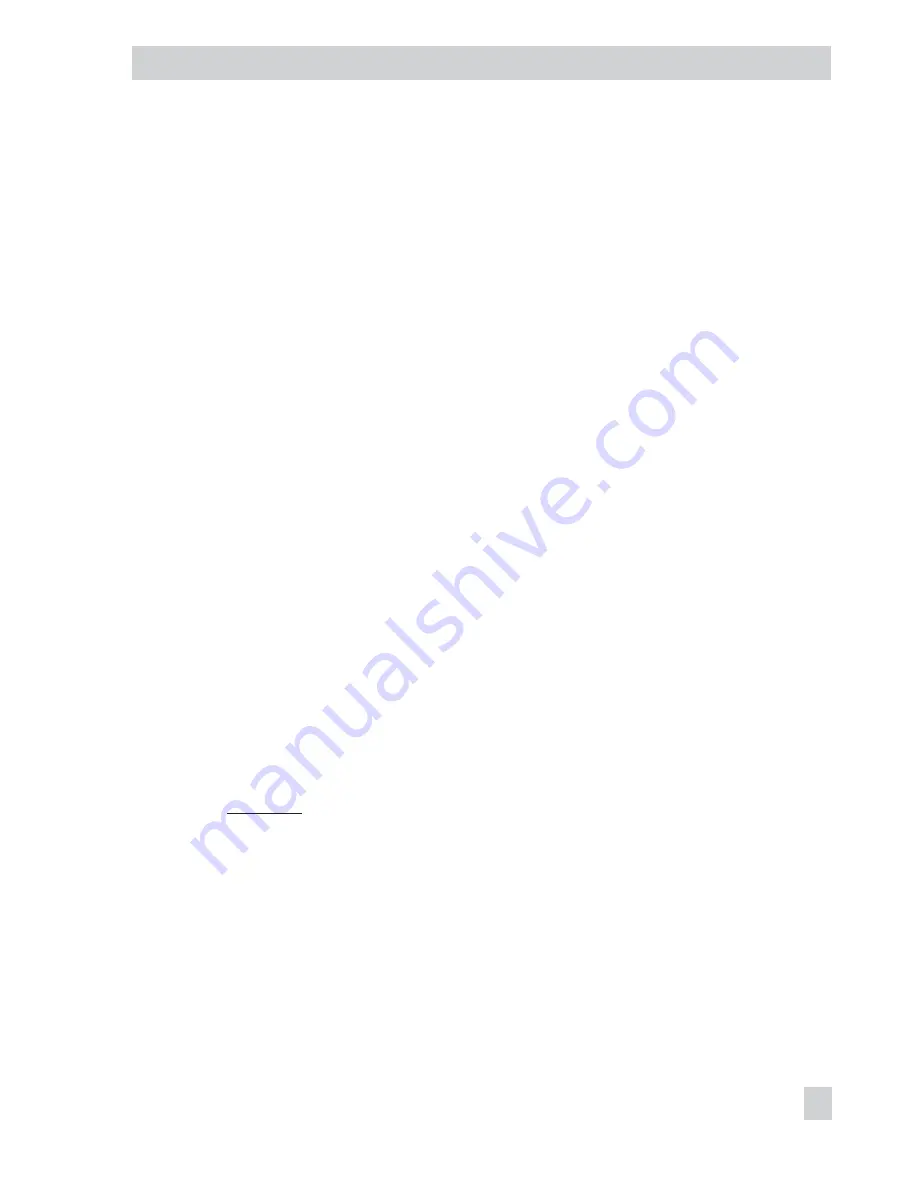
5.1.1 Signal pressure gauges
To monitor the supply air (Supply) and sig-
nal pressure (Output), we recommend that
pressure gauges be attached (see accesso-
ries in Tables 1 to 5).
5.1.2 Supply pressure
The required supply pressure (of supply air)
depends on the bench range and the actua-
tor's operating direction (fail-safe action).
The bench range is registered on the name-
plate either as spring range or signal pres-
sure range depending on the actuator.
The direction of action is marked
FA
or
FE
,
or by a symbol.
Actuator stem extends FA (AIR TO OPEN)
Fail-close (for globe and angle valves):
Required supply pressure = Upper bench
range value + 0.2 bar, minimum 1.4 bar.
Actuator stem retracts FE (AIR TO CLOSE)
Fail-open (for globe and angle valves):
For tight-closing valves, the maximum signal
pressure pst
max
is roughly estimated as fol-
lows:
pst
max
= F +
d
p
A
2
4
⋅ ⋅
⋅
π ∆
[bar]
d
= Seat diameter [cm]
∆
p = Differential pressure across the valve
[bar]
A
= Actuator diaphragm area [cm²]
F
= Upper bench range of the actuator
[bar]
If there are no specifications, calculate as
follows:
Required supply pressure =
Upper bench range value + 1 bar
5.1.3 Signal pressure (output)
The signal pressure at the output (Out-
put 38) of the positioner can be limited to
1.4, 2.4 or 3.7 bar in Code
16
.
The limitation is not activated [No] by de-
fault.
EB 8387-3 EN
35
Connections
Summary of Contents for TROVIS 3731-3
Page 89: ...EB 8387 3 EN 89...
Page 90: ...90 EB 8387 3 EN...
Page 91: ...EB 8387 3 EN 91...
Page 92: ...92 EB 8387 3 EN...
Page 93: ...EB 8387 3 EN 93...
Page 94: ...94 EB 8387 3 EN...
Page 95: ...EB 8387 3 EN 95...
Page 96: ...96 EB 8387 3 EN...
Page 97: ...EB 8387 3 EN 97...