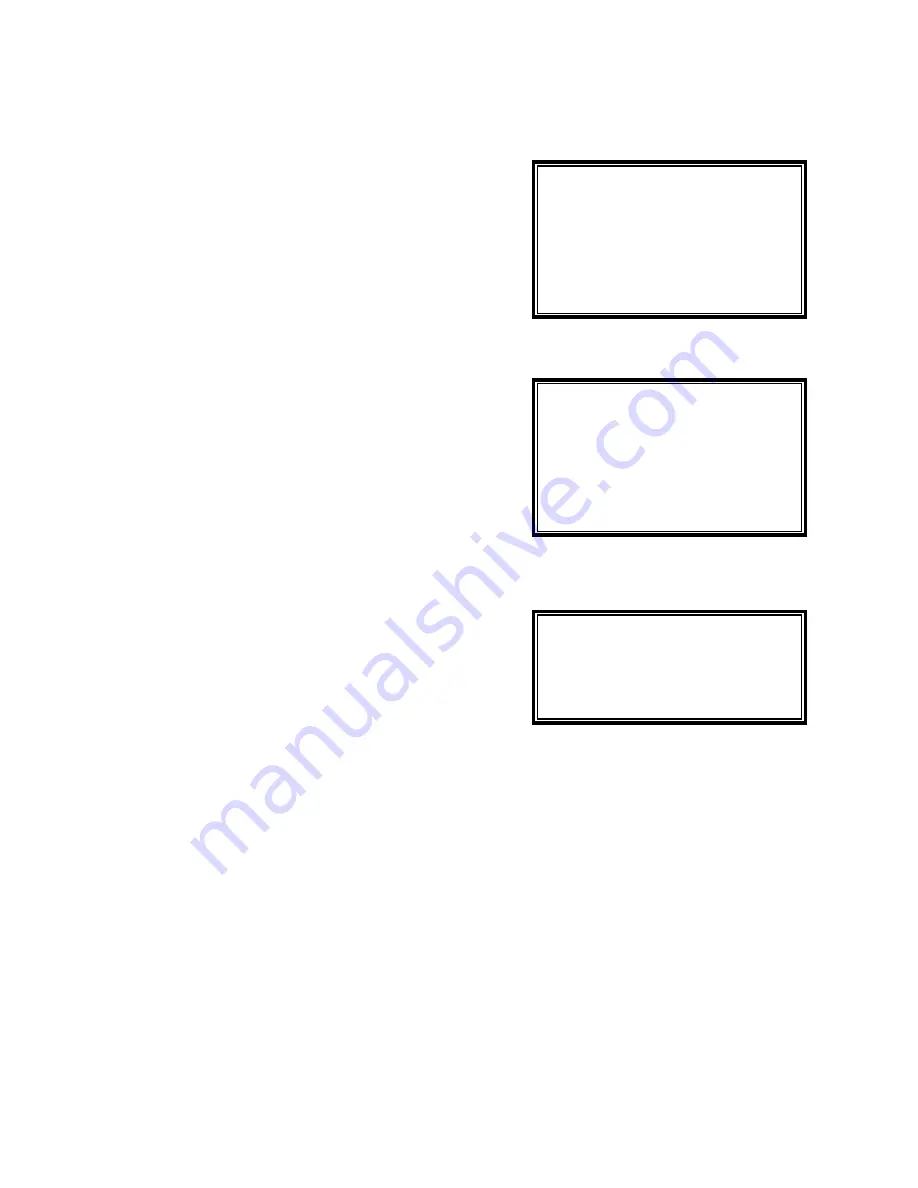
OPERATION
Page 47
MANUAL
CT
Controllers
7.1.1.3.2.4 - Bleed Lockout
The Bleed Lockout submenu 7.1.1.3.2.4 is used to prevent
bleed during - or immediately after - feeding of chemicals and
to specify pre-bleed and/or pre-pH feed operations.
Line 1 displays the bleed lockout time in percentage of feed
time. A value superior to 100% prevents bleed during and
after feed.
Line 2 displays the lock memory option to accumulate feed
lockout time until bleed is completed.
Line 3 and 4 display the pre-bleed option to reduce the risk of
deposits due to increasing conductivity or TDS level during a
lockout period. The pre-bleed can be specified for a length of
time and/or until a conductivity level is reached.
The Pre-pH option is used to adjust the pH level before
additive feed. The pH feed can be set for a length of time (line
5) and/or until a pH level is reached (line 6). The controller
maintains the pH level during the entire feed cycle.
7.1.2 - Time Limit
Line 2 shows the maximum amount of time in minutes that is
allowed for continuous feeding of the additive. This is
designed to alert the operator in case of a malfunction of the
chemical feeder.
7.1.3 - Run Time
The RUN TIME displays the time in minutes for current
activation and cumulative run time since last reset to zero.
To reset the cumulative run time, enter zero in the last column.
To reset only the current run time, turn the control mode off
and back on.
After the cumulative run time is reset, the TOTAL TIME
ALARM submenu (see submenu 7.1.3) is displayed to set the
Total Time Alarm option. It can be used to simulate a low
chemical level alarm by entering the number of minutes
needed to empty the chemical container: container volume
divided by feeder rate (i.e.110 min = 55 ga / 0.5 gpm)
7.1.4 - Booster/Single Shot
The Booster (Single Shot) function is used to schedule a
delayed one-time feed event (i.e. feeding the biocide at 1:00
AM for an hour). It is independent of the other control modes.
The Booster Submenu 7.1.4 allows selection of the date, start
time and duration of the feed event. Selection of line 4 leads to
the Bleed Lockout submenu 7.1.1.3.2.4.
Submenu 7.1.1.3.2.4
Submenu 7.1.3
Submenu 7.1.4
BLEED LOCKOUT
Lockout %
150
Lock memory
YES
Pre-bleed
min
10
Pre-bleed
uS 1900
Pre-pH
min
0
Pre-pH
pH
7.0
TOTAL ALARM TIME
Alarm if total
Feed time exceeds:
110 min
Enter 0 for no alarm
BOOSTER
Date
08/31/04
Start Time
21:00
Run Time
1:00
Bleed Lockout
YES