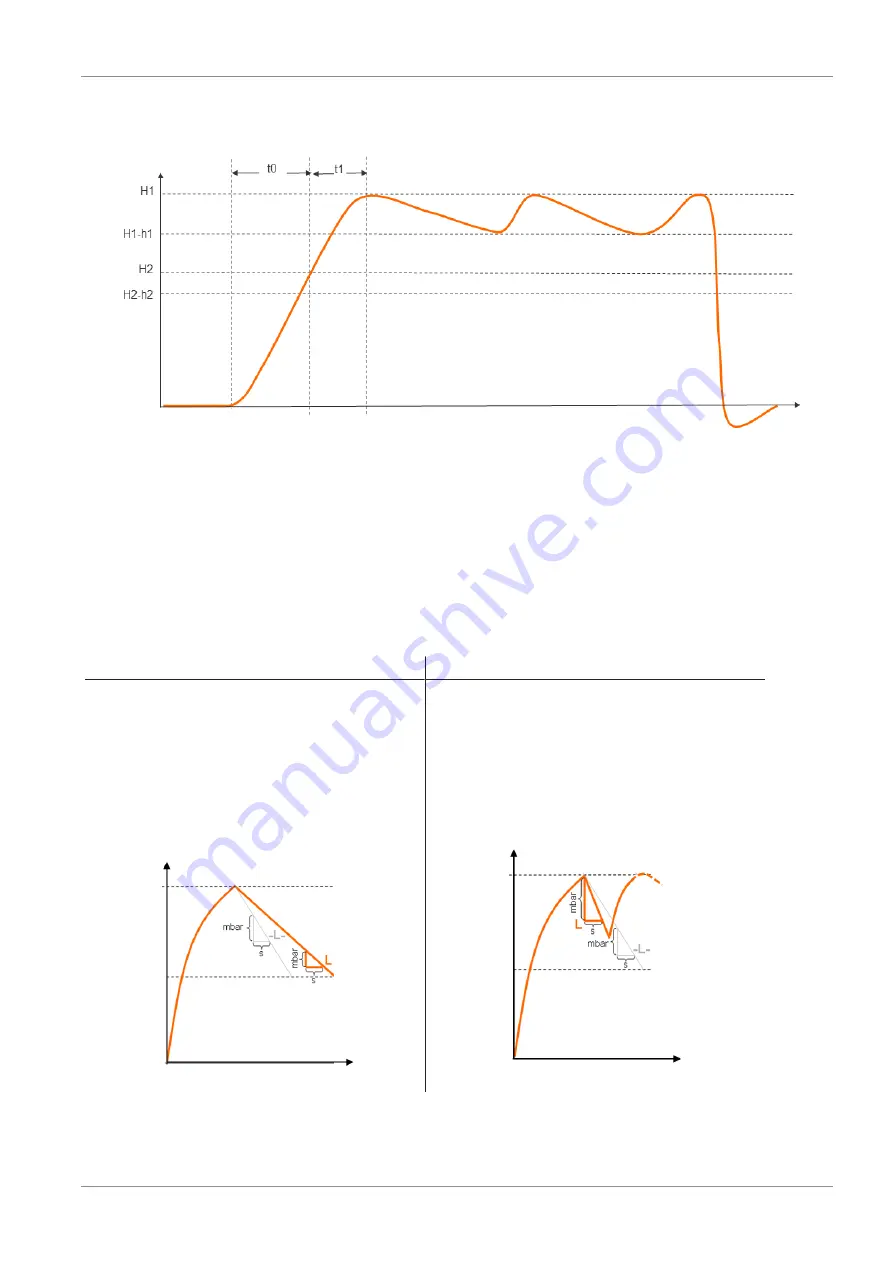
General Description of Functions
EN-US · 30.30.01.01484 · 00 · 01/21
35 / 72
Evacuation times t0 and t1
Vacuum
[mbar]
Suction ON
Time [s]
If the measured evacuation time t1 (from H2 to H1) exceeds the specified value [t-1], the “Evacuation time
longer than t-1” condition monitoring warning is triggered and the system status light switches to yellow.
The specified value for the max. permitted evacuation time can be set under the [
t-1
] menu item in the
configuration menu or via IO-Link. Setting the value to “0” deactivates monitoring. The maximum permit-
ted evacuation time setting is 9.99 seconds.
Leakage monitoring:
In control mode ([
ctr
] = [
on5
]), the loss of vacuum within a certain period is monitored (mbar/s). There
are two possible statuses.
Leakage L < permitted value -L-
Leakage L > permitted value -L-
If the leakage is lower than the set value, the
vacuum continues to fall until it reaches the
vacuum limit value H1-h1, and the ejector be-
gins with suction again (normal control
mode).
The condition monitoring warning is not acti-
vated and there is no effect on the system
status light.
If the leakage is higher than the value, the
ejector readjusts immediately.
If the permitted leakage is exceeded twice,
the ejector switches to continuous suction.
The condition monitoring warning is acti-
vated and the system status light switches to
yellow.
Vacuum
Time
H1
H-h1
Vacuum
Time
H1
H1-h1