharge must be made safe in
some other manner, such as routing it into a
ready mix truck. The blowout head must have
two pressure bleed possibilities: an inlet valve
and a bleed-off valve. There must be enough
space between the two valves that a cleanout
ball cannot block both ports at the same time
(
Figure 22)
.
Remember, if you use this method,
you must disconnect all rubber hose from the
delivery system and clean them manually
anyway, so it might be just as quick to clean the
entire delivery system manually.
•
Clean the clamps and gaskets used on the delivery
system. Do not leave any concrete, stones, or sand
on them, or the clamps won’t properly close the
next time you use them.
Clean the pump
Clean the hopper and concrete valve. If not already
done, stop the pump and disconnect the delivery
system. (Note! Once the delivery system is
disconnected, there is no more danger of compressing
any air that gets sucked into the material cylinders).
Proceed as follows:
•
Restart the unit and pump out the rest of the
concrete from the hopper and concrete valve. Put
the pump in reverse, and give it one stroke. Stop
the pump as soon as the concrete valve switches
(this step assures that the material cylinder is
empty and the piston cup is towards the back of the
unit).
NOTE!
If you used method # 1 to clean the pipeline,
there will only be some clean, washed stones
and sand left in the material cylinders and
concrete valve; in that case, you can skip
this step.
Water/air inlet
Air discharge
regulator valve
Air inlet
regulator valve
caponly
.eps
ports spaced so a
cleanout ball cannot
cover both ports
simultaneously
Figure 22
Blow-out head
Home
TOC
Home
TOC
Summary of Contents for SP 305
Page 10: ...Introduction Operation Manual SP 305 10 8 4 11 NOTES Home TOC Home TOC Print Print...
Page 14: ...Specifications Operation Manual SP 305 14 8 4 11 NOTES Home TOC Home TOC Print Print...
Page 20: ...Safety Operation Manual SP 305 20 8 4 11 NOTES Home TOC Home TOC Print Print...
Page 38: ...Operation 38 8 4 11 Operation Manual SP 305 Home TOC Home TOC Print Print...
Page 100: ...Appendix Operation Manual SP 305 100 revDate NOTES Home TOC Home TOC Print Print...
Page 101: ...SP 305 OPERATION MANUAL INDEX Home TOC Home TOC Print Print...