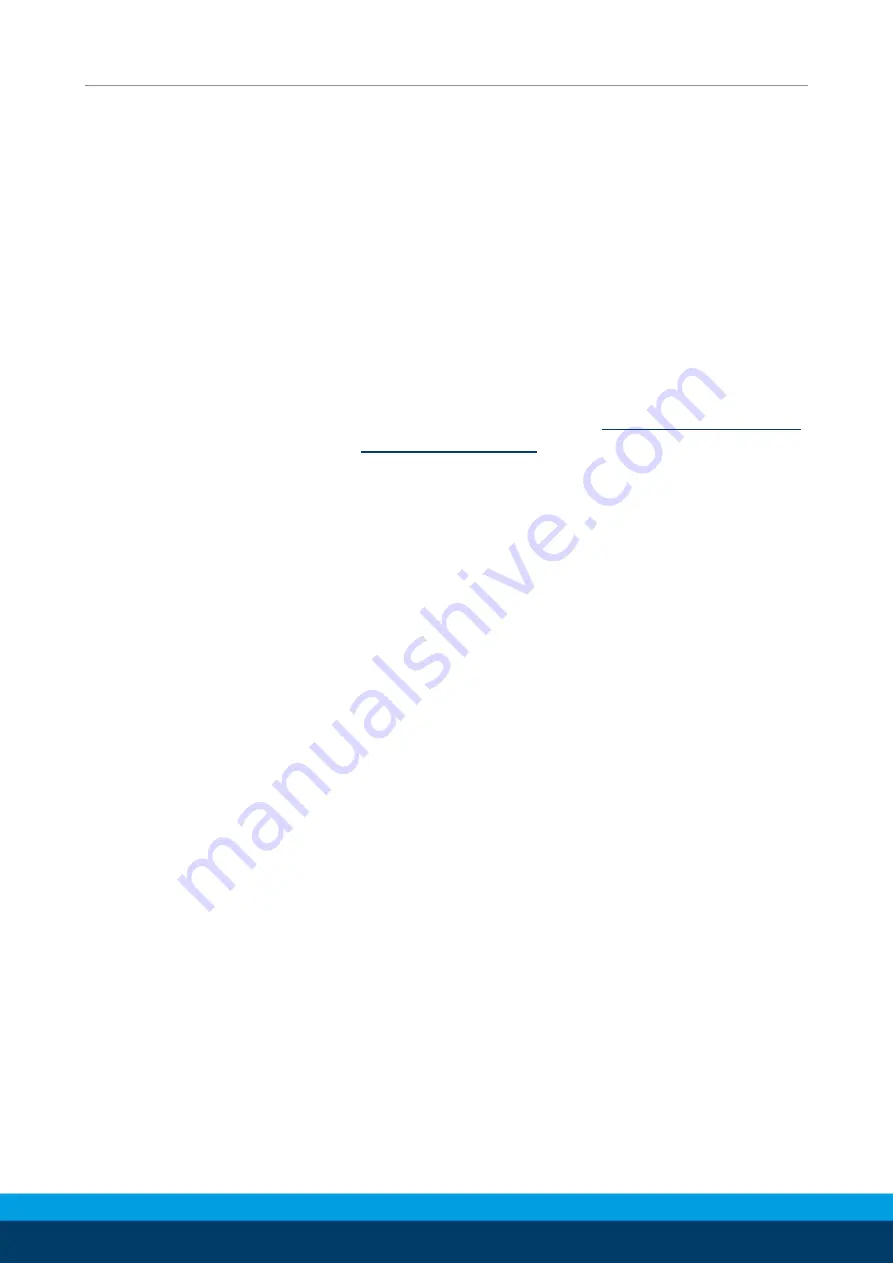
Maintenance and care
42
04.00 | GSM-R | Assembly and Operating Manual | en | 389106
Ø
Turn the screws (140) from the bushing of the gripping module
(31-34) and pull DKM GSM stop 1 (81) and the set of fitting disks
(111/112) off the bushing (44 or 46).
Ø
Pull the gripping module (31-34) from the housing DKM GSM.
Ø
For elastomer variants, proceed as follows:
Remove the stops (83) after loosening the nuts (124).
Also remove the needle rollers (122).
Ø
For shock absorber variants, continue as follows:
Remove the shock absorber (120) after loosening the nuts
(121).
Also remove the sleeves (122).
Assembly
For assembly, observe the permissible tightening torques as well
as the greases and adhesives to be used;
37] and
Ø
Grease the housing DKM GSM(11) and the bushing (44 or 46) on
the running surfaces and bearings.
Ø
Grease the bearing ring (82).
Ø
Insert the bearing ring with the outer chamfer downwards into
the housing DKM GSM.
Ø
Grease the O-rings (103) and mount them into the recesses on
the bushing (44 or 46).
Ø
Insert the gripping module into the housing DKM GSM.
Ø
Match up the axial bearing seat of the bushing with the fitting
disks (111 or 112).
Ø
Place DKM stop 1 (81) onto the bushing and fasten it to the
bushing using the screws (140).
Ø
Grease the ball guide DKM (85).
Ø
Turn the bushing so that DKM stop 1 (81) is pointing 180° away
from the bore holes for dampening.
Ø
Grease the needle rollers (122) and put them into the
appropriate fits.
Ø
For elastomer variants, proceed as follows:
Grease the needle rollers (122) and put them into the
appropriate fits.
Place one ball (142) in the housing in front of each needle roller
(122) and screw DKM stop 2 (83) into the housing.
Ø
For shock absorber variants, continue as follows:
Grease the sleeves (122) and put them on the shock absorbers
(120). Insert the sleeve into the fit provided in the housing DKM
GSM (11) and screw the shock absorber into the housing.
Place one ball (142) in the housing in front of each sleeve (122).
Ø
Mount the counter nut (124) onto the stops/shock absorbers.