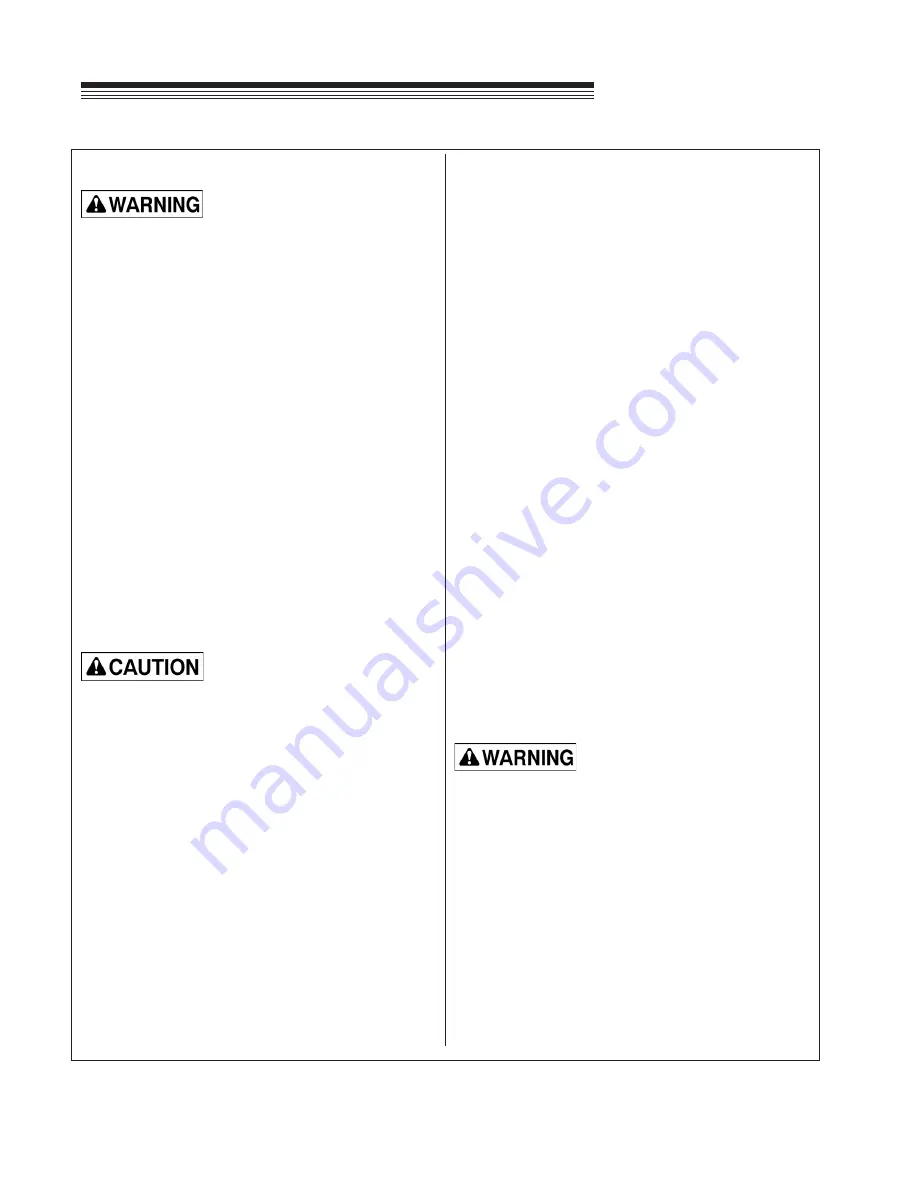
16
MATAWAY
STORAGE
STORAGE INSTRUCTIONS
To prevent possible explosion or ignition of
vaporized fuel, do not store equipment with
fuel in tank or carburetor in enclosure with
open flame (for example, a furnace or water
heater pilot light).
Do not smoke, avoid sparks and open flames
when draining or filling the fuel tank.
Before the equipment is put in to storage for
any period exceeding 30 days, the following
steps should be taken.
1. Drain all fuel from the fuel tank and fuel lines.
2. Start the engine and run until all the fuel is used
from the carburetor float bowl.
3. While engine is warm, drain the crankcase
oil and replace it with the proper weight oil
corresponding to the season the unit will next be
used. Refer to the engine manual for proper oil
recommendations.
Do not attempt to service or make repairs
near the engine area while the engine is still
hot.
4. Remove the spark plug and squirt a small
amount of clean motor oil into the cylinder. Turn
the engine over a few times to distribute the oil
and reinstall the sparkplug.
5. Lubricate all lubrication fittings.
6. Apply a light coat of oil to the blades and reel
shaft to prevent rust.
7. Lubricate drive chain with Lubricant #13563 or
equivalent.
NOTE
: Do not store unit with blades in the down
position. Be sure all belts are free from tension (the
clutch control lever in the disengaged position).
To put the equipment into service after an
extended period of storage:
1. Move unit to a level, well ventilated area.
2. Check unit for loose hardware and broken parts.
Tighten and replace as necessary.
3. Check for cracked or split fuel lines.
4. Make sure the air cleaner filter is clean.
5. Check that the air cleaner components and all
shrouds and belt covers are in place.
6. Check spark plug and plug wire.
7. Note if any blades need replacing.
8. Determine if the transmission and engine oil
need filling. Refill engine oil according to the
manufacturers recommendations, and refer
to the Preventive Maintenance section of this
manual for correct oil weight and amount for the
transmission.
9. Fill the tank with appropriate fuel as
recommended by the engine manual.
Do not smoke, avoid sparks and open flames
when draining or filling the fuel tank.
10. Make sure controls are in the disengaged or
neutral position.
11. Start engine and let run (at slow speed) until
approximate operating temperature has been
reached.
12. While engine is running (and has reached
operating temperature) visually inspect fuel lines
and carburetor for leaks. If a leak is found, make
sure the engine has cooled sufficiently before
attempting any repairs.
Summary of Contents for RYAN MATAWAY 744283C
Page 19: ...17 MATAWAY PARTS SECTION PARTS SECTION ...
Page 30: ...28 MATAWAY FIGURE 6 GUARDS ...
Page 32: ...30 MATAWAY FIGURE 7 REEL 1 32 BLADES 1 2 SPACING 1 2 2 3 3 4 5 6 7 8 9 10 12 13 14 15 16 ...
Page 34: ...32 MATAWAY FIGURE 8 REEL 1 32 BLADES 1 SPACING 1 2 2 3 4 5 6 7 8 9 10 11 13 14 15 16 17 ...
Page 36: ...34 MATAWAY FIGURE 9 REEL 1 16 BLADES 1 SPACING 1 2 2 3 3 4 5 6 7 8 9 10 12 13 14 15 16 ...
Page 38: ...36 MATAWAY FIGURE 10 REEL 1 16 BLADES 1 2 SPACING 1 2 2 3 4 5 6 7 8 9 10 11 13 14 15 16 17 17 ...