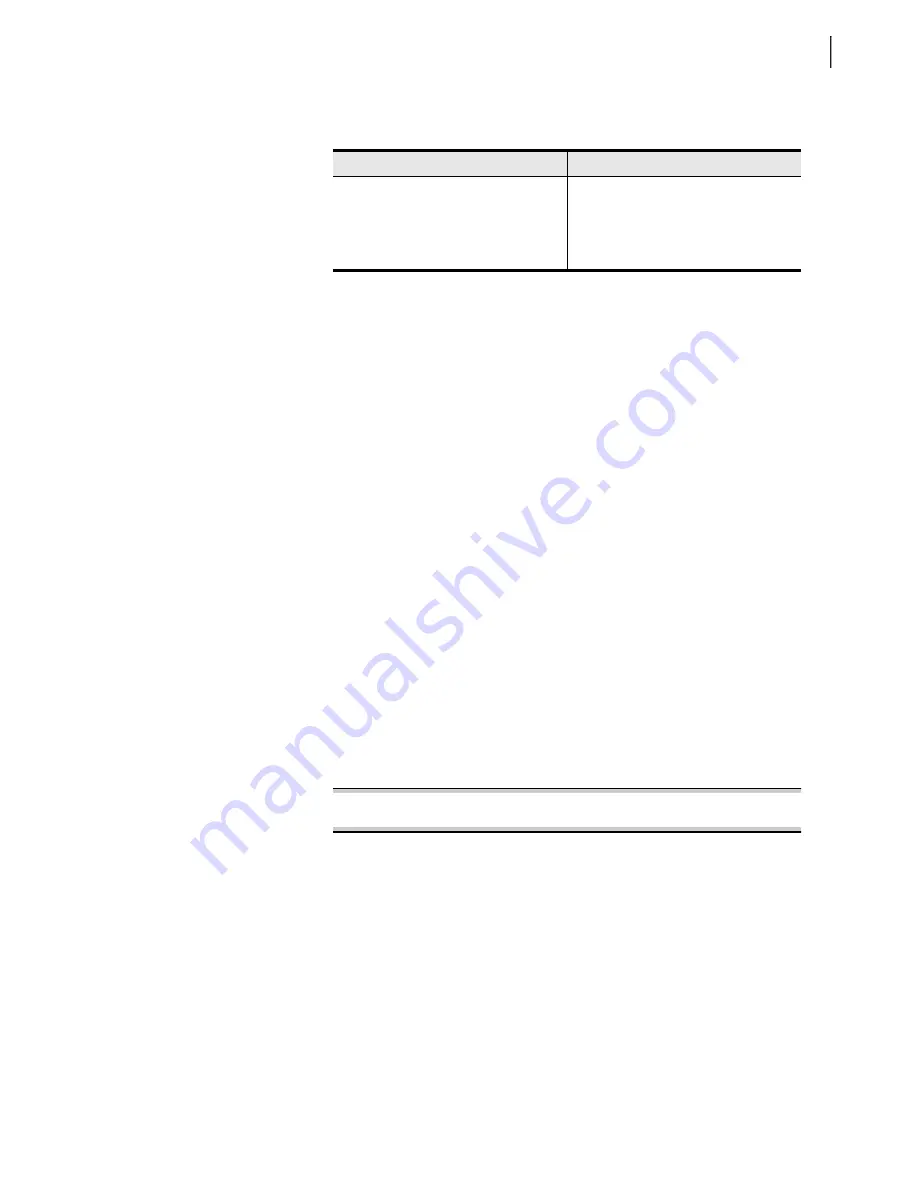
7.15
Date Code 20020903
SEL-587Z Instruction Manual
ASCII Command Reference
Command Definitions
The relay prompts for each setting in the order specified in the
The relay performs limit checks as each value is entered. The limits for each
setting are specified in the
Settings Sheets
. If a setting is out of limits, the relay
responds “Out of range” and prompts for the value again.
After you enter a setting successfully, the relay will prompt you for the next
setting in the class. After you have entered all settings in the class, the relay
performs secondary settings checks to verify that the settings are in order. If a
settings check fails, the relay displays a warning message and prompts for the
settings value that caused the warning condition. If more than one setting
value fails, the relay prompts for the first settings value that failed.
After you have entered the last setting in the class and settings have been
modified, the relay displays a listing of the settings and then responds “Save
changes (Y/N) ?” If you type “n” or “N,” the relay does not save the changes
and responds “Settings aborted.” If you type “y” or “Y,” the relay saves the
changes and responds “Settings saved.” The relay response is the same when
no settings are changed.
Use the
TER
option to inhibit the relay from sending the setting class or
instance readback when you end a setting session. SEL recommends that you
use the
TERSE
option sparingly; you should review the readback information
to confirm that you have entered the settings that you intended. You can use
the
TERSE
option in any command at any position after typing
SET
. When
you end the setting edit session, the relay responds, “Save settings (Y,N)?” If
you answer
Y<Enter>
, the relay pulses the alarm contact, saves the new
settings, then responds “Settings Saved.” If you answer
N<Enter>
to the save
settings prompt, the relay responds “Settings aborted.”
For example, to set the differential element 87A2 pick-up value, enter the
following:
Set 87A2P <Enter>
=>>
SHO (Showset)
Access Levels 1, 2
Use the
SHO
command to view relay settings.
The
SHO
command format is the following:
SHO
x y
where:
x
is the settings class to display
y
is the name of the first setting to display
Keyed Entry After the Prompt
SEL-587Z Action
<CR>
Retains previous setting value
“
^
” or “
<
“
Backs up to previous setting value
“
>
”
Advances to next setting value
“
END
” or “
end
”
Skips to the end of the class
Summary of Contents for SEL-587Z
Page 10: ...This page intentionally left blank ...
Page 12: ...This page intentionally left blank ...
Page 66: ...This page intentionally left blank ...
Page 106: ...This page intentionally left blank ...
Page 126: ...This page intentionally left blank ...
Page 162: ...This page intentionally left blank ...
Page 228: ...This page intentionally left blank ...