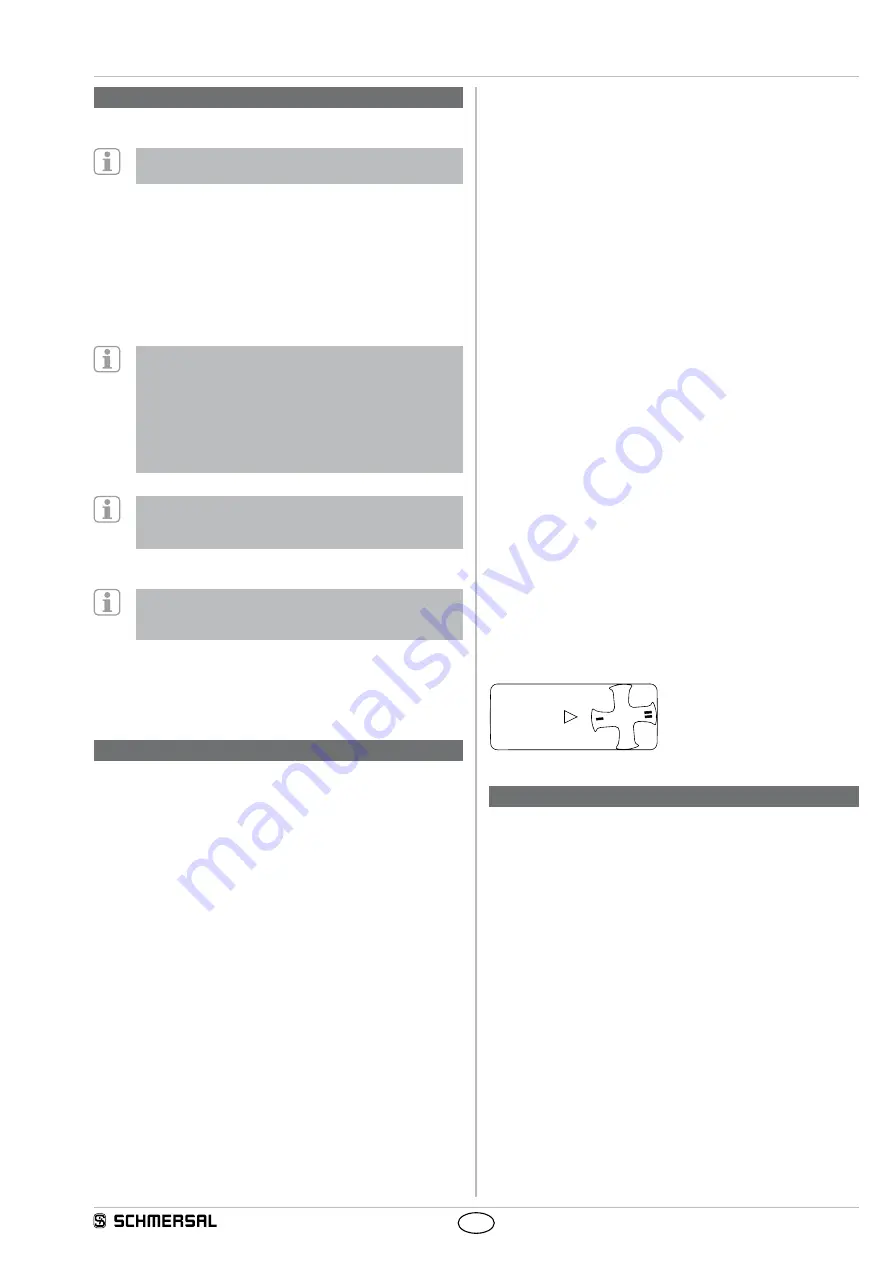
7
AZM300
Operating instructions
Solenoid interlock
EN
4. Electrical connection
4.1 General information for electrical connection
The electrical connection may only be carried out by
authorised personnel in a de-energised condition.
The voltage inputs A1, X1, X2 and IN must have a protection against
permanent overvoltage. supply units according to IEC 60204-1 is
recommended.
The safety outputs can be integrated in the safety circuit of the control
system.
Requirements for the connected safety-monitoring module:
• Dual-channel safety input, suitable for p-type semi-conductor outputs
Configuration of the safety-monitoring module
If the safety sensor is connected to electronic safety-monito-
ring modules, we recommend that you set a discrepancy time
of min. 100 ms. The safety inputs of the safety-monitoring
module must be able to blank a test impulse of approx. 1 ms.
The safety-monitoring module does not need to have a cross-
wire short monitoring function, if necessary, the cross-wire
short monitoring function must be disabled.
Information for the selection of suitable safety-monitoring
modules can be found in the Schmersal catalogues or in the
online catalogue on the Internet: products.schmersal.com.
Cable design in case of serial diagnostics
When wiring SD devices, please observe the voltage drop on
the cables and the current carrying capacity of the individual
components.
The wiring capacity of the connecting cable of the solenoid interlock
must not exceed 50 nF. Depending on the strand structure, normal
unshielded 30 m long control cables LIYY 0.25 mm² to 1.5 mm² have a
wiring capacitance of approx. 3 … 7 nF.
5. Operating principle, actuator coding and latching force adjustment
5.1 Magnet control
In the power to unlock version of the AZM300, the solenoid interlock
is unlocked when the IN signal (= 24V) is set. In the power to lock
version of the AZM300, the solenoid interlock is locked when the IN
signal (= 24 V) is set.
5.2 Mode of operation of the safety outputs
In the standard AZM 300Z variant, the unlocking of the solenoid
interlock causes the safety outputs to be disabled. The unlocked
safety guard can be relocked as long as the actuator is inserted in
the AZM 300Z solenoid interlock; in that case, the safety outputs are
re-enabled. The safety guard must not be opened.
In the AZM300B version, only the opening of the safety guard causes
the safety outputs to be disabled.
If the safety outputs are already enabled, any error that does not
immediately affect the functionality of the solenoid interlock (e.g.
too high an ambient temperature, interference potential at the
safety outputs, cross-wire short) will lead to a warning message,
the disabling of the diagnostic output and the delayed shutdown
of the safety outputs.
Safety outputs are disabled if the error warning is active for 30 minutes.
The signal combination, diagnostic output disabled and safety channels
still enabled, can be used to stop the production process in a controlled
manner. After the rectification of the error, the error message is reset
by opening the corresponding safety guard. For devices with serial
diagnostic, a bit can be set/deleted in the call telegram to reset the fault.
5.3 Actuator coding
Solenoid interlocks with standard coding are ready to use upon delivery.
Individually coded solenoid interlocks and actuators will require the
following "teach-in" procedure:
1. Switch the solenoid interlock's voltage supply off and back on.
2. Introduce the actuator in the detection range. The teach-in procedure
is signalled at the solenoid interlock, green LED off, red LED on,
yellow LED flashes (1 Hz).
3. After 10 seconds, brief yellow cyclic flashes (3 Hz) request the
switch-off of the operating voltage of the solenoid interlock. (If the
voltage is not switched off within 5 minutes, the solenoid interlock
cancels the "teach-in" procedure and signals a false actuator by 5 red
flashes).
4. After the operating voltage is switched back on, the actuator must
be detected once more in order to activate the taught actuator code.
In this way, the activated code is definitively saved!
For ordering suffix -I1, the thus executed allocation of safety switchgear
and actuator is irreversible.
For ordering suffix -I2, the "teach-in" procedure for a new actuator can
be repeated an unlimited number of times. When a new actuator is
taught, the code, which was applicable until that moment, becomes
invalid. Subsequent to that, an enabling inhibit will be active for ten
minutes, thus providing for an increased protection against tampering.
The green LED will flash until the expiration of the time of the enabling
inhibit and the detection of the new actuator. In case of power failure
during the lapse of time, the 10-minutes tampering protection time will
restart.
5.4 Adjustment of the latching force
In order to enable trouble-free functionality of the device, the rotary
handle must be in position I or II when the safety guard is open.
In the intermediate positions, locking is impossible.
The latching force is changed by turning the rotary handle by 180°.
In position I,the latching force is approx. 25 N.
In position II, the latching force is approx. 50 N.
6. Diagnostic function
6.1 Diagnostic-LEDs
The solenoid interlock signals the operating condition, as well as errors
through 3-colour LEDs.
green
(Power) supply voltage on
yellow
(Status) operating condition
red
(Fault)
Error (see table 2: Error messages /
flash codes red diagnostic LED)
6.2 Solenoid interlock with conventional diagnostic output
The short-circuit proof diagnostic output OUT can be used for central
visualisation or control tasks, e.g. in a PLC.
The diagnostic output is not a safety-related output.