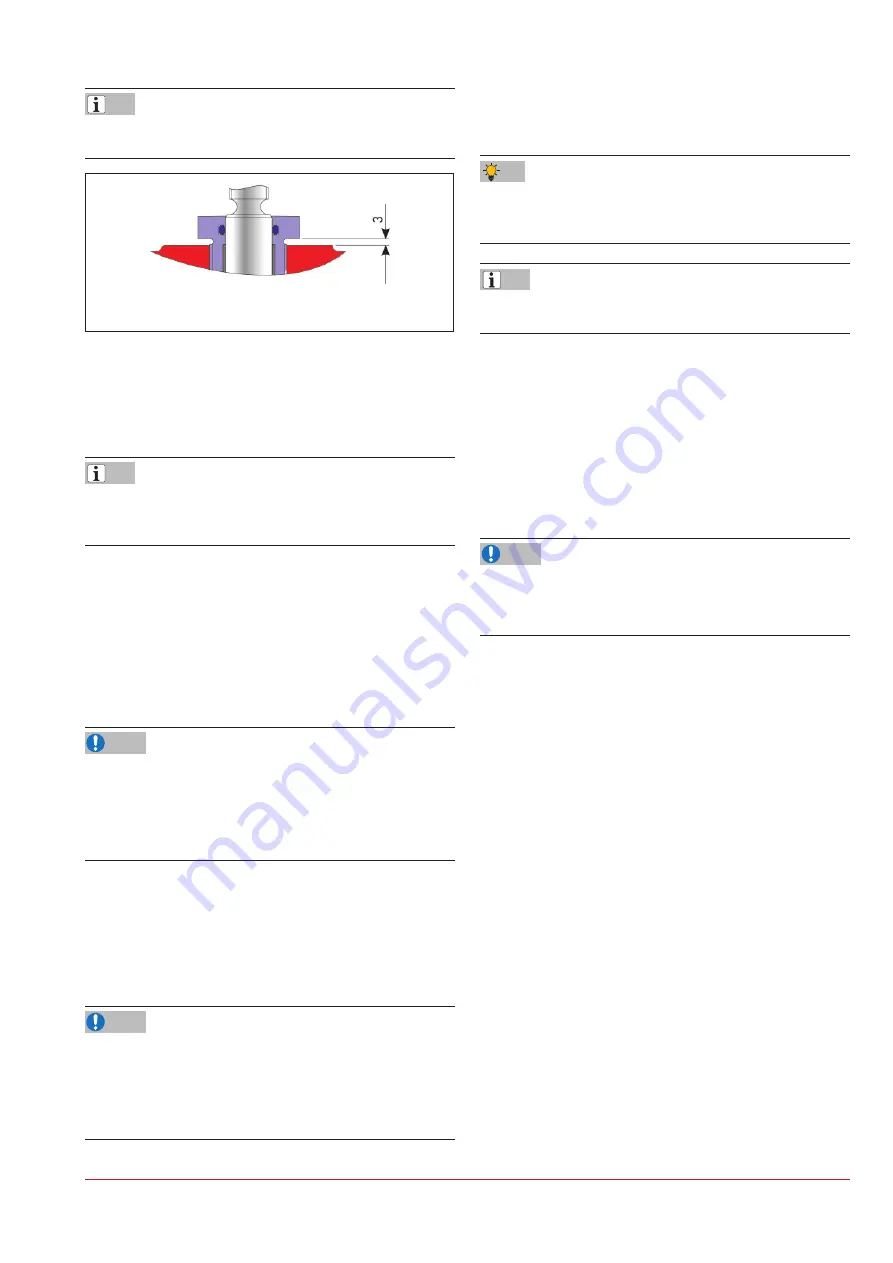
3-5
EB 01b_EN
February 2022 edition
Subject to technical changes
Design and principle of operation
Do not tighten the stuf
fi
ng box, the distance between the collar of
the stuf
fi
ng box and the bonnet
fl
ange must be 3 mm!
Figure
|
3-2:
Adjustable stuf
fi
ng box
Ö
Seal the stuf
fi
ng box with a dot of red paint.
3.5.2
Assembly of the valve from DN
|
80 /
NPS3, manufactured before 2006
The assembly of the valves up to DN 50 / NPS2 manufactured
before 2006 is identical to the valves manufactured after 2006,
see Chapter 3.5.1
3.5.2.1 Valve body assembly
Ö
Clamp the valve body (1) with the
fl
ange in a vice so that the
bearing area of the seat is easily reached.
Ö
Screw in the PTFE seat (3) using a suitable special tool into
the thread of the body (1). For the tightening values of the
seat, see Table 15-2 in Chapter “15.1.1 Tightening torques”.
Damage to the valve due to improper assembly
The thread on the seat and in the valve are delicate and can be
damaged
Ö
Do not twist the seat when screwing in and do not damage
the thread.
Ö
Rework the seat inner diameter to size.
3.5.2.2 Assembly of the stem
Ö
Push the retainer ring (22) from the short thread side into the
groove of the stem (12).
Damage to the parts of the stem sealing in contact with media
due to unsuitable grease.
Ö
When assembling the stem, bellows, plug and all other parts
of the stem sealing in contact with media, only use water-free
grease (e. g. halocarbon).
Info
Info
NOTE
NOTE
Ö
Grease the stem (12) on the bottom thread.
Ö
Screw the bellows (5) with a preassembled washer and bush-
ing onto the greased thread of the stem (12).
Due to the sliding property of the PTFE, we recommend using em-
ery cloth to prevent the bellows from sliding when screwing it on-
to the stem.
To make it easy to push on the plug stem, make a small notch in
the bellows to let air escape.
Ö
Push the plug (4) onto the bellows (5).
Ö
Secure the connection between the plug and bellows with a
PTFE cord (6) inserted as far as possible. Use a sharp knife to
cut off the remaining part of the cord that projects.
3.5.2.3 Assembly of the bonnet
fl
ange
Ö
Clamp the bonnet
fl
ange (2) with the stem guide facing down
in a vice.
Damage to the bonnet
fl
ange due to improper handling!
Ö
Do not damage the bonnet
fl
ange, especially the thread on
the stem end.
Ö
Apply Loctite on the Glycodur bushings (27 and 28).
Ö
Insert the Glycodur bushing (27) with a suitable pin as far as
possible into the stem guide.
Ö
Push in the Glycodur collar bushing (28) as far as possible.
Ö
For further assembly, place the bonnet
fl
ange (2) with the
fl
ange side on a clean surface at a working height so that the
upper opening is easy to reach.
Ö
Push in the V-ring packing (15) V-pressure ring, PTFE V-rings
and
fi
nal ring in the correct order into the intended bore. Re-
fer to the drawing Figure 3-3 for the arrangement of the
V-ring packing.
Ö
Insert the set of spring washers (16). Refer to the drawing
Figure 3-3 for the arrangement of the spring washers.
Tip
Info
NOTE
Summary of Contents for EB 01b
Page 28: ...5 6 EB 01b_EN February 2022 edition Subject to technical changes Installation...
Page 30: ...6 2 EB 01b_EN February 2022 edition Subject to technical changes Start up...
Page 32: ...7 2 EB 01b_EN February 2022 edition Subject to technical changes Operation...
Page 36: ...8 4 EB 01b_EN February 2022 edition Subject to technical changes Malfunction...
Page 40: ...10 2 EB 01b_EN February 2022 edition Subject to technical changes Decommissioning...
Page 42: ...11 2 EB 01b_EN February 2022 edition Subject to technical changes Removal...
Page 48: ...13 2 EB 01b_EN February 2022 edition Subject to technical changes Disposal...
Page 50: ...14 2 EB 01b_EN February 2022 edition Subject to technical changes Certificates...
Page 51: ...14 3 EB 01b_EN February 2022 edition Subject to technical changes Certificates...
Page 52: ...14 4 EB 01b_EN February 2022 edition Subject to technical changes Certificates...
Page 53: ...14 5 EB 01b_EN February 2022 edition Subject to technical changes Certificates...
Page 54: ...14 6 EB 01b_EN February 2022 edition Subject to technical changes Certificates...
Page 61: ...EB 01b_EN February 2022 edition Subject to technical changes...
Page 62: ...EB 01b_EN February 2022 edition Subject to technical changes...
Page 63: ...EB 01b_EN February 2022 edition Subject to technical changes...