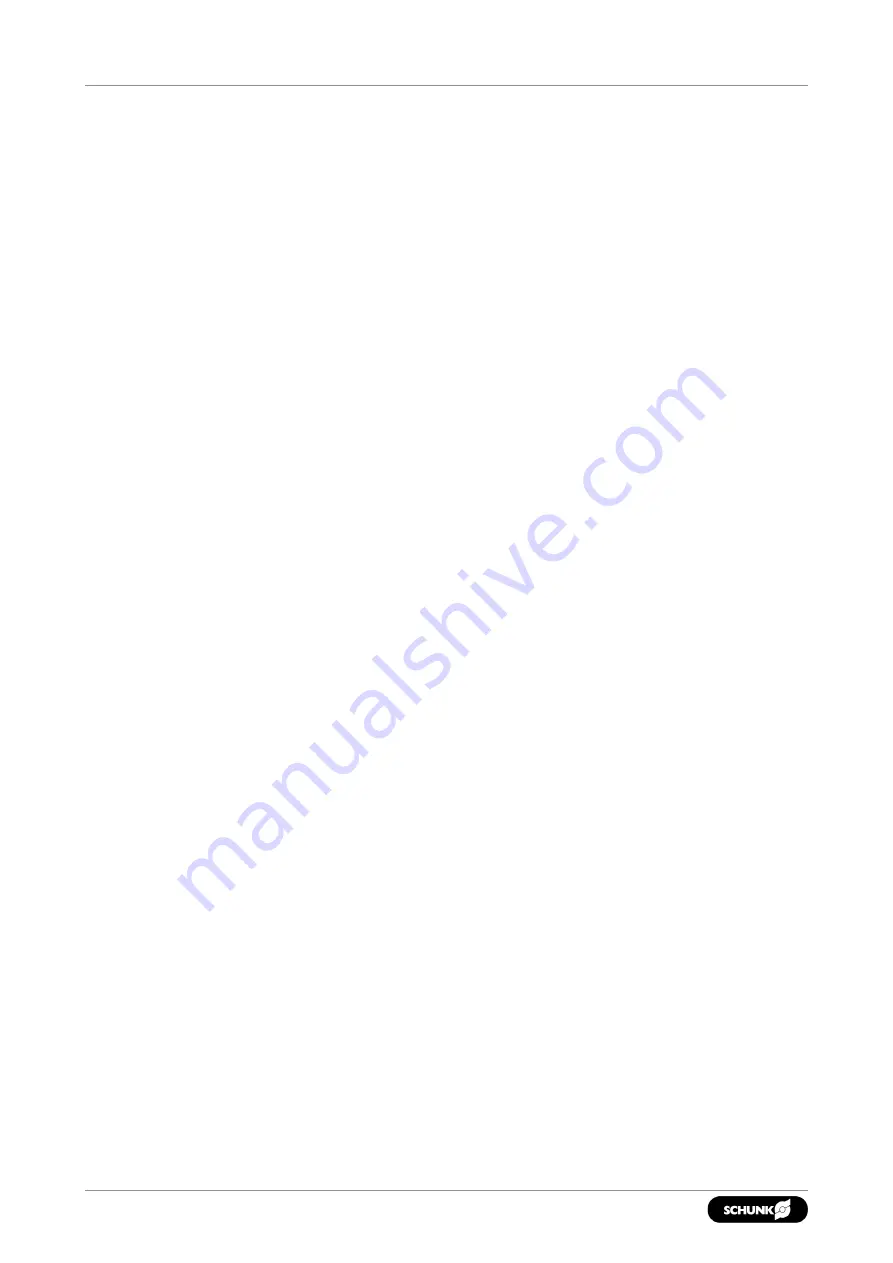
Assembly and connection
20
04.00 | KSP3, KSP3-LH, KSP3-F | TANDEM Clamping Block | en | 1463318
NOTE:
If the clamping force block and base plate are ordered separately,
the screws, O-rings and clamping sleeves for assembling the parts
are included in the accessory kit that comes with the clamping
force block.
• Do not open the connections on the front of the clamping force
block (
I, II
), or seal them with suitable dummy plugs (M5 or
G1/8").
• Insert the clamping sleeves from the accessory pack into the
centering holes on the base plate.
• Remove the seal plugs from the base plate (internal air feed-
through
III, IV
) and insert the O-rings from the accessory pack
into the recesses for the air feed-throughs.
• Mount the clamping force block onto the base plate.
NOTE:
The TANDEM base plates do not have a connection possibility for
the inductive proximity switches on the TANDEM clamping force
blocks.
The function for monitoring the jaw position can only be
connected externally. When joining, make sure the air feed-
throughs for the clamping system and the base plate are precisely
aligned.
• Screw the two parts together using the four screws (item 84)
from the accessory kit. In doing so, observe tightening
torques
• Remove the locking screws from the pneumatic connections on
the base plate.
• Connect the diaphragm pressure switch and set the switch to
the required minimum pressure.