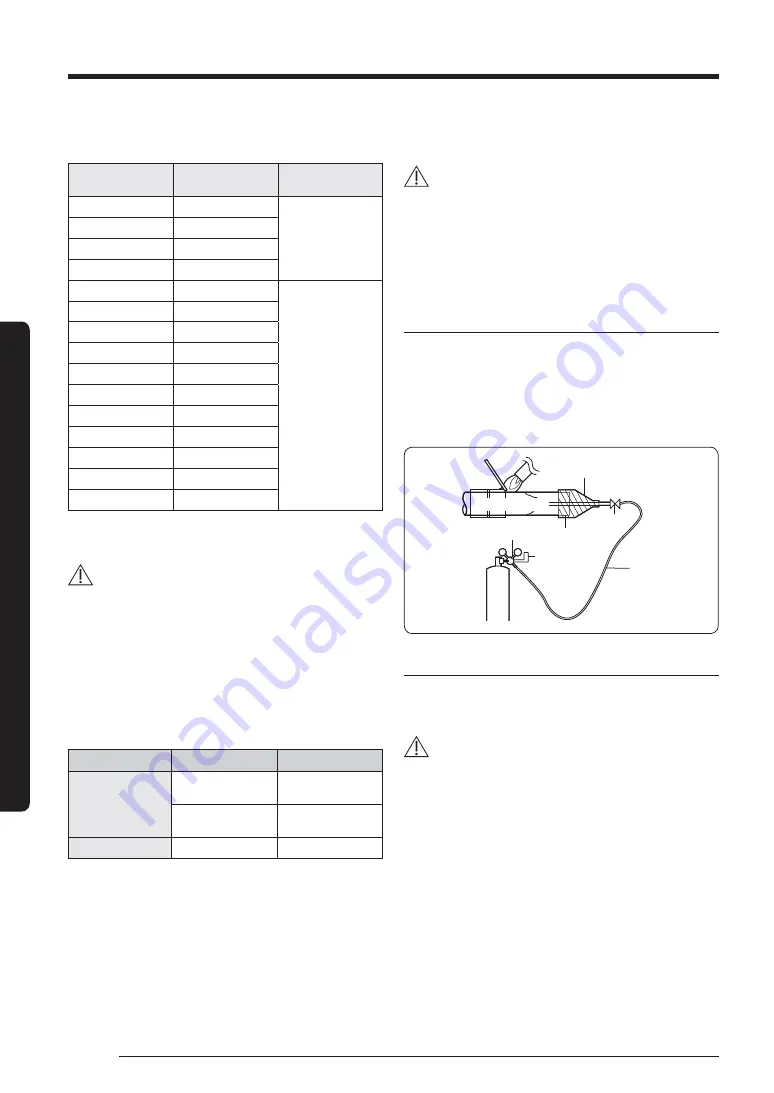
24
Refrigerant pipe installation
English
Instal
lation Pr
oc
edur
e
Temper grade and minimum thickness of
the refrigerant pipe
Outer diameter (mm)
Minimum thickness
(mm)
Temper grade
Ø 6.35
0.70
Annealed
Ø 9.52
0.70
Ø 12.70
0.80
Ø 15.88
1.00
Ø 19.05
0.90
Drawn
Ø 22.22
0.90
Ø 25.40
1.00
Ø 28.58
1.10
Ø 31.75
1.10
Ø 34.92
1.20
Ø 38.10
1.35
Ø 41.28
1.43
Ø 44.45
1.60
Ø 50.80
2.00
Ø 53.98
2.10
• The material specification (thickness) of the refrigerant pipes
must be in accordance with EU and/or local legislation and
standards.
CAUTION
•
For pipes larger than Ø 19.05, drawn type (C1220T-1/2H or
C1220T-H) type copper pipe must be used. If a annealed type
(C1220T-O) copper pipe is used, pipe may break due to its low
pressure resistance and cause personal injury.
Keeping refrigerant pipe
To prevent foreign materials or water from entering the pipe,
storing method and sealing method (especially during installation)
is very important. Apply correct sealing method depending on the
environment.
Exposure place
Exposure time
Sealing type
Outdoor
Longer than one
month
Pipe pinch
Shorter than one
month
Taping
Indoor
-
Taping
Refrigerant pipe welding and safety
information
CAUTION
• Important information for refrigerant pipe work.
– Make sure there is no moisture inside the pipe.
– Make sure there are no foreign substances and impurities
in the pipe.
– Make sure there is no leakage.
– Make sure to follow the instruction when welding or storing
the pipe.
Nitrogen flushing welding
• When welding the refrigerant pipes, flush them with nitrogen
gas as shown in the picture.
• If you do not perform nitrogen flushing when welding the
pipes, oxide may form inside the pipe. It can cause the damage
of the important parts such as compressor and valves etc.
• Adjust the flow rate of the nitrogen flushing with a pressure
regulator to maintain 0.05m
3
/h or less.
Welding part
Nitrogen gas
Ø 6.35 copper pipe
Stop valve
Taping
High pressure hose
Pressure regulator
Nitr
ogen
gas
Flowmeter
Direction of the pipe when welding
• Direction of the pipe should be headed downward or in a
sideways when welding.
• Avoid welding the pipe with pipe direction heading upward.
CAUTION
• When you test gas leakage after welding the pipes, use a
designated solution for gas leakage detection. If you use the
detection solution that includes sulfuric ingredient, it may
cause corrosion to the pipes.
Summary of Contents for AM AXV Series
Page 68: ......