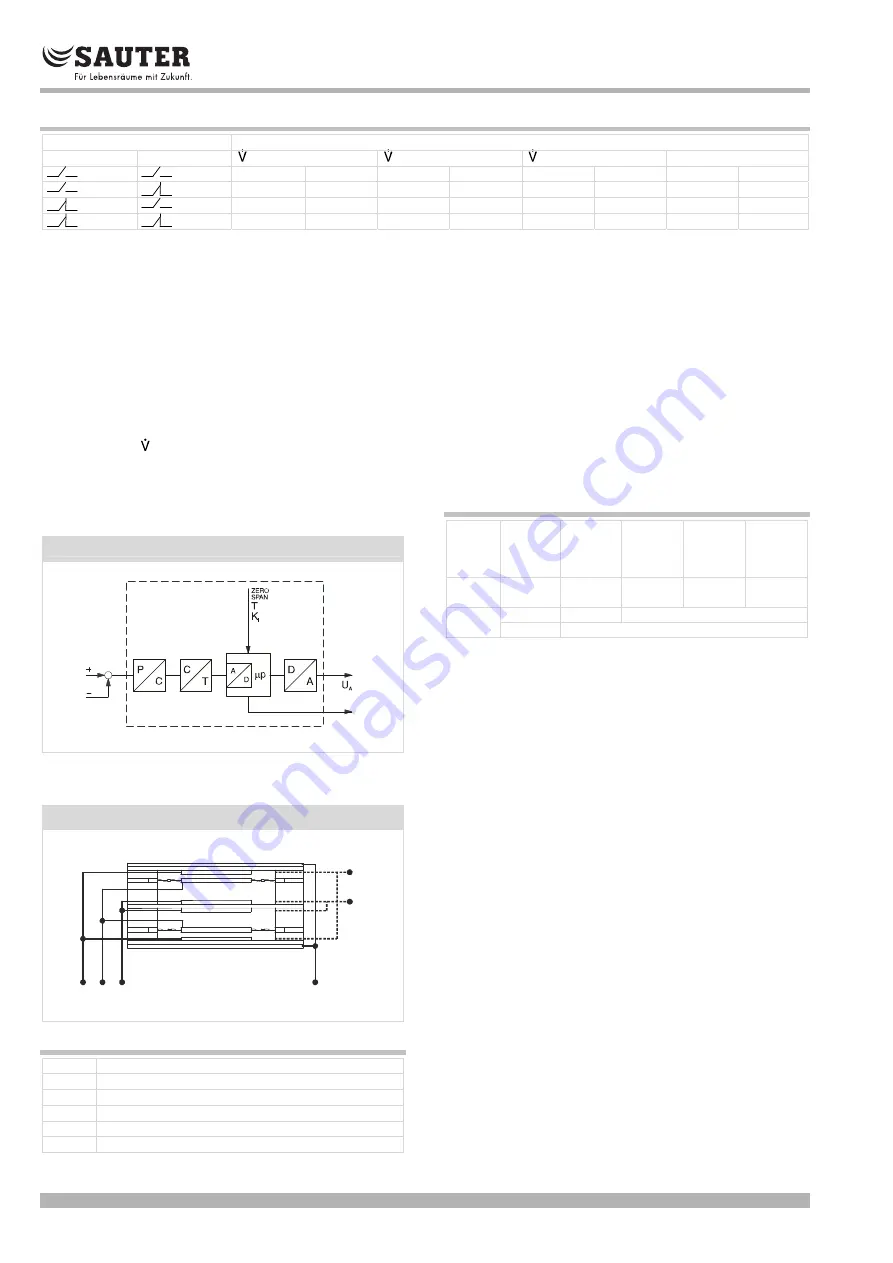
ASV115
Logic table for digital inputs
Configuration of connections
Function with factory setting
DI05 (c
qV.p.2
) DI04
(c
qV.p.1
)
var
min
max
Damper
closed
n. act.
n. act.
n. act. act.
act.
n.
act. act.
act.
n. act.
act.
n. act.
n.
act.
act. act. act. n.
act.
act.
n.
act.
act.
act.
n. act.
n. act.
n. act.
act.
act.
act.
act.
n.
act.
n. act.
act.
n. act.
n. act.
n. act.= connected switch or contacts are
not activated
, i.e. normally open contacts are open and normally closed are closed.
act. = connected switch or contacts are
activated
, i.e. normally open contacts are closed and normally closed are open.
In order to stabilise the sensor's measurement signal in case of
severely fluctuating pressure signals, the SAUTER CASE VAV
software can be used to set the filter time constant
continuously in
a range from 0 to 5.22 s. Zero can be reset as required by using the
zeroing function.
Sensor technology
The measuring sensor used in the VAV controller is a static double-
membrane sensor manufactured using PCB technology. Thanks to
its symmetrical structure with two measuring cells which are (in
principle) independent, the sensor is position-compensated and
can, therefore, be operated in any fitted position. The differential
pressure is evaluated using the differential capacitance measure-
ment method. The unique design ensures highly accurate meas-
urement at differential pressures of up to < 1 Pa, allowing precise
control of air volume at a differential pressure of 1 Pa. This enables
users to set low
min
values for reduced mode in order to save
energy.
Power supply connection
The drive can be operated with 24 V d.c. or a.c. Automatic connec-
tion recognition is available only in a.c. mode. In d.c. mode, the full
nominal torque of 10 Nm is available within the specified tolerances.
If the controller is operated with 24 V d.c., the following function
differs from a.c. operation, in relation to analogue inputs AI01 and
AI02:
Thanks to the principle of using a static measuring method, the
sensor can also be used to measure pumped media which contain
dust or are contaminated with chemicals.
Functions with 24 V d.c.
Connec-
tion
Para-
meterised
function
Circuit
connec-
tion
Function
range
0…10 V
Function
range
2…10 V
Function
freely
configur-
able
AI 01
Standard NC
1)
Vvar
2)
Damper
closed
3)
AI
NC
max. pos. shift if factor shift > 0
AI/AO 02
AO
not available
Sensor block diagram
6/13
www.sauter-controls.com
Bus
F
B
104
1
8
1) NC, not connected
2) It is recommended to put the setting for forced operation for LOW voltage additionally to
Vvar.
3) Connection is recognised as
LOW voltage
and, accordingly, the factory setting for
forced operation is performed; other parameters provide different behaviour.
After applying power, the working range of the damper drive is
determined automatically. For this purpose, the drive approaches
both limit stops and specifies the possible angle of rotation (factory
setting). The initialisation procedure in the event of a power failure
can be disabled by setting a parameter in the SAUTER CASE VAV
software tool.
The SAUTER CASE VAV software enables zeroing and setting of
damping factors by the user as required.
Sensor structure
RS-485 / SLC interface function
GND
Pn
Pp
Ac
Ap
An
B1
1
563
The VAV compact controller is fitted with an RS-485 interface which
is not galvanically separated. The baud rate used is 115.2 kbps,
which is a fixed setting. The SAUTER Local Communication (SLC)
protocol that is used specifies the master-slave bus access proce-
dure, with a maximum of 31 devices permitted in one network seg-
ment. The 32
nd
device is the parametering tool. The SAUTER CASE
VAV software is used to parameterise each individual device and to
configure the devices within the network segment. Physical access
to the bus system is gained either via the connection in the housing
cover or via three separate leads at the end of the cable.
CASE VAV function
The SAUTER CASE VAV software is available to parameterise the
air volume controller. This software tool enables you to configure all
the values required for operation via a comfortable user interface.
The connection is made via a USB interface on the PC/laptop and
via the jack on the drive, or via the RS-485 leads on the drive cable.
The drive parameterisation set comprises: software, including in-
stallation and operating instructions, fitting instructions, connection
plug, connection cable (length 1.2 m) and an interface converter for
the PC. The software is intended for use by OEM manufacturers,
commissioning and service technicians and experienced operators.
The following functions are available:
Key
Pp
Connection for higher pressure
Pn
Connection for lower pressure
Ac
Common pole flange of the differential capacitor
Ap
Positive pole flange
An
Negative pole flange
GND Earth
(ground)